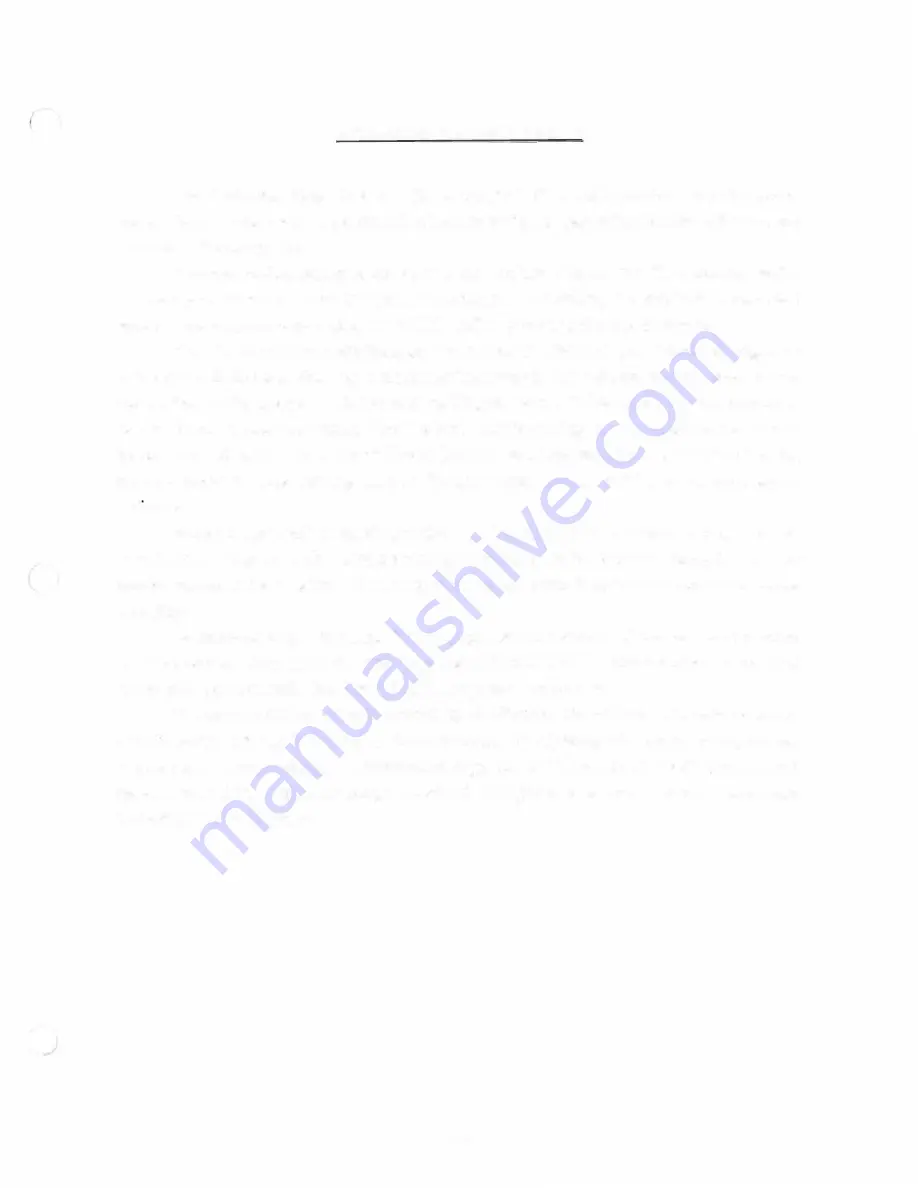
l
ABRASIVE CONTROL VAL VE
The Goff airless blast wheel assembly is equipped with a totally enclosed abrasive control
valve. Correct adjustment of the control valve is essential for maximum cleaning efficiency and
maximum blast motor life.
The abrasive flow adj ustment is determined by the blast wheel motor. (To determine the full
load rating of the motor, check the motor manufacturer's nameplate.) To obtain maximum blast
wheel efficiency, the motor should run at "full load" amperage during the blast cycle.
When the blast wheel motor is started, the ammeter indicator will go to the extreme right side
of the dial until the blast wheel has attained maximum speed. The indicator will then drop back to
normal "no load" amperage. This "no load" reading can serve to indicate the presence of motor or
bearing trouble in future operation. When the blast wheel is running true, the ampere reading should
be constant and steady. Any severe fluctuations can be interpreted as an indication of bearing
trouble, "drag" in some moving parts of the blast wheel, motor trouble, or electrical supply
variances.
While the machine is in actual operation, any fluctuations in the ammeter reading should be
investigated. Changes could indicate shortage of abrasive, stalled elevator, clogged screen, or
foreign objects in the impeller. The ammeter serves as a prime indicator of proper or improper
operation.
As the abrasive valve is opened the amperage load will increase. The valve should be set so
that the motor will draw maximum rated amperage or run at full load. Always run the blast motor at
full load (never overload). Monitor and adjust amperage as necessary.
The abrasive control valve is operated by an adjustable air cylinder. The cylinder has an
adjustable bolt mounted in the end of the air cylinder. By adjusting this bolt, in or out, you can
increase or decrease amperage. To increase amperage, loosen the jam nut on the bolt adjustment and
back the bolt out until desired amperage is obtained. Re-tighten the jam nut. To decrease amperage,
the bolt should be tightened.
2-18
Summary of Contents for 2460
Page 6: ...SECTION 1 GENERAL INFORMATION General Description 1 1 Installation Procedures 1 2 ...
Page 15: ...M0I099 CW BLAST WHEEL FRONT VIEW Refer to replacement parts list on page 2 2 2 5 ...
Page 16: ...MOI OO 0 I CCW BLAST WHEEL FRONT VIEW Refer to replacement parts list on page 2 3 2 6 ...
Page 17: ...M0581B BLAST WHEEL SIDE VIEW Refer to replacement parts list on page 2 2 2 3 2 7 ...
Page 18: ...M058IC BLAST WHEEL EXPLODED VIEW Refer to replacement parts list on page 2 2 2 3 2 8 ...
Page 38: ...M01159A 0 0 I 0 FRONT VIEW DETAIL Refer to replacement part list on page 3 1 3 3 ...
Page 39: ...MO 159B L SIDE VIEW DETAIL Refer to replacement part list on page 3 1 3 4 ...
Page 41: ...MOl 159D I I G SPAN SPINNER DETAIL Refer to replacement part list on page 3 1 3 6 ...
Page 42: ...MOl 159E l I CHMHBER E THRUST BEARING DETAIL Refer to replacement part list on page 3 1 3 7 ...
Page 43: ...M01 159F SPAN DETAIL l Refer to replacement part list on page 3 1 3 8 ...
Page 44: ... G M01 159G CHAMBER DRIVE ASSEMBLY DETAIL Refer to replacement part list on page 3 1 3 9 ...
Page 55: ...M01163B 0 9 ELEVATOR BOTTOM ASSEMBLY Refer to replacement parts list on page 4 9 4 10 4 ...