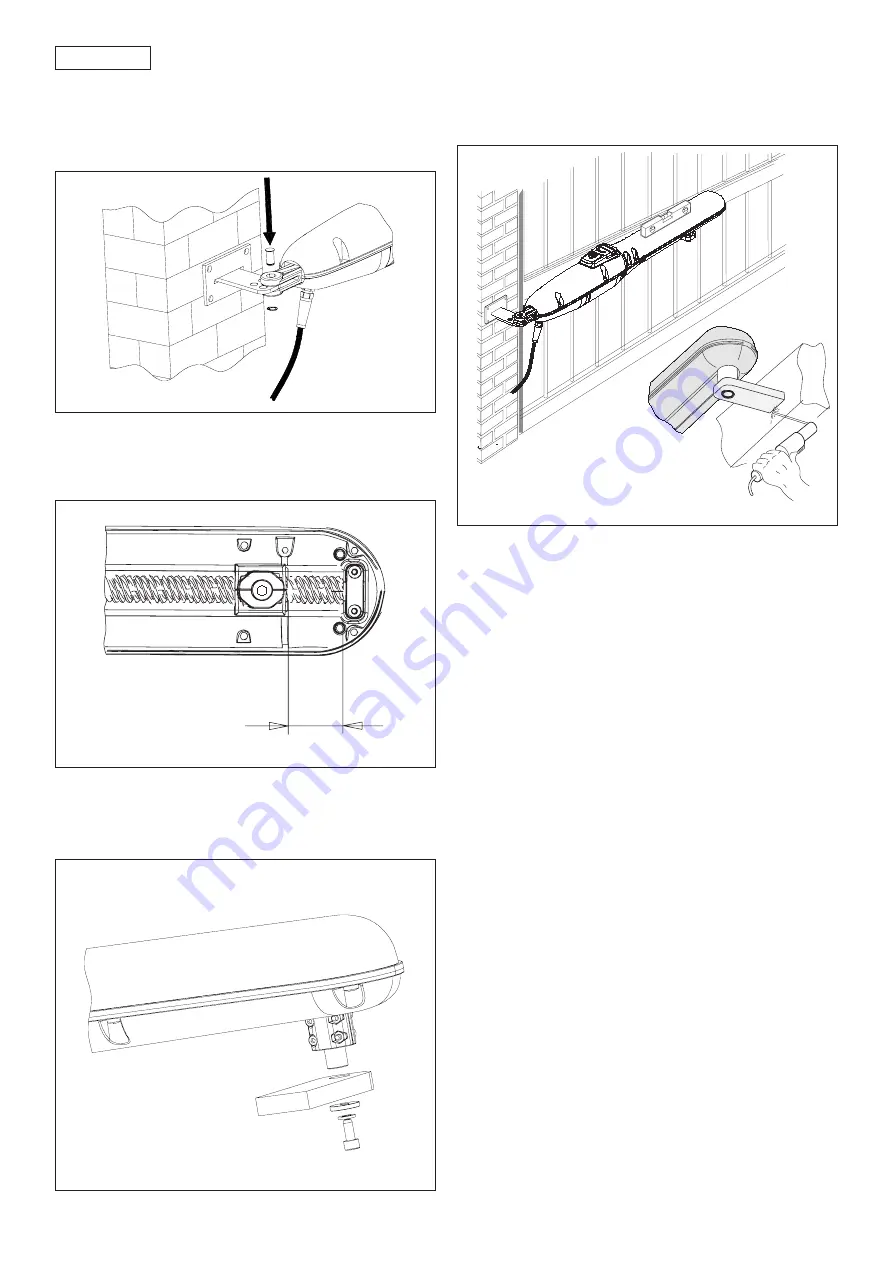
8
ENGLISH
Fig. 6
Fig. 7
Fig. 8
10
2) Secure the articulated fitting of the operator to the rear
bracket by means of the supplied pins (Fig. 5).
Attention:
before securing the operator on the rear
bracket, which has just been welded, make sure its
temperature does not damage the articulated fitting.
3) Power up the motor and move the front attachment pin
backward by about 10 mm (fig. 6).
ATTENTION: The operator can be moved by hand only if
installed on the gate in released position.
4) Fit the front bracket to the front attachment pin as shown
in Fig. 7.
5) Close the gate leaf and, holding the operator in a
perfect horizontal position, locate the front bracket
securing point on the leaf (Fig. 8).
6) Temporarily secure the front bracket on the leaf by
means of two welding points.
Note
: If the fitting cannot be secured firmly due to the
gate structure, a firm resting base on the structure is to
be created.
7) Release the operator and check manually if the gate is
free to open completely up to the mechanical stops and
if the leaf movement is regular and without any friction
whatever.
8) Completely weld the front bracket on the leaf (Fig. 8).
To do this, temporarily release the operator from the
fitting in order to avoid that welding slag damage it.
Note:
We recommend to grease every fixing pin of the
fittings.
9) Carry out the installation of the second operator, if any,
repeating the above mentioned operations.
10) Install the enclosure and the control board keeping into
consideration the overall dimensions given in the relevant
instructions.
6. START-UP
ATTENTION: Before attempting any work on the system or on
the operator, always turn off power.
Observe points 10, 11, 12, 13, 14 of the GENERAL SAFETY
OBLIGATIONS.
Observing the instructions in Fig.3, lay the raceways and
make the electric connections of the control board to the
selected accessories.
Always separate power cables from control and safety
cables (push-button, receiver, photocells, etc...). To prevent
any electric noise whatever, use separate sheaths.
1) Program the control board according to your needs
observing the concerning instructions.
2) Switch on power to the system and check the condition
of the LEDs according to the table of the control board
instructions.
Fig. 5
Summary of Contents for Skill 01
Page 1: ...Skill 01 ...