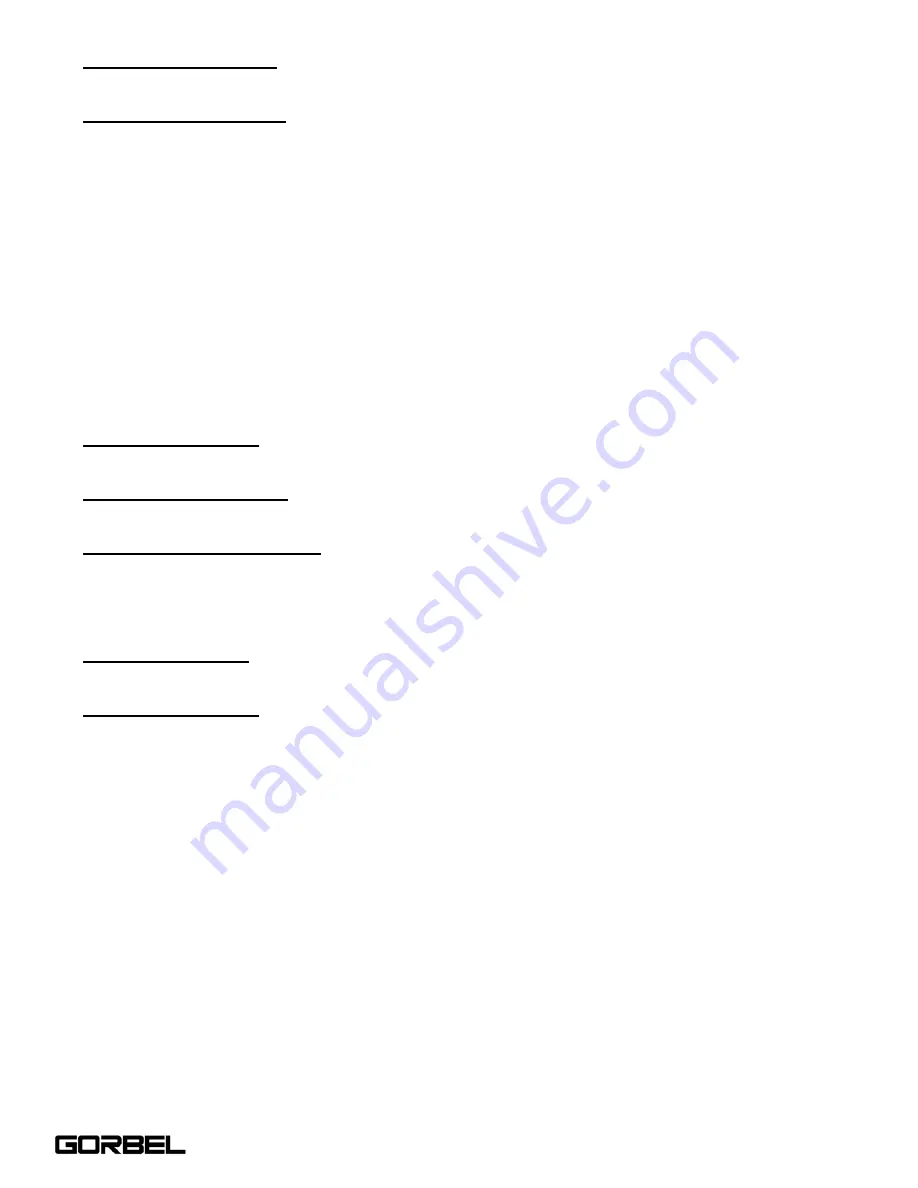
2.
Speed Control Adjustment:
The 10 position Speed Control adjustment switch allows the operator to adjust the
speed of the lifting device with a small flathead screwdriver.
3.
Power Up Diagnostic Mode:
When the “E-stop” button is released and power is applied to the lift, the servo
motor controller goes into a power up diagnostic mode test. The following are the sections of the diagnostic
mode test:
a) LED Indicator Test:
The purpose of this test is to verify the five (5) indicator LEDs are functional.
When the E-stop button is released, the yellow “Power On” LED comes on immediately indicating the
internal 24 volt power is operational. After the servo controller completes a series of self-tests, it turns
on the four (4) remaining LEDs for two (2) seconds to simply verify functionality.
b) Switch Test:
After completion of the indicator test, a system switch test is started. The purpose of this
test is to display the state of the “Slack” switches and “Upper and Lower Limit” switches. During the
switch test, the Green “Standard Mode” LED will remain on if the “Upper Limit” switch is triggered (up
limit state) and the Blue “Float Mode” LED will remain on if the “Slack” switches are triggered (wire rope
slack). Once the operator present switch or jog switch is activated, the servo motor controller exits the
power up diagnostic mode and goes into normal operation.
Note:
The Yellow Power On indicator will remain on during the power up diagnostic mode test.
4.
Power On LED (Yellow):
The “Power On” LED illuminates when the required 220 VAC, single-phase power
has been correctly applied to the system and the E-Stop button has been released.
5.
Standard Mode LED (Green):
The “Standard Mode” LED illuminates when all system initialization is complete
and the operator present switch is depressed, thus activating the standard mode of operation.
6.
Capacity Overload LED (Orange):
The “Capacity Overload” LED illuminates when a load or impact load
greater than the capacity of the hoist has been detected by the system. When this LED illuminates, the
controller will allow the operator to lower the load, but it will inhibit the operator from raising the load prior to
“resetting” the system. To clear the overload fault and “reset” the system, release the switch for approximately 1
to 2 seconds. Once the LED turns off, the system can again be operated.
7.
Float Mode LED (Blue):
If the unit is equipped with Float Mode (system option), the “Float Mode” enabled LED
will illuminate when the Float Mode button is pressed on the hand controller and Float Mode has been initiated.
8.
System Fault LED (Red):
The “System Fault” LED flashes when basic faults have been detected by the control
system. If a fault has occurred, the “Standard Mode” or “Float Mode” (if equipped) LEDs will turn off.
9
4/04-Rev. S
®
Summary of Contents for 150 BX G-Force
Page 26: ...Figure A3 bottom Figure A4 top 150 BX Actuator Assembly 25 4 04 Rev S ...
Page 27: ...Figure A5 150 BX Actuator Assembly 26 4 04 Rev S ...
Page 28: ...Figure A6 150 BX Actuator Assembly 27 4 04 Rev S ...
Page 29: ...Figure A7 bottom Figure A8 top 150 BX Actuator Assembly 28 4 04 Rev S ...
Page 30: ...Figure A9 bottom Figure A10 top 150 BX Actuator Assembly 29 4 04 Rev S ...
Page 31: ...Figure A11 bottom Figure A12 top 150 BX Actuator Assembly 30 4 04 Rev S ...
Page 32: ...Figure A13 150 BX Actuator Assembly 31 4 04 Rev S ...
Page 33: ...Figure A14 150 BX Actuator Assembly 32 4 04 Rev S ...
Page 35: ...Figure B3 bottom Figure B4 top 300 380 BX Actuator Assembly 34 4 04 Rev S ...
Page 36: ...Figure B5 300 380 BX Actuator Assembly 35 4 04 Rev S ...
Page 37: ...Figure B6 300 380 BX Actuator Assembly 36 4 04 Rev S ...
Page 38: ...Figure B7 bottom Figure B8 top 300 380 BX Actuator Assembly 37 4 04 Rev S ...
Page 39: ...Figure B9 bottom Figure B10 top 300 380 BX Actuator Assembly 38 4 04 Rev S ...
Page 40: ...Figure B11 bottom Figure B12 top 300 380 BX Actuator Assembly 39 4 04 Rev S ...
Page 41: ...40 Figure B13 300 380 BX Actuator Assembly 4 04 Rev S ...
Page 42: ...Figure B14 300 380 BX Actuator Assembly 41 4 04 Rev S ...
Page 44: ...Figure C3 Standard Handle Assembly 43 4 04 Rev S ...
Page 45: ...Figure C4 Standard Handle Assembly 44 4 04 Rev S ...
Page 46: ...Figure C5 bottom Figure C6 top Standard Handle Assembly 45 4 04 Rev S ...
Page 47: ...Figure C7 bottom Figure C8 top Standard Handle Assembly 46 4 04 Rev S ...
Page 48: ...Figure C9 bottom Figure C10 top Standard Handle Assembly 47 4 04 Rev S ...
Page 49: ...Figure C11 bottom Figure C12 top Standard Handle Assembly 48 4 04 Rev S ...
Page 50: ...Figure C13 Standard Handle Assembly 49 4 04 Rev S ...
Page 52: ...Figure D3 bottom Figure D4 top Float Mode Handle Assembly 51 4 04 Rev S ...
Page 53: ...Figure D5 bottom Figure D6 top Float Mode Handle Assembly 52 4 04 Rev S ...
Page 54: ...Figure D7 bottom Figure D8 top Float Mode Handle Assembly 53 4 04 Rev S ...
Page 55: ...Figure D9 bottom Figure D10 top Float Mode Handle Assembly 54 4 04 Rev S ...
Page 56: ...Figure D11 Float Mode Handle Assembly 55 4 04 Rev S ...
Page 58: ...Figure E2 Air Coil Cord Assembly Standard Float Mode 57 4 04 Rev S ...
Page 59: ...Figure E3 Remote Mount Coil Cord Standard Float Mode 58 4 04 Rev S ...
Page 60: ...Figure E4 Air Remote Mount Coil Cord Standard Float Mode 59 4 04 Rev S ...
Page 61: ...APPENDIX F CONTROLS SCHEMATIC DRAWINGS Figure F1 Remote Load Cell Assembly 60 4 04 Rev S ...
Page 62: ...Figure F2 BX Controls Schematic 61 4 04 Rev S ...
Page 64: ...Figure G2 BX G Force 300 380 Overall Dimensions 63 4 04 Rev S ...
Page 67: ...Figure I2 300 380 Standard Inline Component Layout 66 4 04 Rev S ...
Page 68: ...Figure I3 Standard Remote Mount Component Layout 67 4 04 Rev S ...