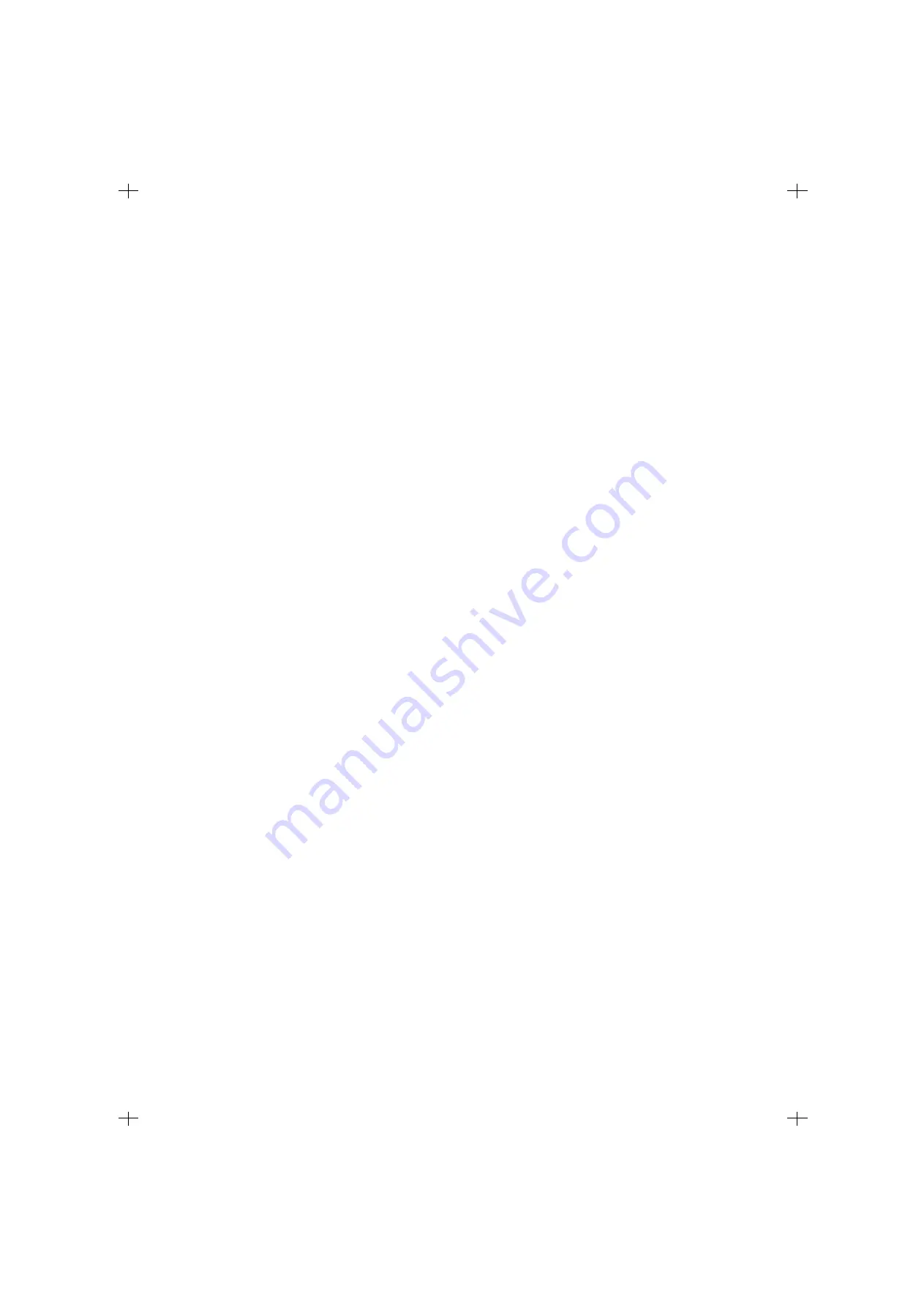
D. REMOVING MAGNETRON (Figures 17 through 21)
(1) Remove the vent grille by removing two screws.
(2) Remove the controller by removing a screw and
disconnect all wire leads.
(3) Remove the base plate by removing six screws
securing it to the oven front plate and outcase.
(4) Remove the wire cover by removing a screw
securing it to the oven lower plate. Disconnect the
cook top leads connector from the bottom plate-R.
(Figure 17)
(5) Remove the outcase by removing eleven screws
securing it to the front bracket, power cord cover,
ventilation asm and outcase.
(6) Remove the ventilation asm by disconnect the wire
leads.
(7) Remove the air duct by removing five screws
securing it to the oven front plate, cover glasswool-R,
and guide air. (Figure 18)
(8) Remove the C-motor bracket assy by removing four
screws securing it to the cover glasswool-R and
guide air. (Figure 19)
(9) Remove the guide air by removing three screws
securing it to the bottom plate-R and guide air.
(Figure 19)
(10) Remove the guide suction by removing three
screws securing it to the bottom plat-R, oven front
plate and magnetron. (Figure 20)
(11) Remove four tap tite screws securing the
magnetron to the wave guide. (Figure 21)
(12) Remove the magnetron VERY CAREFULLY.
NOTES
Remove the leads from the magnetron thermostat very
carefully. Use long nose pliers.
NOTES
●
When removing the magnetron, make sure that its
dome does not hit any adjacent parts, or it may be
damaged.
●
When replacing the magnetron, be sure to install the
magnetron gasket in the correct position and be sure
that the gasket is in good condition.
●
After replacing the magnetron, check for microwave
energy leakage with a survey meter.
Check microwave energy leakage must be below the
limit of 4 mW/Cm
2
.
(All service adjustments should be made minimum
microwave energy leakage readings).
— 17 —
Summary of Contents for MV-1155W
Page 8: ...6 OVERALL CIRCUIT DIAGRAM A SCHEMATIC DIAGRAM 7 ...
Page 40: ...CONTROLLER PARTS 38 WTT028 WTT021 WTT021 268711 24810P 26638A 07 23572A 24781M WTT021 EV ...
Page 42: ...LATCH BOARD PARTS 40 WSZ085 43500A 466001 466004 466002 43510A 466003 43501A EV ...
Page 45: ...INTERIOR PARTS III 43 WTT021 53551S 53551L WSZ002 WSZ002 53551R 568772 WTT021 WTT021 EV ...
Page 48: ......