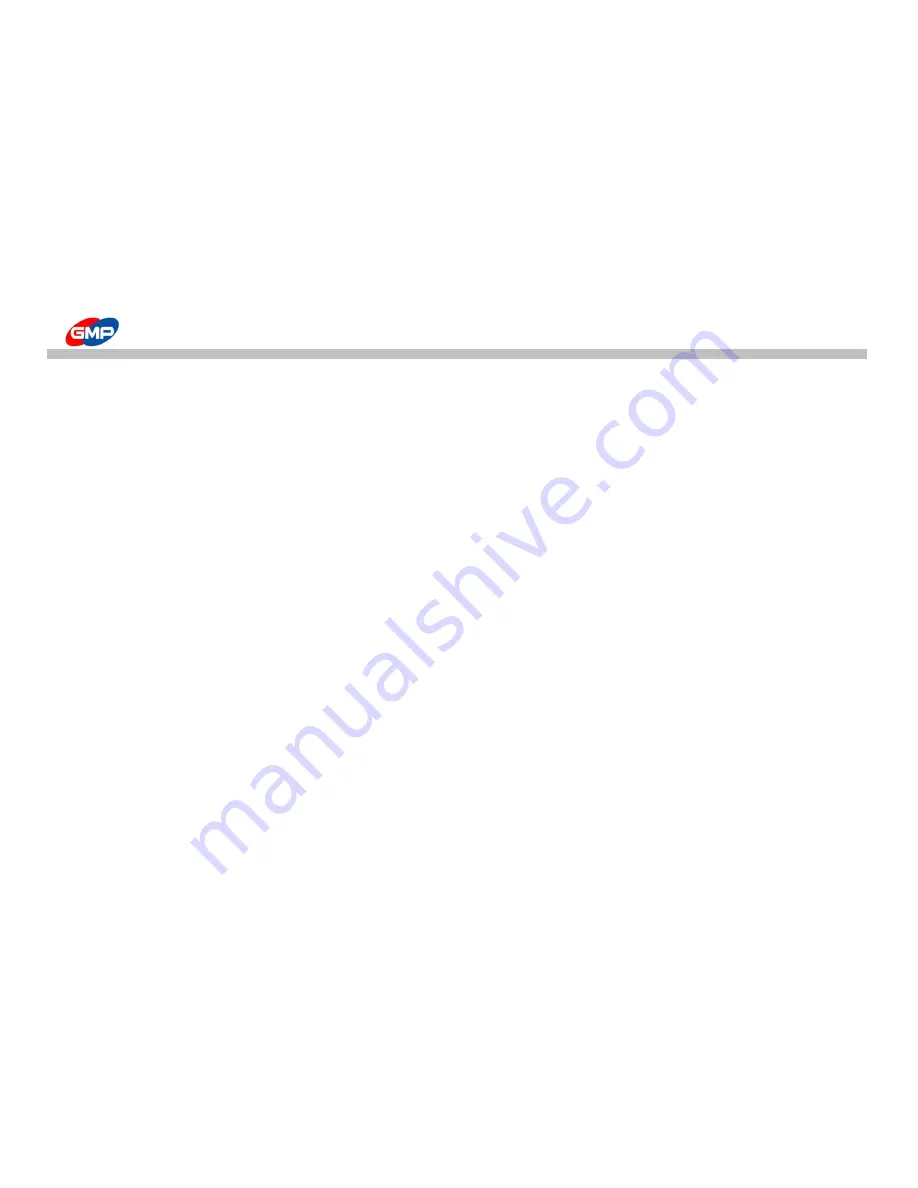
HOW TO LAMINATE
☞ Test Lamination
If Roller Temp. is reached to the Setting Temp., test lamination is required to check the setting condition & lamination status.
Start at 3~5m/min speed and increase its speed.
Press "RUN" button to engage the roller and lamination is started.
※ Checking Points for Test Lamination
1. Distance of Overlap for Substrates
: 3~5mm ideally
- If under lapped area is not sufficient, press "PAPER LENGTH" on control panel to adjust length of substrate.
2. Decurling Status
: check the curling status of the paper and adjust it with Decurling Controller.
- Adjust its angle for substrate thickness and its material.
3. Laminating Status
: Check it with various Pressure, Temp. conditions.
- Each condition requires to be adjusted for film / substrate status. The lamination quality (bonding strength) is
proportional to temp. and pressure strength and is inverse proportional to speed.
4. Cutting
: Check the Bursting Roller Operation Time & Perforator status.
☞ Lamination
If the test lamination is acceptable, increase its speed for lamination.
※ Notice for Lamination
1. Stop lamination could make a mark on a laminated results.
2. Basically, thicker substrates requires lower speed or higher temp.
3. Thinner substrates requires higher speed or lower temp.
4. For perfect lamination, similar materials lamination first and adjust the conditions for real lamination.
5. If substrate would not be fed properly, this could be a cause of wrinkle.
30/48