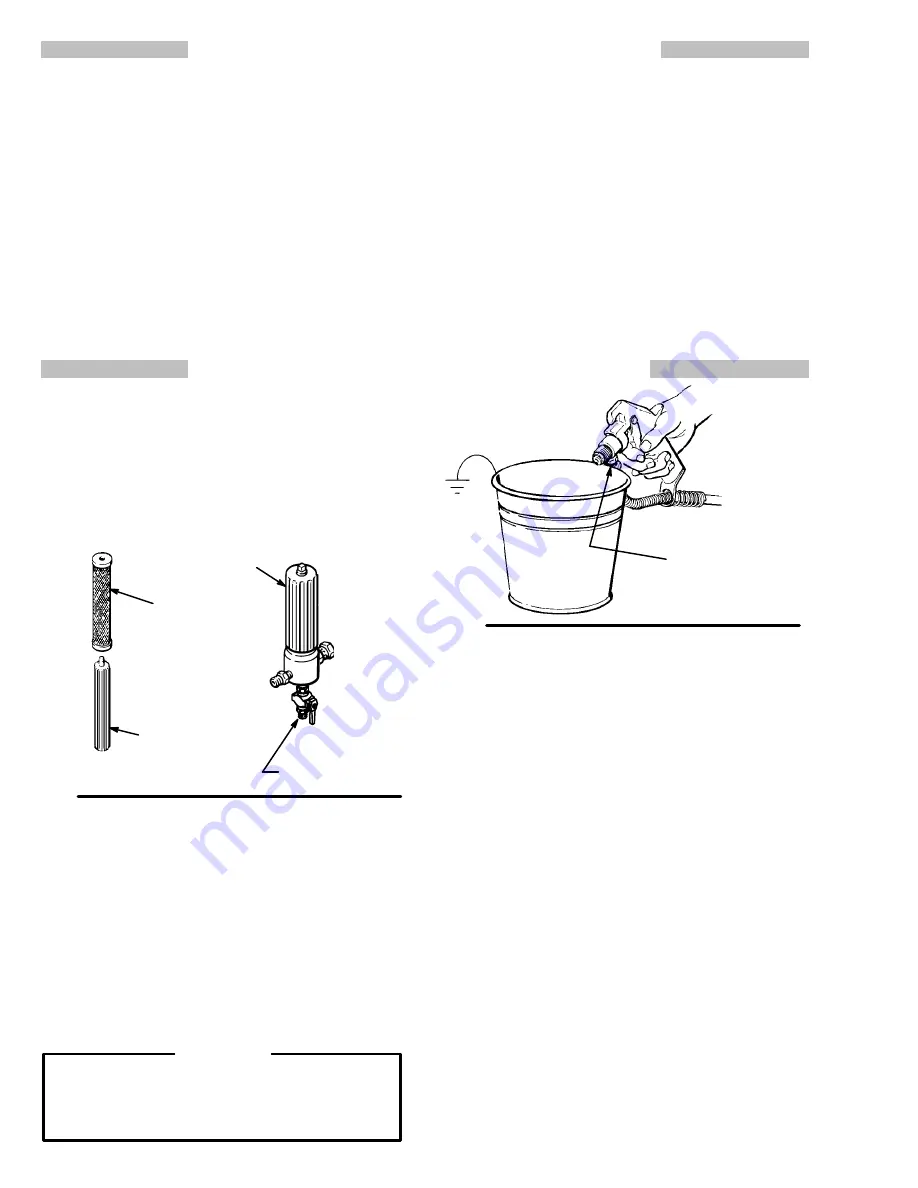
FLUSHING GUIDELINES – WHEN TO FLUSH
1.
New Sprayer . The sprayer was factory tested in
lightweight oil which was left in to protect pump parts.
Before using water–base paint , flush with mineral
spirits, then warm, soapy water , and then clean
water.
Before using oil–base paint, flush with mineral spir-
its.
2.
Changing Colors. Flush with a compatible solvent.
3.
Changing from water–base to oil–base paint.
Flush with warm, soapy water, then mineral spirits.
4.
Changing from oil–base to water–base paint.
Flush with mineral spirits, then warm, soapy water ,
and then clean water.
5.
Storage. Flush as indicated below , shut of f the
sprayer, open the pressure drain valve to relieve
pressure and leave it open.
Water–base paint: flush with water , then mineral
spirits. Leave the system filled with mineral spirits.
Oil–base paint: flush with mineral spirits.
6.
Startup after storage. Before using water–base
paint, flush out mineral spirits with soapy water and
then clean water. When using oil–base paint, flush
out the mineral spirits with the paint to be sprayed.
FLUSHING GUIDELINES – HOW TO FLUSH
1. Relieve pressure. See the
Pressure Relief Proce-
dure Warning on page 11.
2. Remove the filter bowl and screen; see manual
307–273. Clean the screen separately and install the
bowl without the screen to flush it. See Fig 3.
Fig 3
PRESSURE
DRAIN VALVE
FILTER
BOWL
SCREEN
FILTER
SUPPORT
3. Close the pressure drain valve.
4. Pour one–half gallon of compatible solvent into a
grounded metal pail. Put the suction tube in the pail.
5. Remove the spray tip from the gun, if it is installed.
6. Turn the pressure adjusting knob all the way counter-
clockwise to lower the pressure setting.
WARNING
To reduce the risk of static sparking and splashing
when flushing, always remove the spray tip from the
gun, and hold a metal part of the gun firmly to the
side of grounded metal pail.
Fig 4
MAINTAIN FIRM
METAL TO METAL
CONTACT WHEN
FLUSHING
7. Hold a metal part of the gun firmly against a metal
waste container.
See Fig 4. Hold the trigger open,
turn on the sprayer, and slowly increase the pressure
just until the sprayer starts. Keep the gun triggered
until all air is forced out of the system and the solvent
flows freely from the gun. Release the trigger and en-
gage the gun safety latch.
NOTE: If the pump is hard to prime, open the drain valve.
When fluid comes from the valve, close it. Pro-
ceed as in Step 7.
8. Remove the suction tube from the pail. Disengage
the gun safety latch and trigger the gun to force sol-
vent from the hose. Do not run the pump dry for more
than 30 seconds to avoid damaging the pump pack-
ings! Relieve pressure.
9. Remove the suction tube and strainer and clean
them separately . Normal flushing does not ade-
quately clean these parts.
10. Leave the pressure drain valve open until you are
ready to use the sprayer again. If the screen was re-
moved, unscrew the filter bowl and reinstall the clean
screen. Reinstall the bowl, hand tight only.
11. If you flushed with mineral spirits and are going to use
a water–base paint, flush with soapy water and then
clean water. Relieve pressure.
Summary of Contents for Hydra-Spray EH 433 GT 226-432 L Series
Page 26: ...NOTES...
Page 27: ...NOTES...