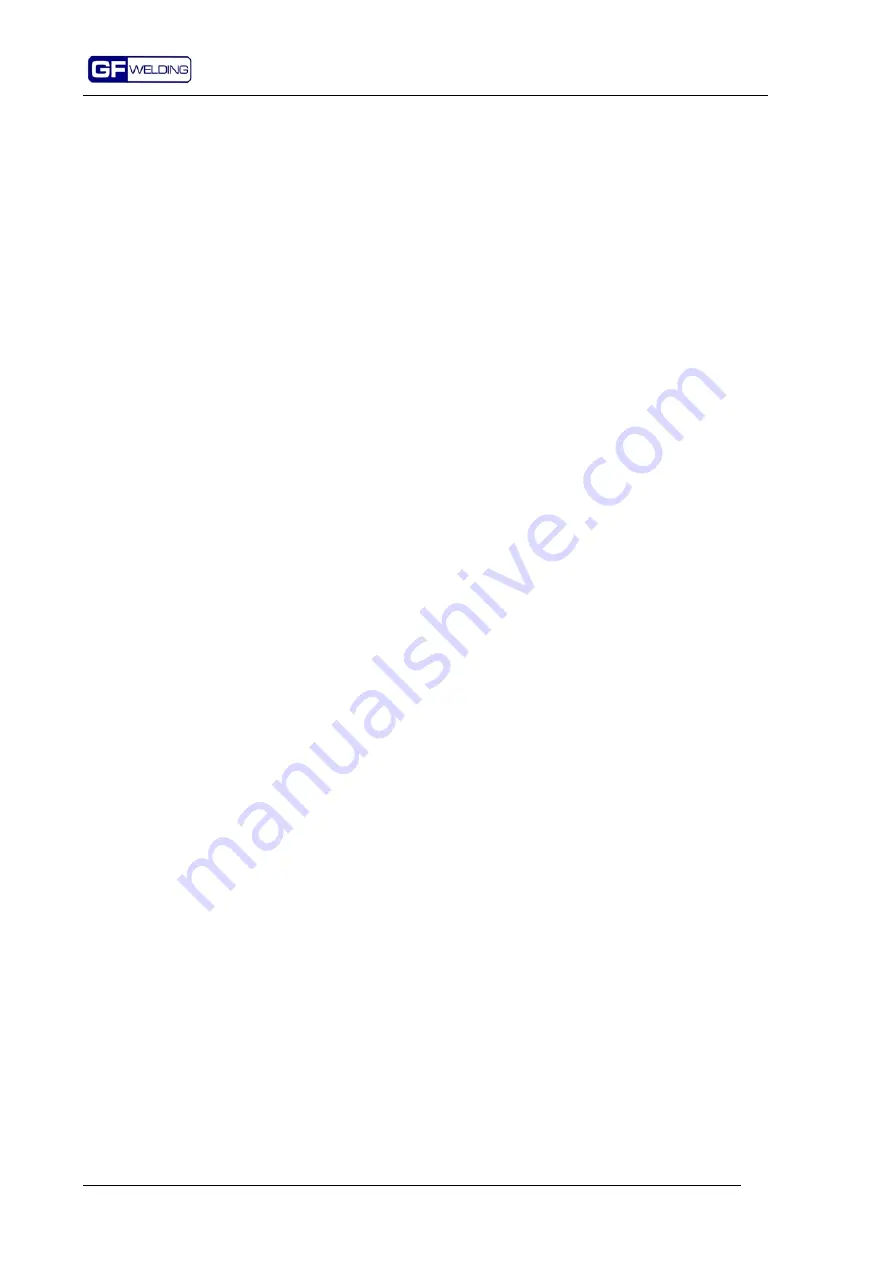
Weld334m - User’s manual
2
1.1
Hazards associated with the use of resistance welding machines
Because of the presence of electric current and live parts in the machine, mounting,
maintenance work and replacement of genuine parts is only to be entrusted to Qualified
Personnel (electricians or authorised personnel). All work undertaken is to be done in safety
conditions. The non-observance of these requirements can cause death, injury to persons
or damage to machine and property.
1.1.1
! Prohibitions
•
It is prohibited to work on the live installation.
•
It is prohibited to remove by-pass and modify the safety devices as this could cause
serious risks to personnel and equipment and could lead to death.
1.1.2
! Conditions to be respected to reduce the hazard
•
Always insure that the electric switchboard main switch is OFF.
•
Work on the machine, equipment and the welding transformer only after breaking
the connection from the mains. This to be sure that no undesired switching of
electrical current occurs.
•
Work on the spotgun and welding cable connections only after breaking the
connection from the mains power.
1.1.3
! Causes of hazard
•
The programming of the welding control is entrusted only to qualified personnel.
Incorrect parameter settings may cause damage or injury because of undesired
molten material splashes during welding.
•
It is compulsory to wear protective goggles, non-flammable clothes and protective
shoes.
•
Dangerous conditions may arise when, for example, electrodes are changed or
dressed and no current re-adaptation/re-setting takes place, especially when using
the stepper function (stepper reset).
•
If 24V power supply is external to the machine or the control device, power may be
applied to the equipment even if the main switch connection is broken.
•
During mounting, setting of work, maintenance and/or repair operations, hazards
may occur because of the exchange of leads, air/water pipes, etc…
•
Unqualified personnel may be unaware of the risk that such changes/modifications
entail, therefore, all changes/modifications are only to be entrusted to and/or
performed by qualified personnel.
•
Hazardous situations may arise because of mains voltage drops, or in case of tripping
of the machine emergency stop device, which causes the return to rest position of
the pneumatic valves in use during the operation (this situation affects the whole
plant).
•
If during the welding process the cooling water flow is low or non-existent, it is
prohibited to bypass or inhibit the tripping of thermostats or the water flow control
device (if installed).
Summary of Contents for Weld334m
Page 1: ...USER S MANUAL Weld334m HC HCM HIC HIM Ed 5 December 2004 Doc 39000326...
Page 6: ...Weld334m User s manual VI WHITE PAGE...
Page 14: ...Weld334m User s manual 8 WHITE PAGE...
Page 28: ...Weld334m User s manual 22 WHITE PAGE...
Page 30: ...Weld334m User s manual F351 BUS Interconnection card 24 WHITE PAGE...
Page 36: ...Weld334m User s manual F353 ADC Analogue Card 30 WHITE PAGE...
Page 40: ...Weld334m User s manual F364 SEV and F385 SEV Proportional Servovalve Modules 34 WHITE PAGE...
Page 42: ...Weld334m User s manual F359 MCP Memory Card and Printer 36 WHITE PAGE...
Page 54: ...Weld334m User s manual F356 IOE I O Expansion Card 48 WHITE PAGE...
Page 58: ...Weld334m User s manual F376 OPC Field Bus InterBus S Card 52 Card layout...
Page 61: ...Weld334m User s manual F386 Ethernet 100Base T and CANbus module 55 Card layout...
Page 62: ...Weld334m User s manual F386 Ethernet 100Base T and CANbus module 56 WHITE PAGE...
Page 64: ...Weld334m User s manual F383 COM RS422 Serial communication card 58 Card layout...
Page 73: ...Weld334m User s manual 67 APPENDIX...
Page 74: ...Weld334m User s manual 68...
Page 90: ...Weld334m User s manual 84 WHITE PAGE...
Page 92: ......
Page 93: ......
Page 94: ......