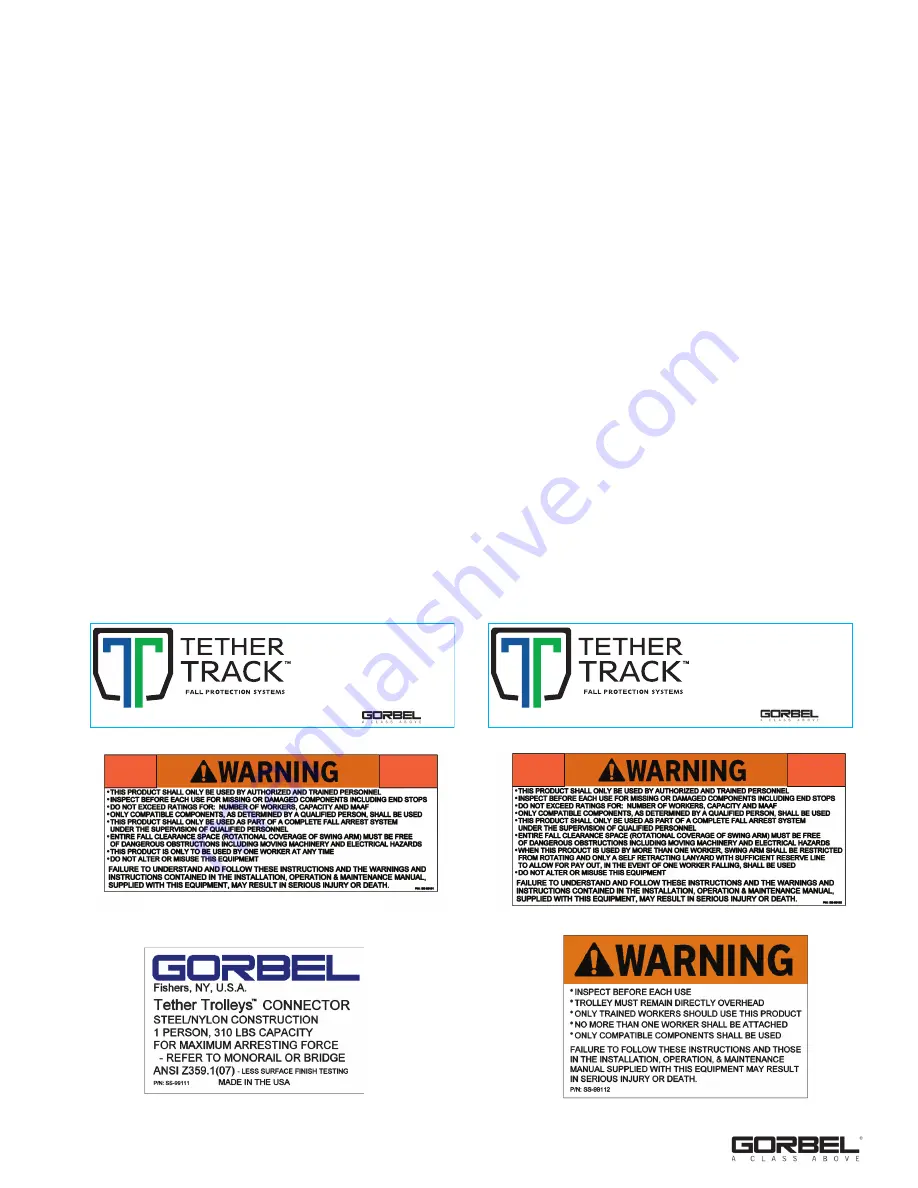
FALL ARREST SYSTEM REQUIREMENTS (CONT.)
Ratings:
Swing Arm labels contain the following four ratings:
1) Maximum number of workers. This will typically be 1 or 2 and represents the total number of workers that
may simultaneously use the Swing Arm.
Note:
Each Tether Track® trolley may have only one worker attached.
2) Maximum worker weight. This is limited to 310 pounds and represents the maximum combined tool and
body weight of each worker. Using fall arrest equipment has an inherent risk of injury. When used properly,
a SRL and a Swing Arm will greatly minimize impact forces experienced by the worker. However, if there
are any concerns that a user may not be able to tolerate the shock load during a fall arrest, they must not
use this equipment. Concerns with exceeding this capacity are due to the higher internal forces that larger
mass organs will generate and the increased risk of suspension trauma from the larger quantity of stale
blood that the body must reprocess.
3) Maximum average arresting force. This is typically 900 pounds. This must be greater than or equal to the
MAAF rating of an ANSI Z359.13 lanyard or a Z359.14 SRL that is being connected to the Swing Arm. For
other lanyards and SRLs, the Swing Arm’s maximum average arresting force rating must be greater than or
equal to the maximum arresting force rating of the connected lanyard or SRL.
Note:
the static proof test load
must be based on the maximum average arresting force rating of the Swing Arm multiplied by the maximum
number of workers. Each trolley must have only one worker’s MAAF applied to it.
4) Maximum arresting force of 1800 lbs. This is rated in conjunction with the maximum average arresting force
rating used in ANSI Z359.13 and .14.
Note:
this rating can only be dynamically proof tested without causing
permanent deformation to the Swing Arm.
LABELS
Swing Arm Labels
Trolley Labels
19
10/12 Rev. E
Cyan
Part Number: SS-99153
Ticket Number: 281386
Size: 28“W x 8”T
Corner Radius:
Artist: GSS
Date: 7/24/12
8/16
8/24 8/28
PMS 355
PMS 647
Black
28”
8”
COMPLIES WITH OSHA AND ANSI Z359.1 REQUIREMENTS
P/N: SS-99153
Fishers, NY, U.S.A.
MAXIMUM AVERAGE
ARRESTING FORCE
PER WORKER
PER WORKER
MAXIMUM
ARRESTING FORCE
310
900
1800
1 WORKER MAXIMUM
LBS CAPACITY
EACH WORKER WITH TOOLS
LBS
LBS
Manufactured by
Cyan
Part Number: SS-99118
Ticket Number: 281389
Size: 28“W x 8”T
Corner Radius:
Artist: GSS
Date: 7/24/12
8/16
8/24
8/28
PMS 355
PMS 647
Black
28”
8”
COMPLIES WITH OSHA AND ANSI Z359.1 REQUIREMENTS
P/N: SS-99118
Fishers, NY, U.S.A.
MAXIMUM AVERAGE
ARRESTING FORCE
PER WORKER
PER WORKER
MAXIMUM
ARRESTING FORCE
310
900
1800
2 WORKERS MAXIMUM
LBS CAPACITY
EACH WORKER WITH TOOLS
LBS
LBS
Manufactured by
Trolley label
Trolley warning label
One worker Swing Arm label
Two worker Swing Arm label
Swing Arm one worker warning label
Swing Arm two worker warning label