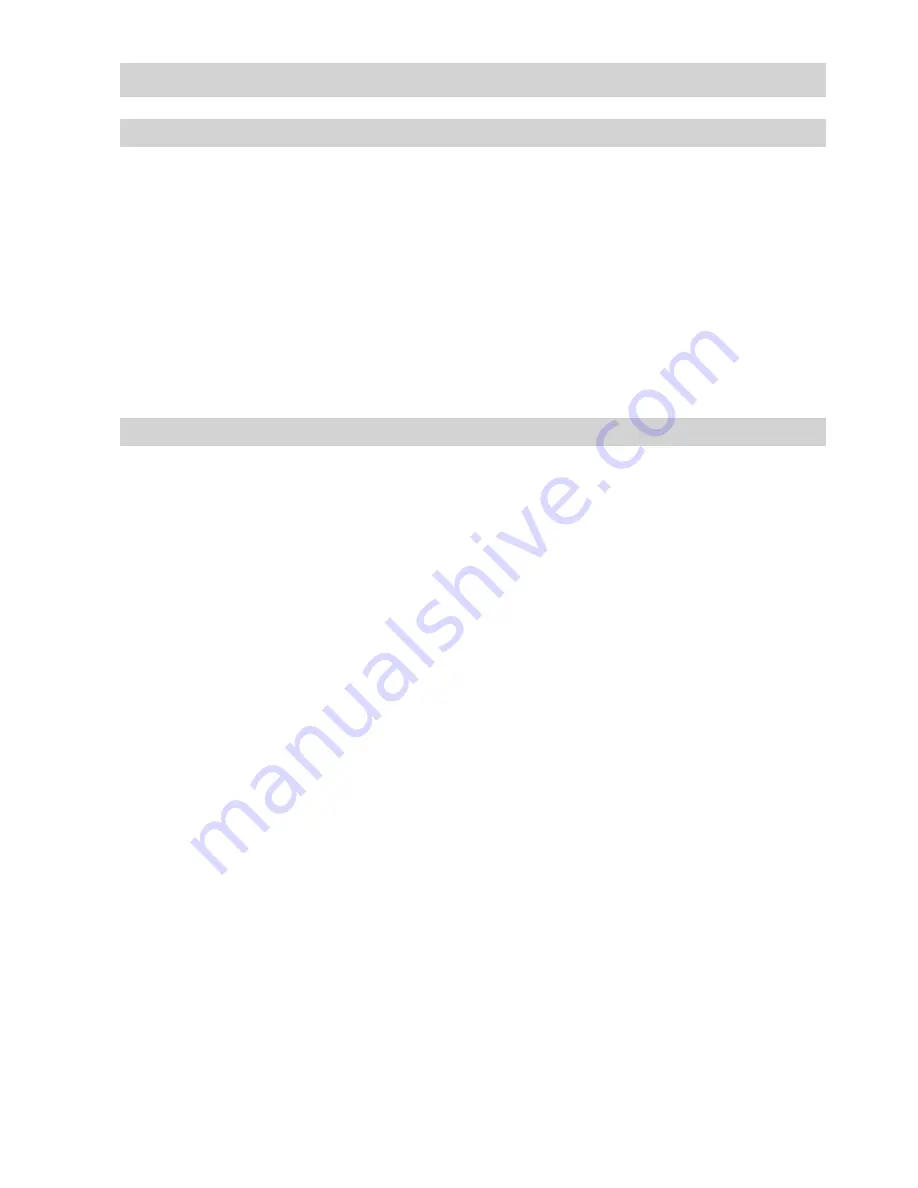
5
Important notes
Usage for the intended purpose
The functional unit consisting of the operating & display unit URB 50 / conductivity controller LRR 1-52,
LRR 1-53 in conjunction with conductivity electrodes LRG 1.-.. and conductivity transmitter LRGT 1.-..
is used as conductivity controller and limiter, for instance in steam boilers, (pressurized) hot-water
installations as well as condensate and feedwater tanks. The conductivity controller indicates when the
preset MAX or MIN conductivity is reached, opens or closes a continuous blowdown valve and may also
control an intermittent blowdown valve.
The conductivity controllers are designed for use with conductivity electrodes and transmitters in the
following equipment combinations: Conductivity controller LRR 1-52 together with conductivity electro-
des LRG 12-2, LRG 16-4, LRG 16-9, LRG 17-1 and LRG 19-1;
Conductivity controller LRR 1-53 together with conductivity transmitters LRGT 16-1, LRGT 16-2 and
LRGT 17-1.
Continuous boiler blowdown (top blowdown)
As the boiler water evaporates, the concentration of non-volatile dissolved solids (TDS) left behind in
the boiler increases over time as a function of steam consumption. If the TDS (= total dissolved solids)
concentration exceeds the limit defined by the boiler manufacturer, foaming and priming occurs as the
density of the boiler water increases, resulting in a carry-over of solids with vapour into steam lines
and superheaters.
As a consequence, the operational safety is impaired and severe damage to boiler and tubes may
occur. To keep the TDS concentration within admissible limits, a certain portion of boiler water must be
removed continuously or periodically (by means of a blowdown valve) and fresh make-up water must
be added to the boiler feed to compensate for the water lost through blowdown.
Electrical conductivity - here as a result of the TDS content of boiler water - is measured in microSie-
mens/cm (μS/cm). However, in some countries ppm (parts per million) is used for conductivity read-
ings. Conversion: 1µS/cm = 0.5 ppm.
Intermittent boiler blowdown (bottom blowdown)
During the evaporation process fine sludge deposits settle on heating surfaces and in the lowest part
of the steam boiler. Boiler sludge is caused e. g. by oxygen-scavenging agents. The accumulated
sludge sediments form a thermally insulating layer and can damage the boiler walls due to excessive
heat. To perform a bottom blowdown the intermittent blowdown valve must be opened abruptly. The
resulting suction effect occurs only at the moment when the valve is being opened, the opening time
should therefore not exceed 3 seconds. Longer blowdown periods will merely waste boiler water.
The timed pulse/interval control of the intermittent blowdown valve optimises sludge removal while
minimising loss of boiler water. The interval between the intermittent blowdown pulses can be set
between 1 and 200 h (intermittent blowdown interval Ti). The duration T of the intermittent blowdown
can be set between 1 and 10 sec. For larger boilers it may be necessary to repeat the intermittent
blowdown pulses. The repetition rate can be set between 1 and 10 with a time interval between 1 - 10
seconds (pulse interval Tp).
External intermittent boiler blowdown
Note that simultaneous intermittent blowdown is not allowed If several steam boilers are connected to
one single blowdown receiver / mixing cooler. In this case the external intermittent blowdown control
unit PRL 50-4 monitors and controls the individual intermittent blowdown operations.
Glossary
Summary of Contents for LRR 1-52
Page 43: ...43 For your Notes ...