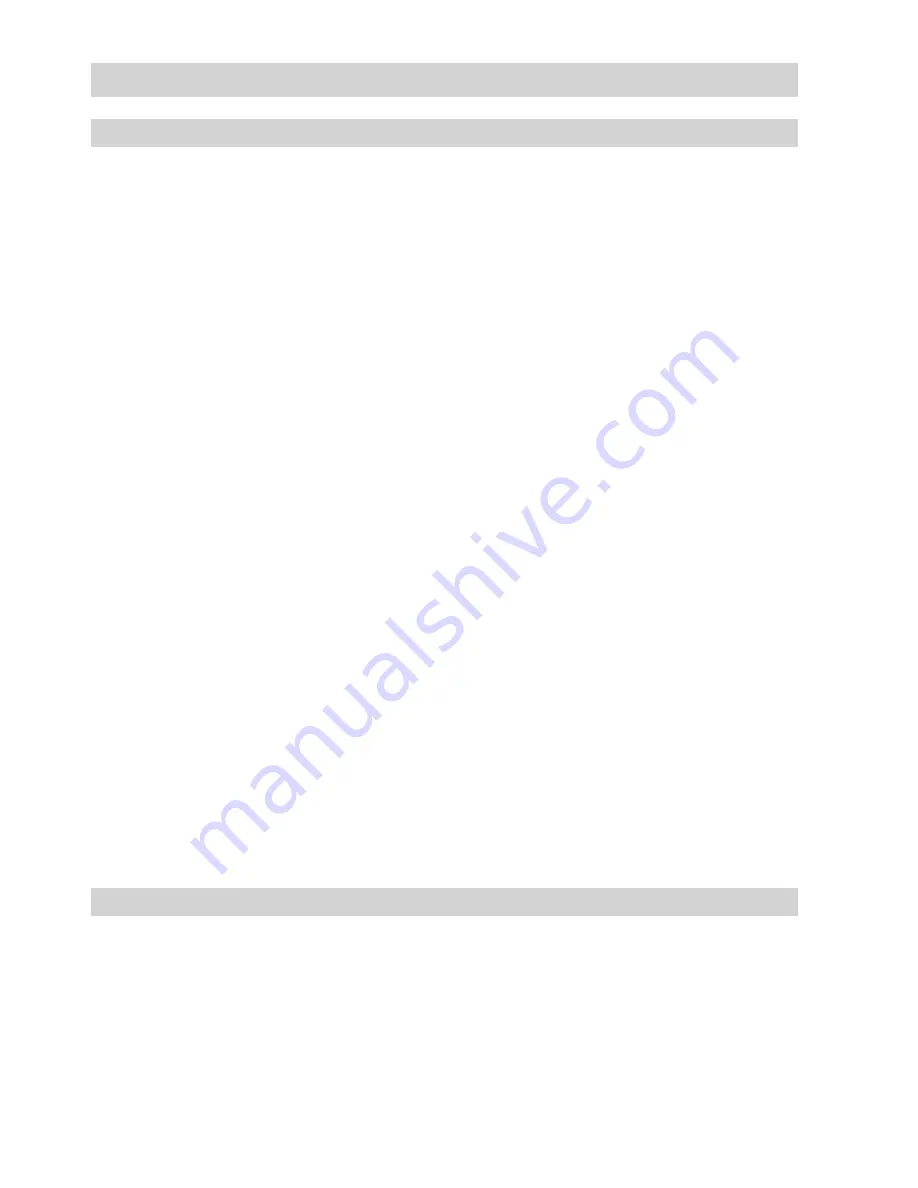
12
URB 50
Supply voltage
24 VDC +/– 20%
Fuse
internal automatic
Power consumption
8 VA
Input / output
Interface for data exchange
Graphic user interface
Analogue resistive touch screen, resolution 480 x 271 pixels, illuminated
Dimensions
Front panel: 147x107 mm
Panel cut-out: 136x96 mm
Depth: 56 + 4 mm
Electrical connection
1 connector with 3 poles,
1 D-SUB connector with 9 poles.
Protection
Front panel: IP 65 to EN 60529
Back: IP 20 to EN 60529
Weight
approx. 1.0 kg
Ambient temperature
when system is switched on: 0 ° .... 55 °C,
during operation: -10 ... 55
°C
Transport temperature
–20 ... +80 °C (<100 hours), defrosting time of the de-energized equipment before it can be put into
operation: 24 hours.
Storage temperature
–20 ... +70 °C, defrosting time of the de-energized equipment before it can be put into operation: 24 hours.
Relative humidity
5 - 85 %, no moisture condensation
Technical data
- continued -
Scope of supply
LRR 1-52
1 Conductivity controller LRR 1-52
1 Installation manual
LRR 1-53
1 Conductivity controller LRR 1-53
1 Installation manual
URB 50
1 Operating & display unit URB 50
1 Data line L = 5m
Summary of Contents for LRR 1-52
Page 43: ...43 For your Notes ...