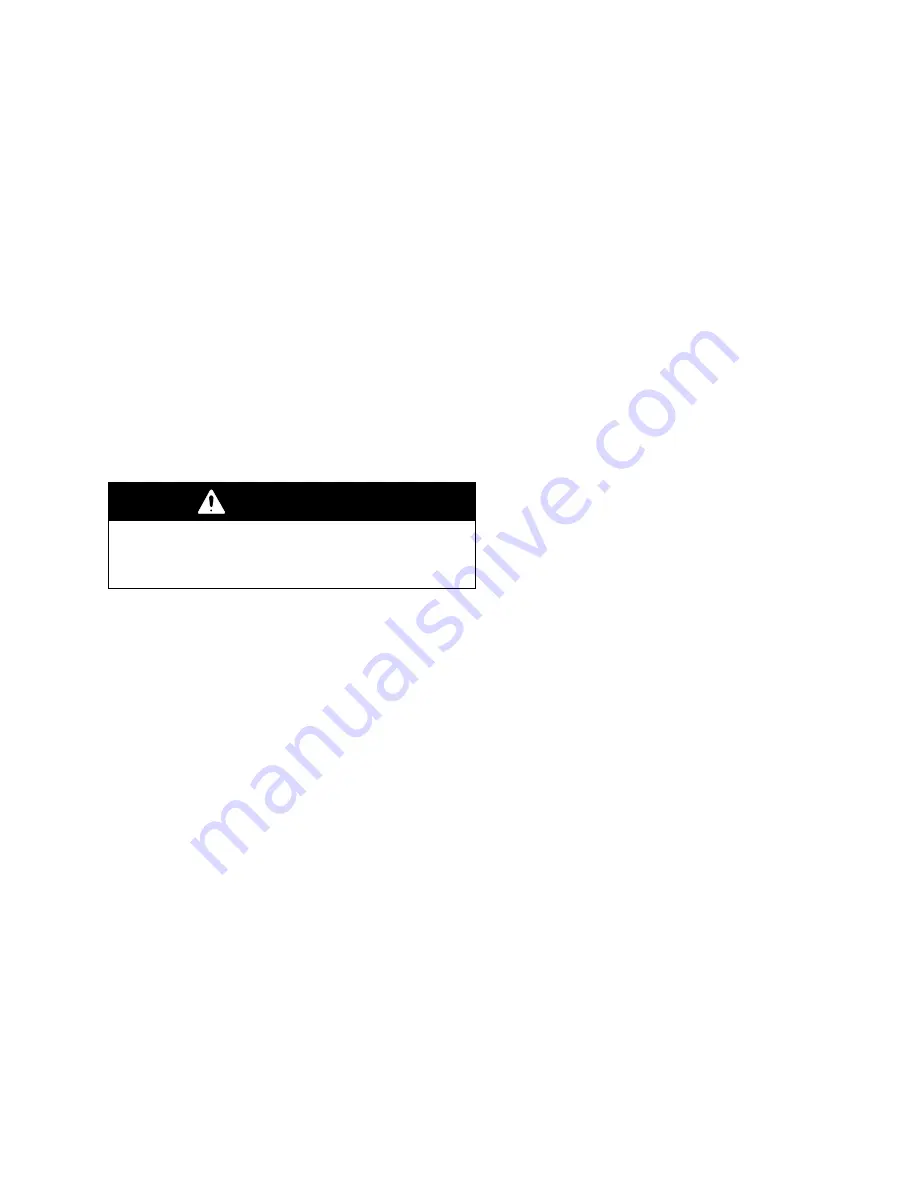
307132
13
Operation
Care of the Pump
Never allow the fluid supply containers to run dry of the
fluid being pumped. A dry container allows air to be
pumped into the system and causes incorrect propor-
tioning. Also, one dry pump will quickly accelerate to a
high speed, possibly damaging itself and the displace-
ment pump(s) because it causes a pressure rise in the
other pump. If a supply container is dry, stop the pump
immediately, refill the container, and prime the system.
Be sure to eliminate all the air from the system.
NOTE:
The pump runaway valve recommended in the
Installation
section will shut off the air supply to the
pump if the pump accelerates beyond the pre-adjusted
setting.
WARNING
To reduce the risk of serious injury whenever you
are instructed to relieve pressure, always follow the
Pressure Relief Procedure
on page 10.
Keep the throat packing nuts filled with TSL, and check
the tightness of the packing nut weekly. The packing
nut should be tight enough to prevent leakage; no
tighter. Too tight an adjustment will cause the packings
to bind or wear prematurely and leak. Relieve the pres-
sure before adjusting the packing nut.
Observe the pot life limit. Flush the mixed fluid out of
the mixer, dispensing lines and equipment before it
hardens. Flush the complete system, when necessary
to prevent the fluids from hardening in the equipment
and hoses. Check the fluid manufacturer’s instructions
for fluid shelf life, and flush the entire system before
this time is reached. Flush the system with a compat-
ible solvent as explained on page 11.
You should use a nitrogen regulator kit to protect the
fluid in the supply containers from moisture that can
crystallize the fluid and cause the ball checks to mal-
function. See
Accessories
.
With heavy fluids, flushing solvents could channel
through the fluid, leaving a coating of fluid on the inside
of the hoses. Disconnect the hoses and clean the fluid
out with a rag and wire or a ramrod type cleaner, or
use a solvent and air purge to agitate the solvent, and
flush until the mixer, hose and gun/dispensing valve
are clean.
Summary of Contents for BULLDOG HYDRA-CAT 208958
Page 17: ...307132 17 Notes...
Page 23: ...307132 23 Notes...