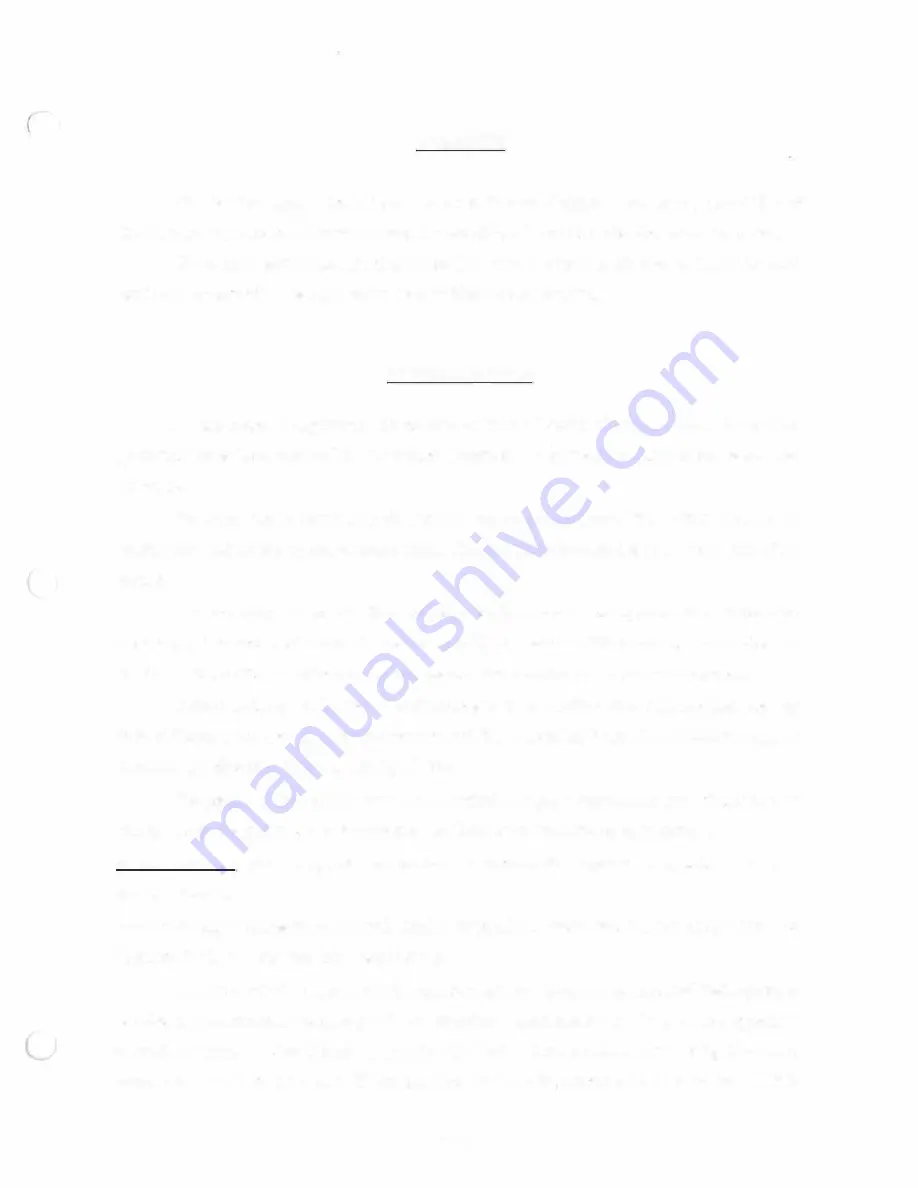
ABRASIVE
The abrasive has a major influence on the efficiency of cleaning and on the profitability of
the blast cleaning system. We recommend the use of tough cast steel abrasive or cut wire shot.
We strongly advise against using chilled iron shot. It is less durable and its sharp edges and
particular texture will cause premature wear of blast wheels and liners
OPERATING MIX
In most cases, the operating mix consists of rounded grains of various sizes. The medium
grain size forms the major portion. There must, however, also be active portions of coarse and fine
granulates.
The coarse grains (nominal grain size) remove the surface layer. The medium sized grains
perform the main cleaning job, whereas the small sized grains clean and smooth the details of the
surface.
This operating mix results from the wear of the abrasive during operation of the blast
cleaning system and should be kept constant by refilling abrasive with the nominal grain size. For
the first filling of the blast cleaning system, a simulated operating mix must be composed.
In order to do so, the following grain sizes should be used: approx. 30% nominal size and
70% of the next two sizes smaller than the nominal size. Thereafter the refill, carried out at regular
intervals, consists only of the nominal grain size.
The quality of the abrasive should be checked at regular intervals, as poor abrasive has a
strong negative effect on the efficiency and profitability of the blast cleaning system.
As a general rule: Abrasive grains smaller than 1/3 of the nominal grain size have to be removed in
the air separator.
In order to keep the abrasive consumption as low as possible, special care must be taken to limit the
abrasive that is retained with the clean castings.
The proper selection of abrasive is important, not only from the standpoint of blasting results
but also from a maintenance standpoint. An abrasive of good quality will help to keep operating
costs at a minimum. Abrasives are generally classified in shape as either "shot" or "grit" and are
designated as such by the letters "S" for shot and "G" for grit preceding the size number. Grit is
4-14
Summary of Contents for 2460
Page 6: ...SECTION 1 GENERAL INFORMATION General Description 1 1 Installation Procedures 1 2 ...
Page 15: ...M0I099 CW BLAST WHEEL FRONT VIEW Refer to replacement parts list on page 2 2 2 5 ...
Page 16: ...MOI OO 0 I CCW BLAST WHEEL FRONT VIEW Refer to replacement parts list on page 2 3 2 6 ...
Page 17: ...M0581B BLAST WHEEL SIDE VIEW Refer to replacement parts list on page 2 2 2 3 2 7 ...
Page 18: ...M058IC BLAST WHEEL EXPLODED VIEW Refer to replacement parts list on page 2 2 2 3 2 8 ...
Page 38: ...M01159A 0 0 I 0 FRONT VIEW DETAIL Refer to replacement part list on page 3 1 3 3 ...
Page 39: ...MO 159B L SIDE VIEW DETAIL Refer to replacement part list on page 3 1 3 4 ...
Page 41: ...MOl 159D I I G SPAN SPINNER DETAIL Refer to replacement part list on page 3 1 3 6 ...
Page 42: ...MOl 159E l I CHMHBER E THRUST BEARING DETAIL Refer to replacement part list on page 3 1 3 7 ...
Page 43: ...M01 159F SPAN DETAIL l Refer to replacement part list on page 3 1 3 8 ...
Page 44: ... G M01 159G CHAMBER DRIVE ASSEMBLY DETAIL Refer to replacement part list on page 3 1 3 9 ...
Page 55: ...M01163B 0 9 ELEVATOR BOTTOM ASSEMBLY Refer to replacement parts list on page 4 9 4 10 4 ...