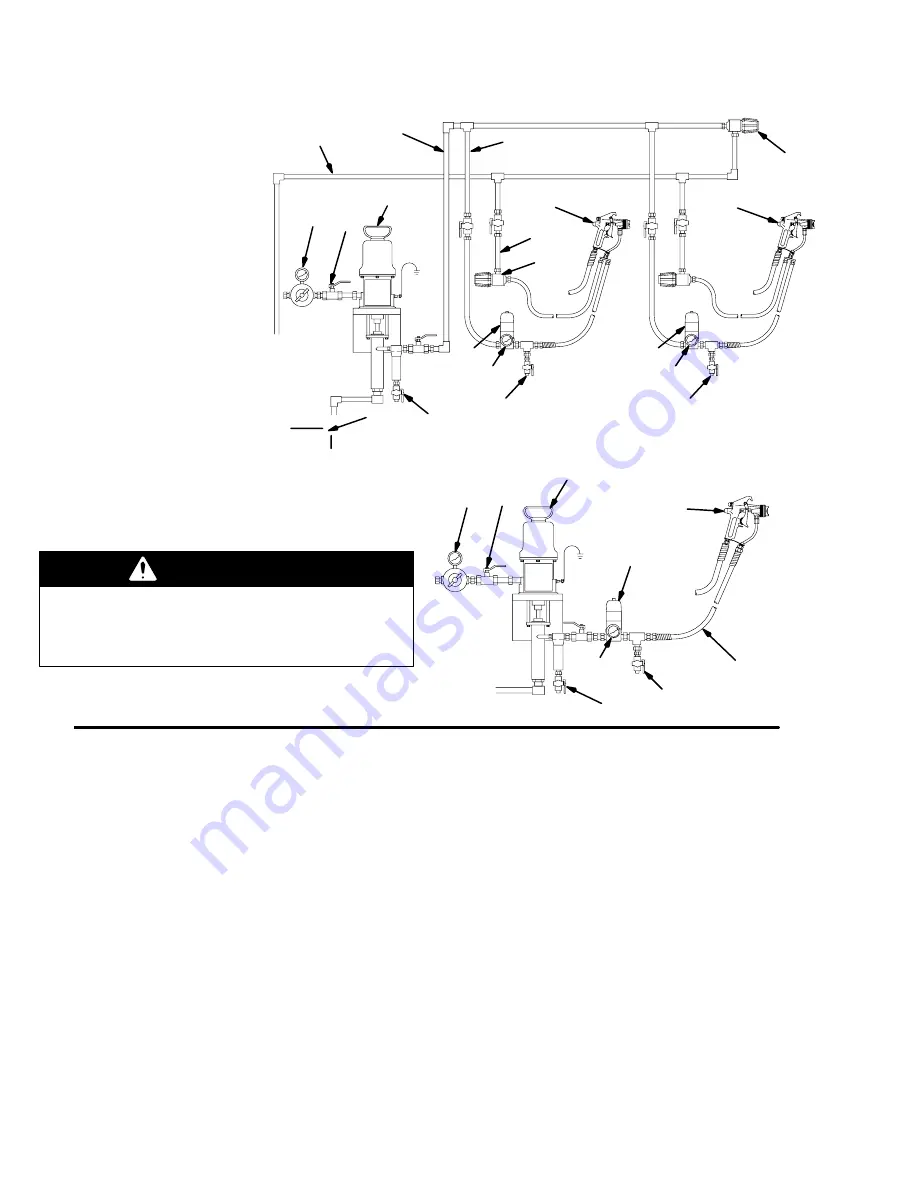
6
308647
Installation
H
Multiple Circulating Spray Station
Key
A Air regulator
B Bleed-type master air valve
C Pump
D Fluid filter and drain valve
E
Main fluid supply line
F
Gun fluid supply line
G Fluid regulator
with fluid pressure gauge (H)
H Fluid pressure gauge
J
Air-assisted airless spray gun
K Back pressure valve
L
Fluid return line
M Main circulating line
N Fluid supply container
P
Drain valve
A
B
C
D
E
F
J
K
M
K
L
A
B
C
G
D
J
Single Direct Spray Station
G
N
F
Fig. 1
06461
J
P
G
P
06462
P
H
H
WARNING
Do not use PTFE tape on pipe threads. Such use
could cause a hazardous condition due to loss of
grounding continuity. Also, if pieces of the tape break
off, the function of the regulator could be affected.
The installations shown in Fig. 1 are only a guide for
selecting and installing a circulating or direct system;
they are not actual system designs. Contact your
Graco distributor for assistance in designing a system
to suit your needs.
NOTE: Before you install the regulator, thoroughly
flush the system to remove metal chips and other
contaminants. A fluid filter (D) of 60-mesh or finer
should always be installed upstream of the regulator.
Connections
Install the fluid regulator (G) in the spray gun fluid
supply line (F), as shown in the typical installation
drawings on this page. Connect only one spray gun
or dispensing valve to each fluid regulator.
Apply pipe sealant to the male pipe threads, and
connect the fluid supply line (F) to the fluid regulator’s
3/8 npt(f) inlet. Connect the line from the gun (J) to the
fluid regulator’s 3/8 npt(f) outlet. Install the gauge or
plug into the 1/4 npt(f) gauge port.
Make sure the direction of fluid flow agrees with the IN
and OUT markings on the regulator body.
Flush the System
The regulator was tested in lightweight oil. Flush the
entire system with a solvent compatible with the fluid
being dispensed. Then test the system.
Mounting Bracket
A Mounting Bracket is available for mounting the
regulator. Order Part 222515 for the bracket and
mounting hardware.
Summary of Contents for 238889
Page 5: ...5 308647 Notes...
Page 22: ...22 308647 Notes...