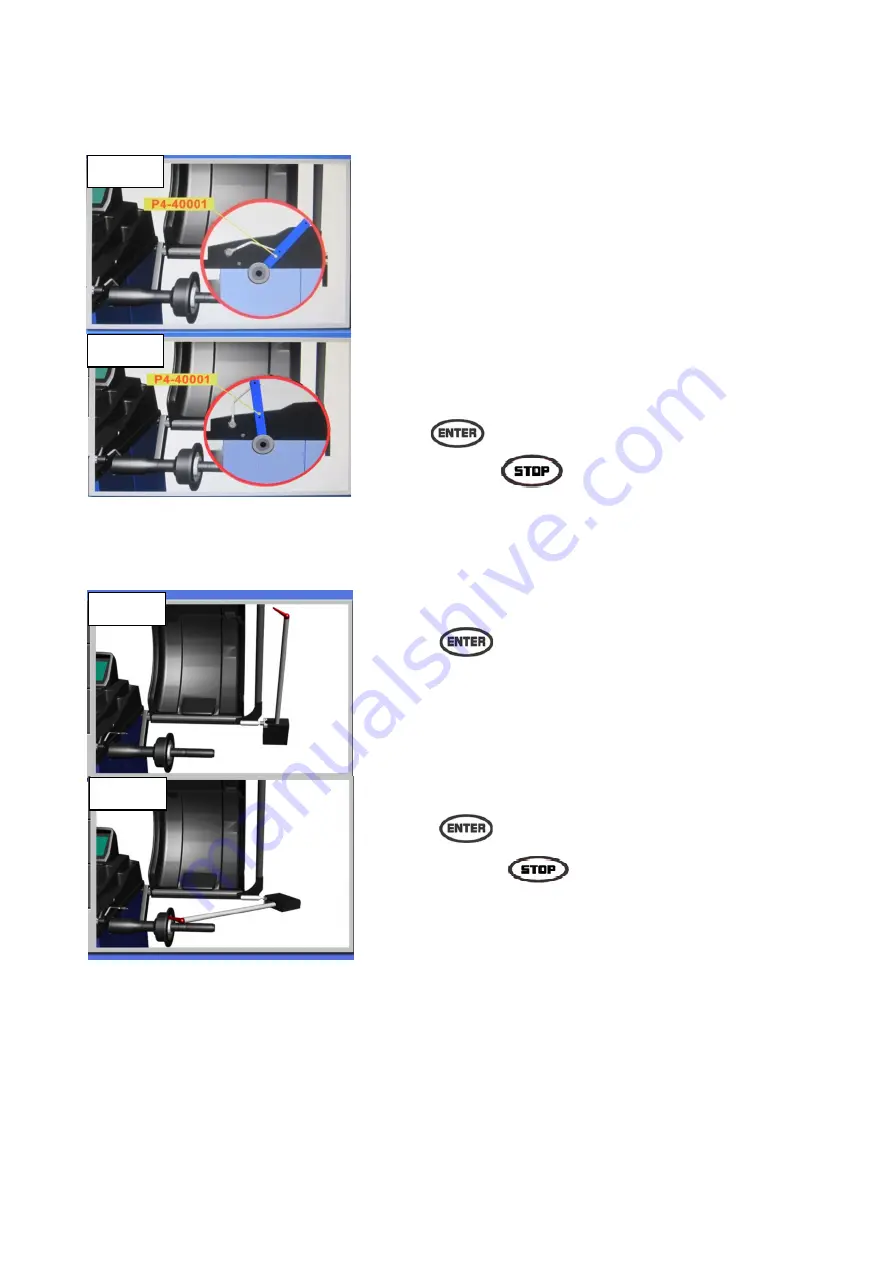
REV. 01 2020
25 / 28
7.2.3 CALIBRATION OF D GAUGE
7.2.4 CALIBRATION OF B GAUGE – optional
Place the gauge to the “0” position.
Press to memorize.
Set the gauge head to the outer surface of the shaft flange.
Press to memorize.
To exist, press .
Place the supplied calibration meter on the HIGER
PROFILE surface of shaft (“0” position) and then set the
gauge tip into the lower hole of the meter.
Place the supplied calibration meter on the HIGER
PROFILE surface of shaft (“0” position) and then set the
gauge tip into the upper hole of the meter (“200” position)
Press to memorize.
To exist, press .
Fig. 31
Fig. 30
Fig. 32
Fig. 33