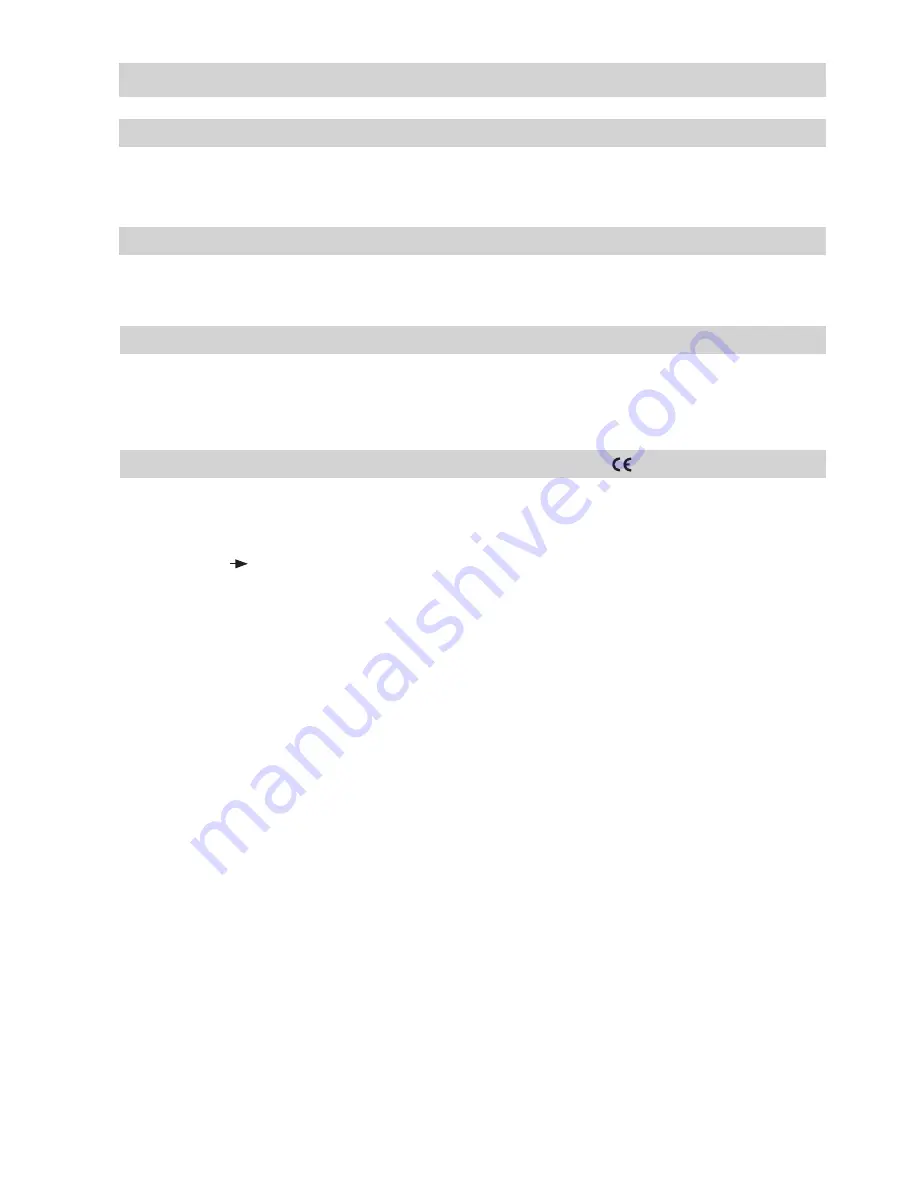
9
Directives and Standards
ATEX (Atmosphère Explosible)
According to the European Directive 2014/34/EU the equipment must
not
be used in explosion risk
areas.
LV (Low Voltage) Directive and EMC (Electromagnetic Compatibility)
The equipment meets the requirements of the Low Voltage Directive 2014/35/EC and the
EMC Directive 2014/30/EC.
Note on the Declaration of Conformity / Manufacturer's Declaration
For details on the conformity of our equipment according to the European Directives see our Declaration
of Conformity or our Declaration of Manufacturer.
The current Declaration of Conformity / Declaration of Manufacturer are available in the Internet under
www.gestra.de Documents or can be requested from us.
The equipment complies with the requirements of the following standards: UL 60950-1 and CSA C22.2
No. 60950-1-07, Information Technology Equipment - Safety - Part 1: General Requirements.
File E176557.
UL/cUL (CSA) Approval
Summary of Contents for SPECTORcontrol II
Page 18: ...18 Commissioning procedure Startup pages ...
Page 26: ...26 For your Notes ...
Page 27: ...27 For your Notes ...