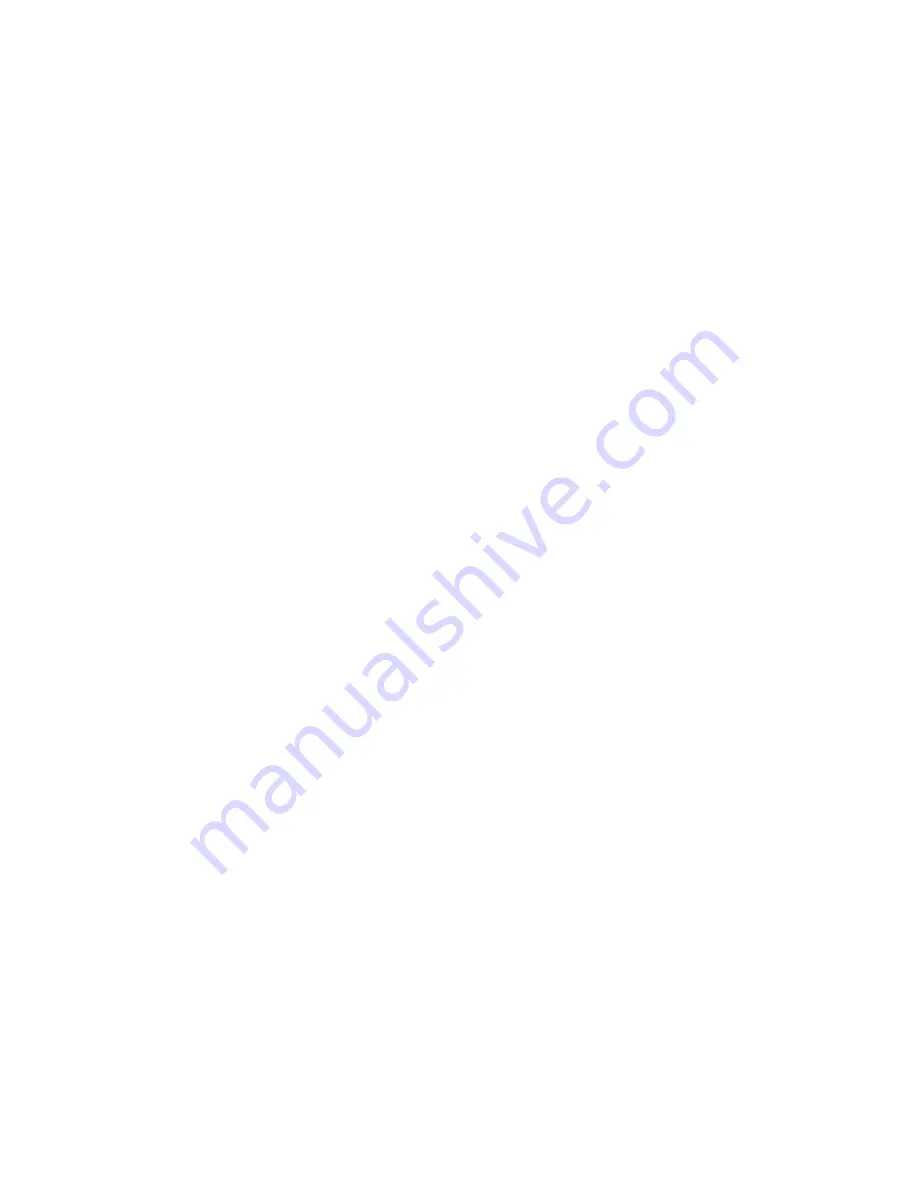
INSPECTION
After a thorough cleaning of all parts, place the components on the bench and
inspect them carefully. All those parts that show signs off wear and/or damage
must be replaced.
Head
Scrape the surface and remove traces of head gasket and remove all carbon
deposit in the combustion chamber. Be certain that all contact surfaces are in
good condition and that the combustion chamber shows no sign of cracks or
deep scratches (especially around the valve seats).
Check that the head surface is not warped by means of a straight gauge.
Max. planning error = 0.05 mm.
The surface may be planed to a max. of 0.2 mm if necessary.
Caution: do not machine the top surface of the head: this may cause the
shafts to lock.
Valves
Valve stems and seats must be in good condition.
Make sure that end of the stem doesn’t show signs of excessive wear.
In the event of valve seat wear, resurface by grinding.
Check that the valve stem is straight.
Max. straightness error allowed = 0.01 mm (fig. 15).
The face must be radial with respect to the stem (fig. 16).
Valve seat must be in good shape, with no sign of pitting, cracking or corrosion
Springs
After visual inspection of the springs and valves, measure the length of each
spring with a gauge (fig. 17).
Allowed values: Outer spring 38.7 ÷ 39.7 mm
Inner spring 37.6 ÷ 38.6 mm
Rocker arms
Make sure the runners (where the camshaft lobes hit against) are in good
condition and don’t have deep scratches, grooves or the like. Check for
excessive gap between rocker arm and shaft.
Max, gap = 0.08 mm
Camshaft
Make sure the camshaft lobes are in good condition, with no sign of damage or
Wear. Measure the height of each lobe. Check cam height on both sides; the
difference between both readings should not exceed 0.1 mm (fig. 18).
Check for excessive gap of the camshaft journals in their respective supports.
Max. radial clearance = 0.1 mm
7 - 2,4
Summary of Contents for Nordwest
Page 1: ...WORKSHOP MANUAL NORDWEST Nordcape in Germany ...
Page 26: ...INTENTIONALLY BLANK ...
Page 28: ...3 1 2 ...
Page 37: ...SECTION 4 INTENTIONALLY BLANK 4 ...
Page 44: ...6 1 2 ...
Page 45: ...6 1 3 ...
Page 49: ...7 1 ...
Page 51: ...7 2 2 ...
Page 52: ...7 2 3 ...
Page 54: ...7 2 5 ...
Page 56: ...CYLINDER PISTON 8 8 Diagram Disassembly Inspection Reassembly Section Page 8 1 8 2 8 2 8 2 ...
Page 57: ...8 1 ...
Page 59: ...8 2 2 ...
Page 61: ...8 2 4 ...
Page 63: ...9 1 ...
Page 65: ...9 2 2 ...
Page 66: ...9 2 3 ...
Page 69: ...10 1 ...
Page 71: ...10 2 2 ...
Page 77: ...12 1 ...
Page 96: ... 15 4 ...
Page 114: ...ELECTRIC STARTER 18 18 1 2 ...
Page 117: ...19 1 2 ...
Page 121: ...TROUBLESHOOTING 20 20 1 ...
Page 122: ...20 2 1 TROUBLESHOOTING 20 Continued on page 20 2 2 ...
Page 123: ...20 2 2 TROUBLESHOOTING 20 Continued from page 20 2 1 ...
Page 124: ...20 3 TROUBLESHOOTING 20 ...
Page 127: ...21 1 2 ...
Page 129: ...21 2 2 ...
Page 131: ...21 3 2 ...