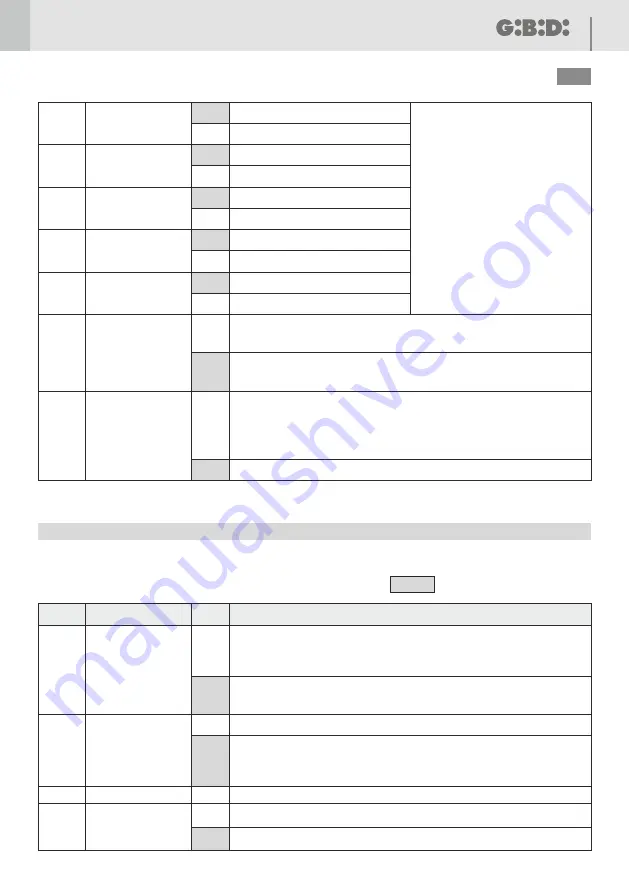
22
F4
UK
8 - DIP SWITCH DIP1
The settings are stored during the rest phase (gate closed
The default settings are highlighted in the boxes with grey background
.
).
DIP1_1
ON
PHOTOCELL
DURING
OPENING
OFF
Description
DIP
Status
Function
When the photocell is broken/interrupted during both opening and closing, the gate
motion is ceased until the photocell is re-made.
Subsequently the gate will always OPEN.
Breaking or interrupting the photocell during PAUSE will cause the pause-time
to begin counting down again.
The photocell stops and immediately inverts the gate motion during closing
while it is uninfluential during opening.
Breaking or interrupting the photocell during PAUSE will cause the pause-time
to begin counting down again.
DIP 3
1_
ELECTRIC LOCK
RELEASE STROKE
ON
Operation: following a START, OPENING or PEDESTRIAN command, the
following will occur in sequence:
• electric lock activation
• closing pulse of 1 second
• opening
• after 2 seconds, electric lock deactivation
Operation AT THE END OF CLOSING CYCLE (ONLY WITH SLOW-DOWN
ENABLED):
• extra movement in closing of 1 second with FORCE trimmer settings.
This function cannot be activated with a sliding gate configuration and is
unadvisable with electromechanical operators.
Electric lock release stroke disabled.
Simultaneous electric lock activation and opening.
OFF
ON
OPERATING
LOGIC
DIP 2
1_
AUTOMATIC logic
Operation in response to the START command:
STEP-BY-STEP WITH STOP logic
Operation in response to the START command:
• Gate closed
• Gate closed
→
OPENS
→
OPENS
• During opening
• During opening
→
UNINFLUENTIAL
STOPS
→
• During closing
• During closing
• After a STOP
→
OPENS
STOPS
→
inverts the motion
→
• Gate open
• Gate open (PAUSE)
If automatic closing is enabled (see PAUSE trimmer
function) then the pause-time begins again, otherwise it
closes. If automatic closing is enabled (as above) then a
permanent START command (always closed) will hold
the gate open, otherwise it closes.
→
OFF
→
(SEE PAUSE TRIMMER)
If automatic closing is enabled then the gate stops
23
F4
UK
The settings are stored during the rest phase (gate closed
The default settings are highlighted in the boxes with grey background.
).
DIP1_4
DIP1_5
DIP1_6
DIP1_7
DIP1_8
DIP1_9
DIP1_10
MOTOR 1 OPENING
LIMIT SWITCH
MOTOR 1 CLOSING
LIMIT SWITCH
MOTOR 2 OPENING
LIMIT SWITCH
MOTOR 2 CLOSING
LIMIT SWITCH
PHOTOCELL
TERMINALS 7-8
FUNCTIONING
HYDRAULIC LOCK
UPKEEP
ON
OFF
ON
DIP2_1
DIP2_2
ON
TERMINAL 23
FUNCTIONING
TERMINAL M4
FUNCTIONING
OFF
Description
DIP
Status
Function
The STOP input (23) functions as EDGE and when activated, will invert the
motion for 2 seconds in order to free the obstacle.
See also jumper SW15.
The STOP input (23) functions as STOP and when activated, will stop the
motion. See also jumper SW15.
The outputs 7-8 of the terminal board are used to control a FLASHING LIGHT
equipped with its own flashing circuit.
The outputs 7-8 of the terminal board are used to control a COURTESY LIGHT
that remains active for 2 minutes after the motor movement.
For HYDRAULIC motors only.
If the gate has not performed any operation in the last 5 hours, a 2-second
closing pulse is given.
THE STOP KEY DISABLES THE FUNCTION.
Disables the limit switch input
Enables the limit switch input
Disables the limit switch input
Enables the limit switch input
Disables the limit switch input
Enables the limit switch input
Disables the limit switch input
Enables the limit switch input
Disables the photocell input
HYDRAULIC LOCK UPKEEP deactivated.
Terminal M4 operates as WARNING LIGHT.
Terminal M4 operates as FLASHING LIGHT.
In this mode, the terminals 28-29 can be used to connect a FLASHING LIGHT
without a flashing circuit.
NOT USED
Enables the photocell input
ON
ON
ON
ON
ON
OFF
ON
OFF
OFF
OFF
OFF
OFF
OFF
In the case of a system with only one
motor and using the limit switches,
the DIP switches 4, 5, 6 and 7 are
to be set to OFF; while if using only
one type of limit switch (e.g. FCAM1
and/or FCCM1), enable only the
corresponding DIP switch (set to OFF).
9 - DIP SWITCH DIP2
DIP2_3
DIP2_4
Extended positional time recovery. Ideal for motors with inertia (AGO).
Normal positional time recovery.
ON
OFF
POSITIONAL TIME
RECOVERY
Summary of Contents for AS06320
Page 58: ...NOTE NOTES 58 F4 ...
Page 59: ...NOTE NOTES 59 F4 ...