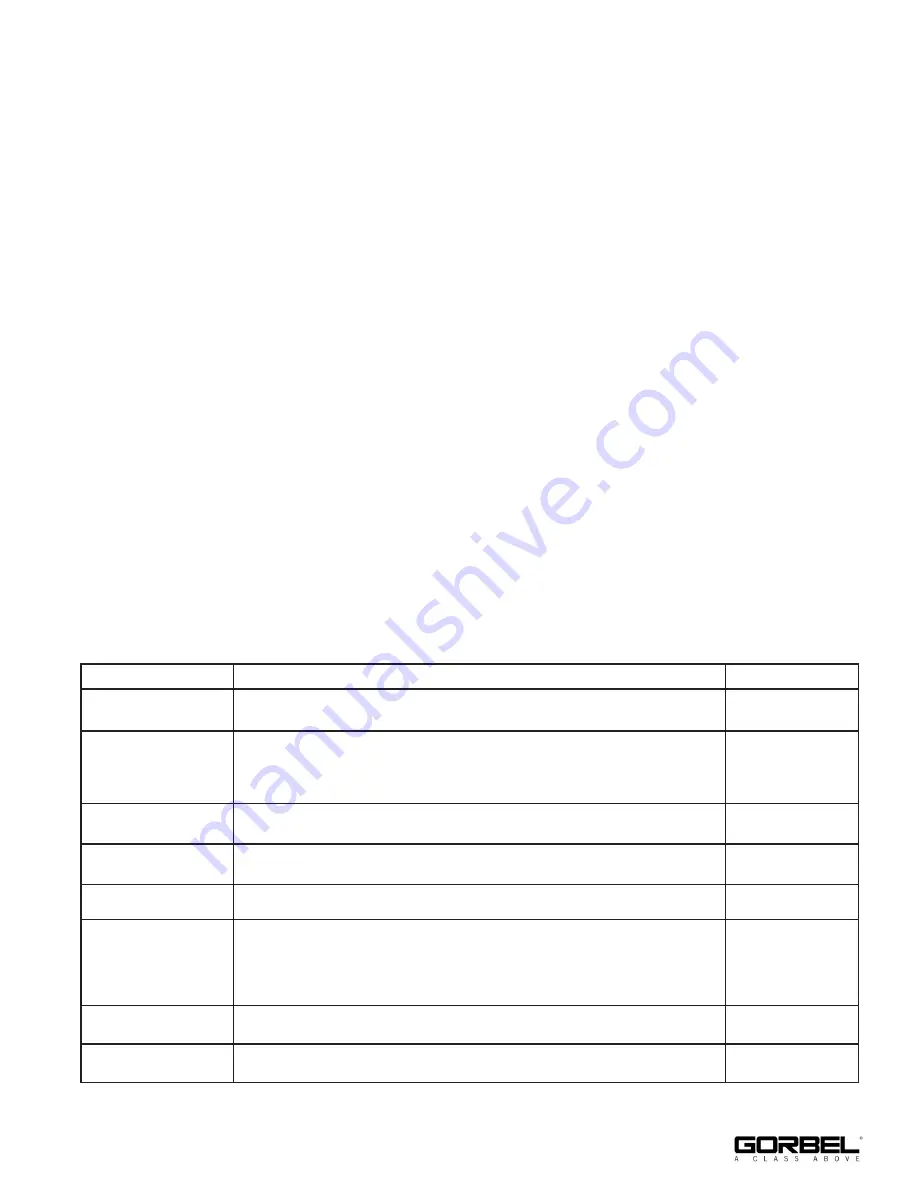
21
11/2018
PERIODIC INSPECTION AND LUBRICATION RECOMMENDATIONS
The following is a checklist to be followed in performing periodic inspections and preventative
maintenance on Gorbel® Tarca® Systems. It is intended that this checklist be supplemented with
any additional instruction sheets and maintenance manuals sent with each job.
The frequency of inspection and lubrication recommendations presented herein is based upon
normal operating conditions of one complete handling cycle every 10 minutes throughout a
40-hour week. If the actual duty cycle of a particular unit is greater or less than this, the inspec-
tions and lubrications should be performed more frequently or less frequently in proportion.
Each industry has conditions peculiar to it, which may cause wear of certain parts. The tabulation
given is only general and may be supplemented by an individual maintenance department
program to meet its own particular requirements. Particular attention should be given to corrosive
conditions, excessive vibrations, extreme ambient temperature variations, and rough handling
conditions.
Questions regarding damaged, worn or cracked equipment components should be directed to
the Gorbel® Customer Service Department at 800-821-0086 or 585-924-6262.
The recommendations contained herein are to be supplemented by any vendor instructions,
which are included in this manual.
WARNING:
Power should be off and locked when performing maintenance on any part of the
system.
* State and local codes may require inspection and maintenance checks more often. Please
check the state and local code manuals in your area.
TRACK SWITCHES
COMPONENT
MAINTENANCE
FREQUENCY
Outer Frame
Check for loose support bolts and levelness of frame in both directions.
Check for excessive wear at latch holes or on latch cams.
Every 2,000 hours
or yearly
Inner Frame
Check rollers (should not rock with level outer frame). Check latch pin or
rollers for full and positive engagement. Make sure operator fasteners
are tight and in proper position. Check crank and fasteners for wear and
proper tightness.
Every 2,000 hours
or yearly
Slides or Rollers
Clean and perform maintenance greasing of grease fittings with any gen-
eral purpose grease. Refer to
figure 1
on page 24 for position of fittings.
Every 2,000 hours
or yearly
Jumper Harness
Check for loose or corroded connections or abrasion.
Every 2,000 hours
or yearly
Grounds
Check for continuity.
Every 2,000 hours
or yearly
Track
Check for worn ends. Check for raised tread. Check for track width.
Check for cracked welds. Replace track or switch if badly worn. Check
alignment at rail gaps. Should be within 0-1/32” vertically and +/- 1/16”
horizontally. If realignment is necessary, adjust throw first then shim and
align adjacent rails.
Every 2,000 hours
or yearly
Electrical
Check control panel and/or junction box terminals. Check contacts.
Tighten loose screws.
Every 2,000 hours
or yearly
Rubber Bumper
Check for loose bolts and for incipient cracks.
Every 1,000 hours
or every 6 months
Summary of Contents for Tarca I Series
Page 2: ...11 2018 THIS PAGE INTENTIONALLY LEFT BLANK...
Page 4: ...11 2018 THIS PAGE INTENTIONALLY LEFT BLANK...
Page 15: ...11 11 2018 APPENDIX A BEAM END PREP DIAGRAMS...
Page 16: ...APPENDIX A BEAM END PREP DIAGRAMS CONTINUED 12 11 2018...
Page 17: ...13 11 2018 APPENDIX A BEAM END PREP DIAGRAMS CONTINUED...
Page 18: ...APPENDIX A BEAM END PREP DIAGRAMS CONTINUED 14 11 2018...
Page 19: ...15 11 2018 APPENDIX B WIRING DIAGRAMS 2 Way Motorized Schematic...
Page 20: ...APPENDIX B WIRING DIAGRAMS CONTINUED 16 11 2018 3 Way Motorized Schematic...
Page 21: ...17 11 2018 APPENDIX B WIRING DIAGRAMS CONTINUED 2 Way Pneumatic Schematic...
Page 22: ...APPENDIX B WIRING DIAGRAMS CONTINUED 18 11 2018 3 Way Pneumatic Schematic...