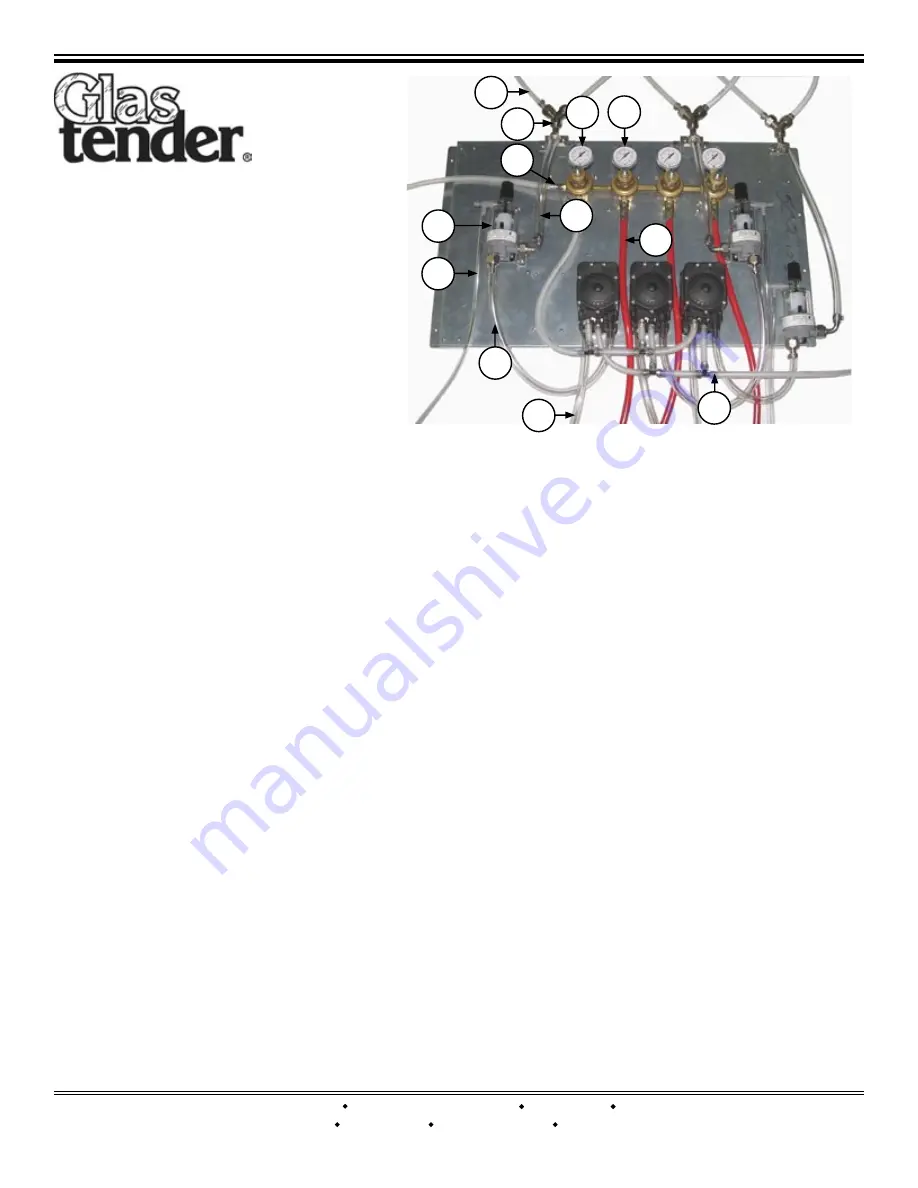
Glastender, Inc. 5400 North Michigan Road Saginaw, MI. 48604-9780
800.748.0423 989.752.4275 Fax: 989.752.4444 www.glastender.com
BPIK-EY
Beer Pump Panel
Installation Instructions
04-06-06
F-750-359 Rev. A
These instructions assume that the primary
regulator and CO2 line to the walk-in cooler are
already installed.
1. Position the regulator panels according to
factory instructions.
2. Connect CO2 source line to one end (A) of
regulator bank. If there is more than one panel, continue the line to the next panel until all panels are connected
3. Approximately 9 feet of clear vinyl beer line (B) is provided for the keg jumper line from each keg to its beer pump.
Trim clear line to size and attach one end to the input port of the beer pump and the other end to the keg tap. The beer
pump ports are shipped loose in a bag attached to the regulator.
4. Approximately 9-1/2 feet of red air line (C) is provided for the jumper line from each keg to its regulator (D). Trim red
air line to size and attach one end to the regulator and the other end to the keg tap.
5. Attach an Empty Keg Detector (E) to each of the black EKD mounting brackets by sliding them in place. The EKD
can be mounted to flow left or right. Position them so that the EKD output port points in the appropriate direction to
flow to the corresponding Y angle bracket (F).
6. Attach the appropriately numbered, pre-made jumper line (G) from the output port of each pump to the bottom input
port of its EKD. Use a black washer on the EKD end.
7. Attached to each Y angle bracket (F) is a clear jumper line (H). Attach the free end of the clear jumper line to the
appropriate EKD side output port, using a black washer.
8. Attach the polyline (I) from the beer line set (conduit) to the top output ports of each Y angle bracket.
9. Approximately 6 feet of exhaust line (J) is provided for the exhaust port of each EKD. Trim the exhaust line to length
and attach to each EKD exhaust port so the exhaust can be drained to a bucket. No clamp is required.
10. The CO2 exhaust port of each pump has been pre-plumbed at the factory to create one CO2 exhaust port connection
(K). Use the CO2 line provided to exit the CO2 from the walk-in cooler. An extra tee is provided with each panel
in case you want to join the exhaust lines of adjacent panels. THE EXHAUST PORT OF EACH PUMP MUST BE
VENTED OUTSIDE THE WALK-IN.
11. The keg regulators (D) provide individual pressure to each keg. Set each keg regulator at the keg’s natural internal
head pressure, normally between 12 to 16 pounds. To get to the natural head pressure level for the keg, start with the
regulator set around 10 pounds. Draw beer through the line. If bubbles appear in the clear keg jumper line, then the
pressure should be adjusted upward slightly. Repeat until the bubbles do not form in the line. Be careful not to set the
pressure too high or the beer will over-carbonate. NOTE: This step needs to be done in conjunction with step #8 until
proper results are achieved.
12. The beer pump regulator (L) controls the pressure going to the beer pumps on that panel. Each pump on the panel
receives the same level of pressure, which is intended for beer lines traveling to the same tower (i.e. same length of
beer line). Upon start-up, the beer pump regulator should be set at a pressure level that provides the proper flow rate.
Start around 10 pounds and work up from there to achieve a 2 ounces per second flow rate.
A
E
D
C
B
G
F
H
I
J
K
L