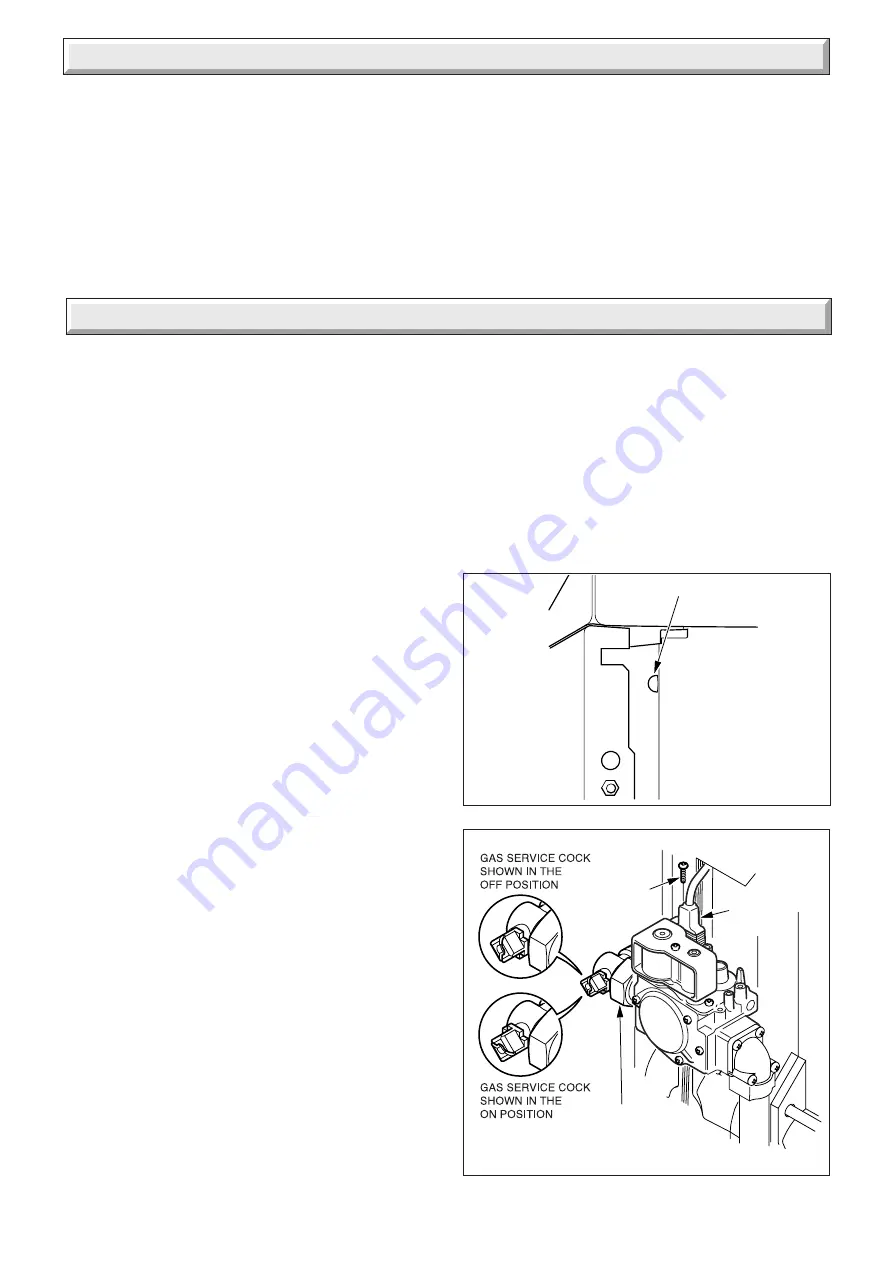
23
0020003579A
7 Instructions to the User
Instruct and demonstrate the safe and efficient operation of the boiler, heating system and domestic hot water system.
Advise the user, that to ensure the continued efficient and safe operation of the boiler, it is recommended that it is checked and
serviced at regular intervals. The frequency of servicing will depend upon the particular installation and usage, but in general once
a year should be enough.
Draw attention, if applicable to the current issue of the Gas Safety (Installation and Use) Regulations, Section 35, which imposes
a duty of care on all persons who let out any property containing a gas appliance in the UK.
It is the Law that servicing is carried out by a
competent person
.
Advise the user of the precautions necessary to prevent damage to the system and building in the event of the heating system being
out of use during frost and freezing conditions.
Reminder - Leave these instructions and the “Benchmark” logbook with the user.
8 Servicing
REMEMBER, When replacing a part on this appliance, use only
spare parts that you can be assured conform to the safety and
performance specification that we require. Do not use
reconditioned or copy parts that have not been clearly authorised
by Glow-worm
Products of Combustion Check
NOTE:
To obtain a products of combustion reading, remove the
front panel, see diagram 6.3 and remove the control box as
described in the relevant paragraphs of section 4.9. Next,
remove the cap from the sampling point, located on the top of
the left hand side of the inner casing, see diagram 8.1.
Connect the analyser tube on to the nipple.
WARNING:
The multifunctional control and fan operate on
mains voltage, terminals will become live.
Switch on the electrical supply and gas supply then operate the
boiler.
On completion of the test switch off the electrical supply and gas
supply, remove analyser tube and replace sampling point cap.
Servicing
Before servicing turn off the gas and isolate the electrical supply
to the boiler.
After completing a service always test for gas soundness, make
electrical checks and carry out functional check on controls.
Unless stated otherwise all parts are replaced in the reverse
order to removal.
8.1 Access
Remove the boiler front casing panel, refer to paragraph 6.8.
Remove the bottom plinth panel by unscrewing the two dog
point screws securing the panel to the boiler plinth, see diagram
8.4.
Disconnect gas valve from gas cock and unplug electrical plug
from gas valve, firstly removing electrical plug securing screw,
see diagram 8.2.
Unclip electrical wires from control box support bracket, see
diagram 8.3.
Undo the five self-tapping screws that secure the combustion
chamber front and carefully withdraw it together with the burner
and gas valve assembly, taking care not to strain the ignition,
sensing and earth leads, see diagram 8.5.
NOTE:
When replacing burner in combustion chamber make
sure it fits correctly on the guides.
Diagram 8.2
12165
GAS SERVICE
COCK UNION
Diagram 8.1
Disconnect the ignition, sensing and earth leads from the
burner and remove by drawing the leads though the grommet,
see diagram 8.5 and 8.9.
Remove the three self-tapping screws from the lower part of the
control box support bracket, see diagram 8.6.
Undo the wing nut that secures the top of the heat shield and
carefully hinge down control box and heat shield, see diagram
8.6.
Release the three toggle latches that secure the boiler access
door and remove, see diagram 4.10.
SECURING
SCREW
12091
SAMPLE POINT
ELECTRICAL
PLUG