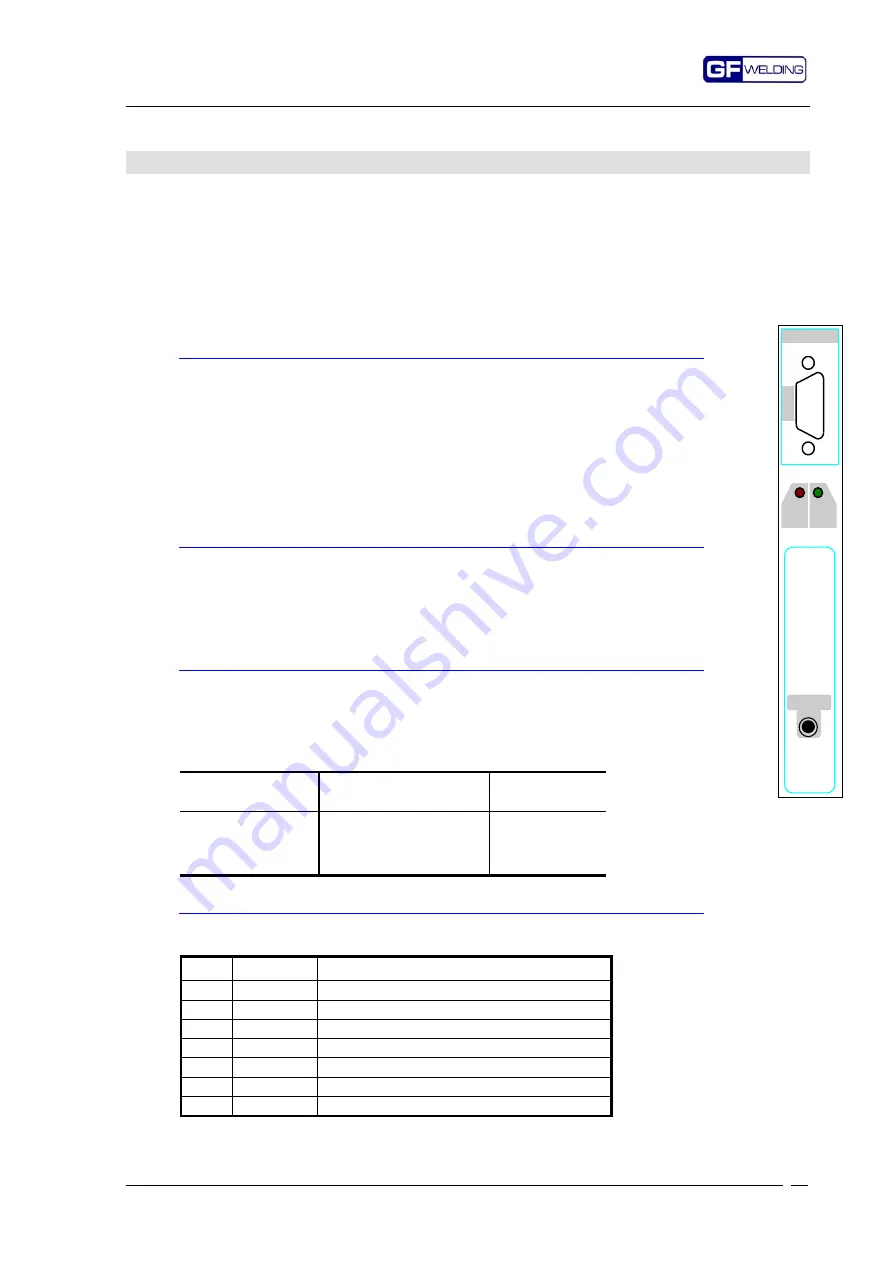
Weld334m - User’s manual
F384-CPU Microprocessor card
25
Code:33038400
5.
F384-CPU Microprocessor card
This is the system calculation centre and it is fitted with a MCU Motorola 68332 card
(20MHz clock). Data and program RAM resides on flash eprom (1MB).
Permanent data is stored in a buffer battery.
The CPU has 2 ports, an RS485 full/duplex port for the HHT4300 programming terminal or
a Laptop (P1 Sub-d 9-way connector located on the front part), and another one for
connecting the multifunctional display (internal port).
CPU status Led indicators:
LOWBATT - Red: illuminated during power reset (when switching on the
Control device) and when the reset is given via the push
button.
If it stays On during the operation (RUN led indicator
illuminated) this indicates that the battery is nearly down.
RUN -
Green: the processor is operating correctly when
illuminated.
This indicator is OFF during the reset or when the Watchdog
(indication of Fault) condition intervenes.
Reset push button
The Reset push button is placed in the lower part, This control has direct
influence on the 68332 and is used (in case of system shutdown) to re-
start the program with no need to cut off power to the control device.
The Reset control is not an alarm reset and it must not be used to this
end.
Internal battery for data backup
Lithium battery with surveying circuit of the charge status and Supercap
(high capacity capacitor) used to store data during the replacement. The
battery is housed in a container which facilitates the replacement.
To replace the battery, refer to Appendix A - Maintenance
Average battery life
Extinction
Operating condition
Duration
(years)
Daily
6 working days
3
Weekly
5 working days
4
Weekly
6 working days
5,4
P1 - 9-way, Sub-d socket connector
RS485 serial communication port for the connection to the HHT4300
programming unit or to a PC
Pin
Signal
Description
1/6
0VH
Earth
2/7
+VH
HHT4300 unit power supply
3
N.C.
Pin bias
4
RXD+
Data rec
5
TXD+
Data transm
8
RXD-
Data reception -
9
TXD-
Data transmission -
Maximum length of connection cable: 100m
RESET
F384-CPU
RUN
LOW
BAT.
P
1
Summary of Contents for Weld334m
Page 1: ...USER S MANUAL Weld334m HC HCM HIC HIM Ed 5 December 2004 Doc 39000326...
Page 6: ...Weld334m User s manual VI WHITE PAGE...
Page 14: ...Weld334m User s manual 8 WHITE PAGE...
Page 28: ...Weld334m User s manual 22 WHITE PAGE...
Page 30: ...Weld334m User s manual F351 BUS Interconnection card 24 WHITE PAGE...
Page 36: ...Weld334m User s manual F353 ADC Analogue Card 30 WHITE PAGE...
Page 40: ...Weld334m User s manual F364 SEV and F385 SEV Proportional Servovalve Modules 34 WHITE PAGE...
Page 42: ...Weld334m User s manual F359 MCP Memory Card and Printer 36 WHITE PAGE...
Page 54: ...Weld334m User s manual F356 IOE I O Expansion Card 48 WHITE PAGE...
Page 58: ...Weld334m User s manual F376 OPC Field Bus InterBus S Card 52 Card layout...
Page 61: ...Weld334m User s manual F386 Ethernet 100Base T and CANbus module 55 Card layout...
Page 62: ...Weld334m User s manual F386 Ethernet 100Base T and CANbus module 56 WHITE PAGE...
Page 64: ...Weld334m User s manual F383 COM RS422 Serial communication card 58 Card layout...
Page 73: ...Weld334m User s manual 67 APPENDIX...
Page 74: ...Weld334m User s manual 68...
Page 90: ...Weld334m User s manual 84 WHITE PAGE...
Page 92: ......
Page 93: ......
Page 94: ......