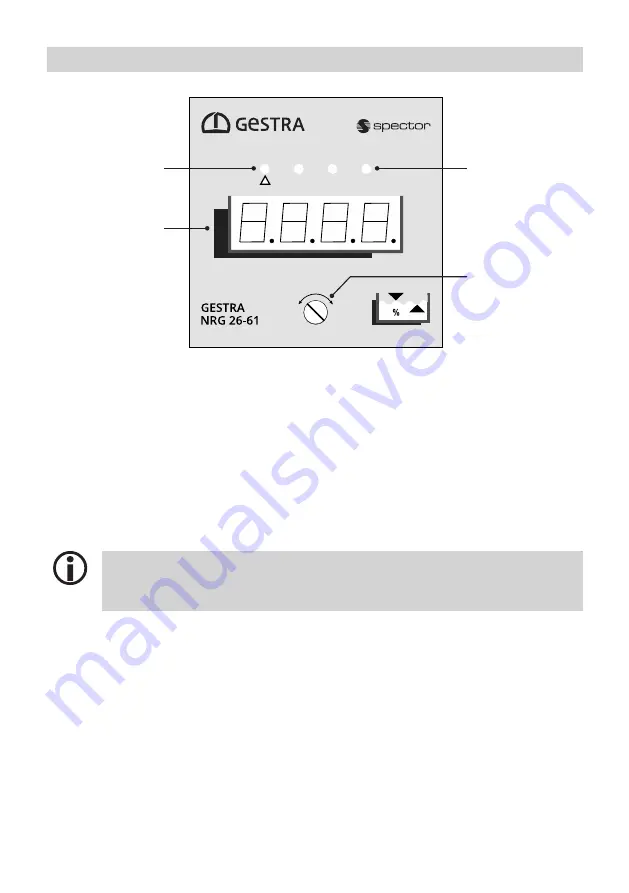
47
NRG 26-61 - Installation & Operating Manual -
819874-00
Starting, operation and testing
Fig. 19
The operating panel:
1
Actual value display/fault code/limit value, green, 4 digits
2
LED 1, alarm/fault, red
3
LED 2, function OK, green
4
Rotary knob/push-button for operation and settings
OK
!
+
-
Notes on the priority of the various indications
Fault indications and alarms are displayed based on their priority. Indications with higher
priority are shown continuously before those with low priority. If several indications need
attention, the display does not alternate between them.
Priority 1 = fault indications as per fault code table, see page 52 ff.
Priority 2 = low-level (LW) alarm
Priority 3 = high-level (HW) alarm
Priority of fault code display
Higher priority fault codes overwrite lower ones on the display!
1
2
4
3