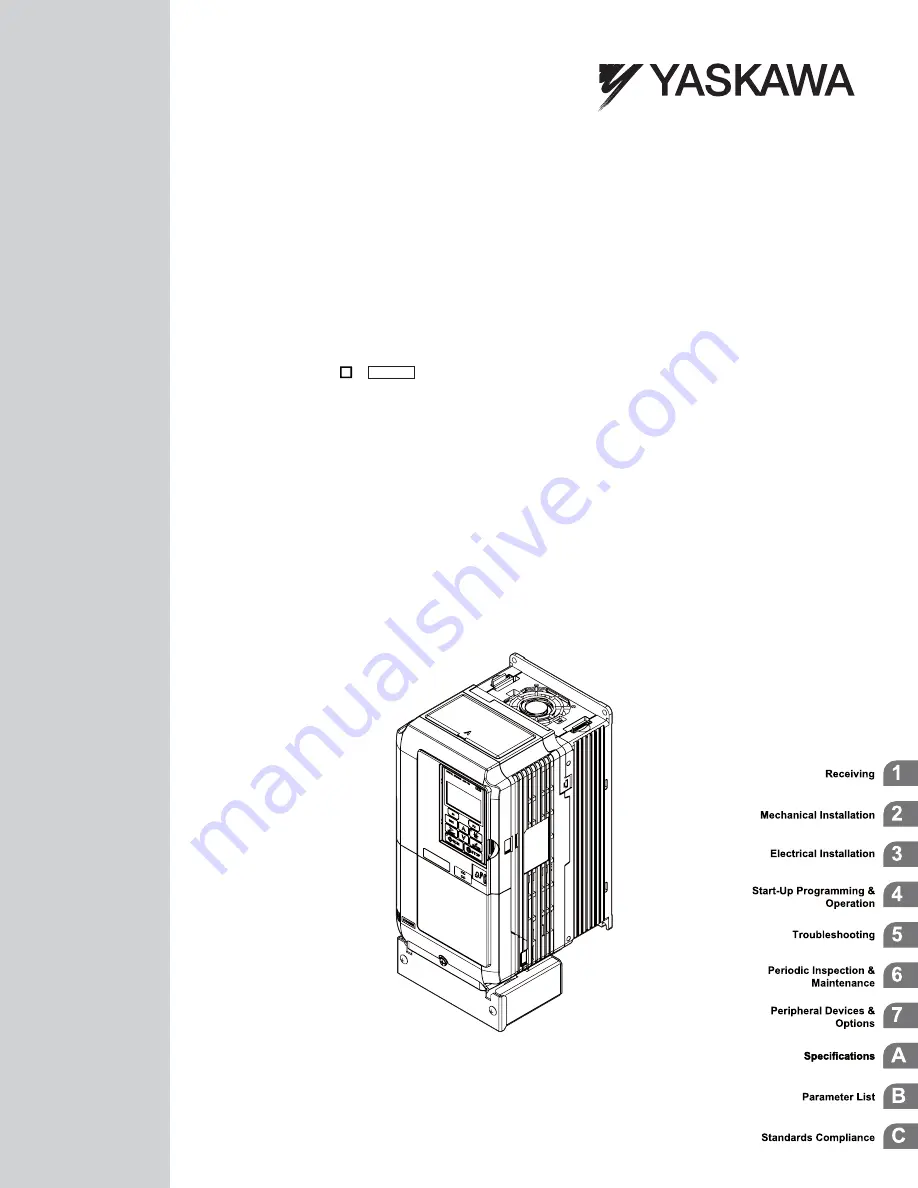
YASKAWA AC Drive P1000
Industrial Fan and Pump Drive
Quick Start Guide
MANUAL NO. TOEP YAIP1U 01B
To properly use the product, read this manual thoroughly and retain
for easy reference, inspection, and maintenance. Ensure the end user
receives this manual.
Type: CIMR-PU A
Models: 200 V Class: 3/4 to 175 HP ND
400 V Class: 3/4 to 1000 HP ND
600 V Class: 2 to 250 HP ND
Summary of Contents for P1000
Page 255: ......