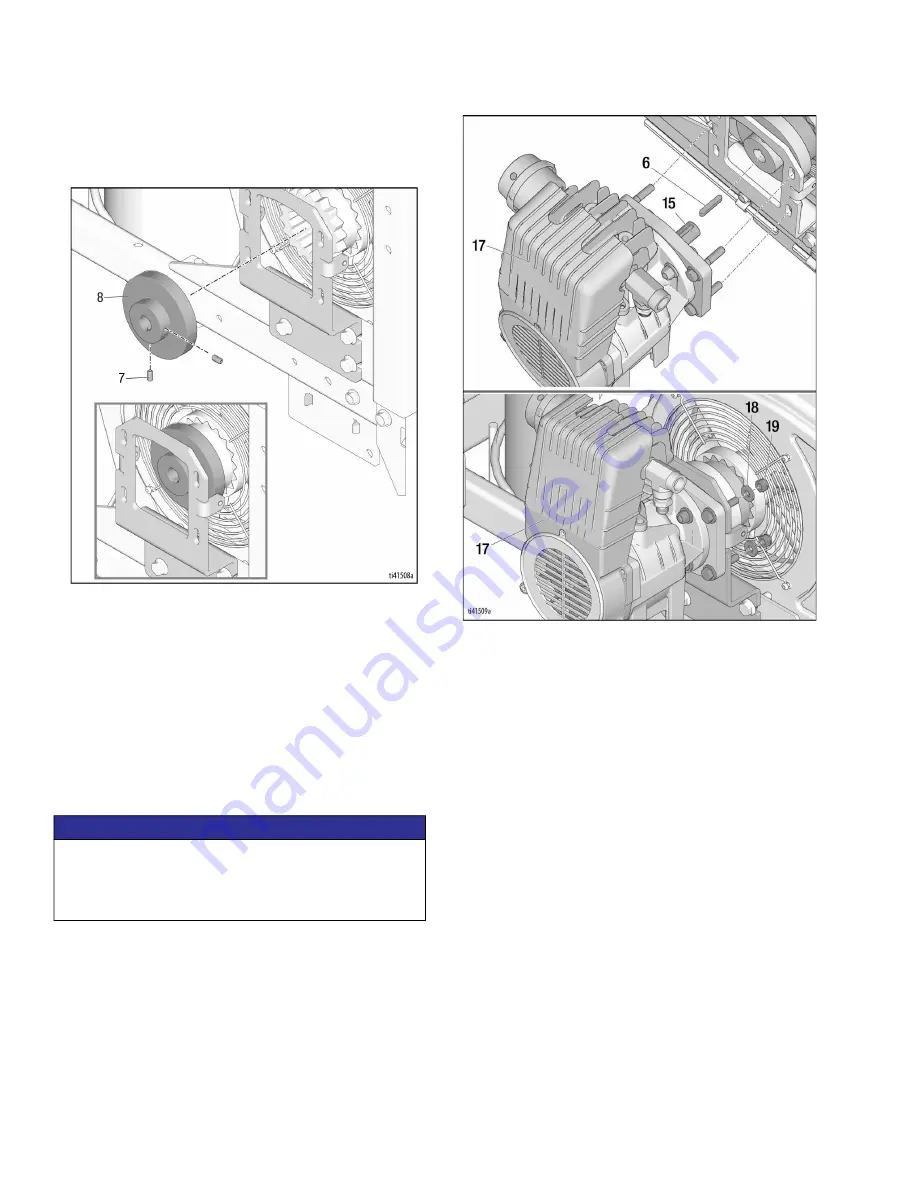
LL200 Compressor Installation
12
332230T
16. Start two set screws (7) into second coupler (8).
Slide coupler (8) over flex insert (9). Coupler (8)
should stay in position, if not it may need to be held
until the next step.
17. Ensure keyway on coupler shaft (15) is on top,
rotate as necessary. Place second key (6) in
keyway of coupler shaft (15). Align keyway in
coupler (8) to receive coupler shaft (15) and key (6).
Aligning all four studs (16) with associated vertical
slots, slide compressor assembly (17) into
mounting bracket so that coupler shaft (15) inserts
into coupler (8), ensure key (6) stays in place. Install
four washers (18) and four nuts (19) onto four studs,
tighten until slightly loose to allow for vertical
adjustment.
18. Horizontal Alignment: hold compressor assembly
(17) such that when viewed from above both
couplers (8) and flex insert (9) are aligned axially.
When properly aligned, tighten mounting bracket
bolts (11) to frame to 23-27 ft-lbs (31-37 N•m).
Horizontal alignment is now complete.
NOTICE
Performing the following step incorrectly may result in
improper alignment of the two rotating couplers. This
may cause premature wear and require replacement
of the flex insert (9).