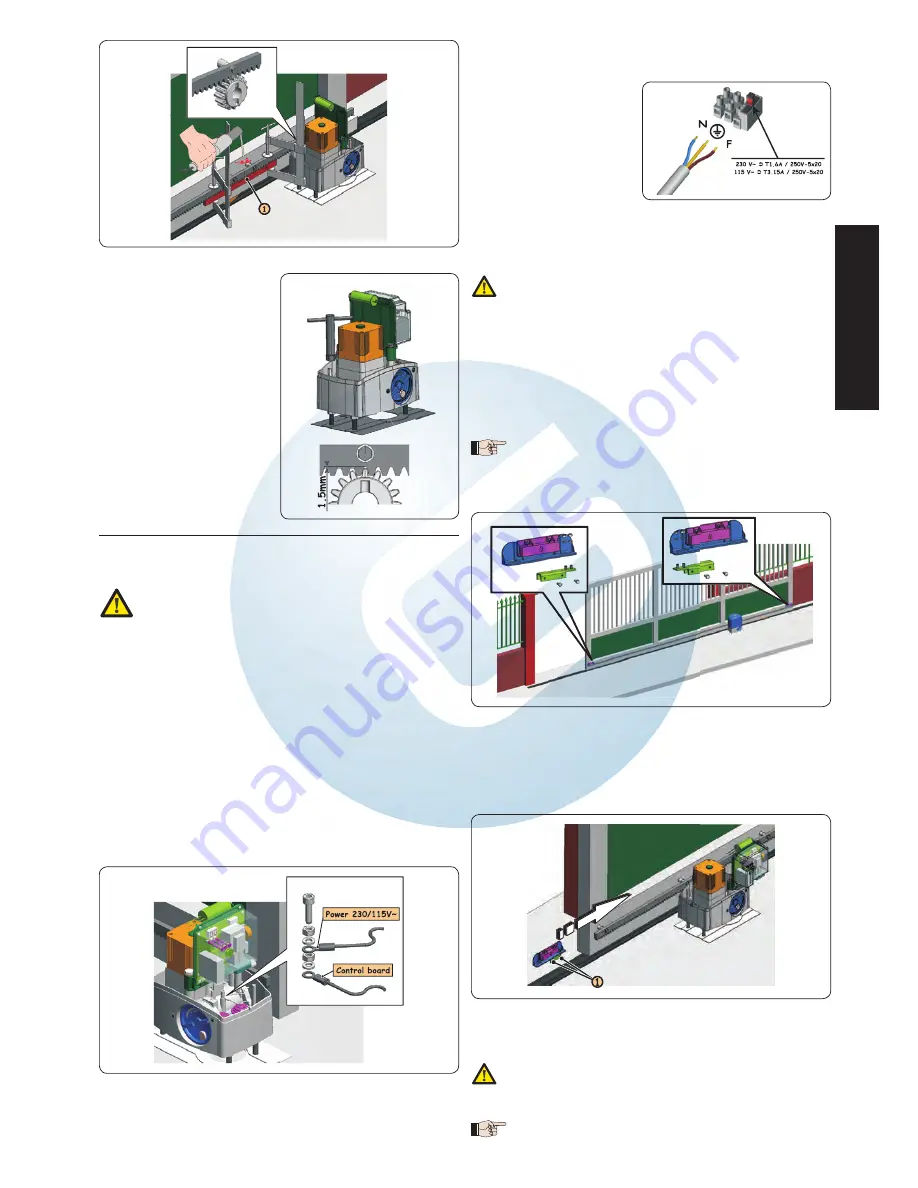
9
ENGLISH
Notes on installing the rack
• Make sure that, during gate travel,
all the rack elements do not come
out of the pinion.
• Do not, on any account, weld the
rack elements either to the spac-
ers or to each other.
• After you have finished installing the
rack, to ensure correct meshing
with the pinion, we advise you to
lower the position of the gearmo-
tor by about 1.5 mm (Fig.15).
• Manually check if the gate correctly
reaches the travel-limit mechani-
cal stops and if there is any friction
during travel.
• Do not use grease or other lubri-
cants between rack and pinion.
6. START-UP
6.1. CONNECTION OF CONTROL BOARD
Before attempting any work on the board (connections, program-
ming, maintenance), always turn off power.
Observe points 10, 11, 12, 13 and 14 of the GENERAL SAFETY RULES.
Follow the instructions in Fig. 3, route the cables in the raceways and make
the electrical connections to the selected accessories.
Always separate power cables from control and safety cables (push-but-
ton, receiver, photocells, etc.). To prevent any electric noise whatever, use
separate sheaths.
6.1.1. EARTHING
Connect the earthing cable as shown in Fig. 16.
6.1.2. CONTROL UNIT
In the “
C
” version gearmotors, the electronic control unit is secured to an
adjustable support with a transparent cover.
The board programming push-buttons are located on the cover - this enables
you to program the board without having to remove the cover.
To connect the control unit correctly, follow the specific instructions.
6.1.3. CONNECTION OF POWER CABLE
(
FOR
F
ALCON
424C
ONLY
)
The
FALCON 424C
gearmotor
houses a screw terminal with fuse-
holder (Fig 17) connected to the
primary circuit of the toroidal tran-
sformer. The mains power cable
230 / 115 V ~ must be connected to
this terminal, respecting what was
specified in Fig. 17. If you have to
replace the fuse, use a fuse type
T1.6A/250V - 5x20 for a 230V power
supply and type T3.15A/250V - 5x20
for a 115V power supply.
6.2. POSITIONING THE TRAVEL-LIMIT ELEMENTS
To correctly position the travel-limit magnets, the control unit must
first be installed and correctly connected to all the command and
safety accessories.
The operator has a magnetic limit switch, which commands gate motion
to stop when the magnet, which is secured to the upper part of the rack,
activates the sensor. The magnets supplied with the operator are specifically
polarised and activate only one of the sensor’s contacts: the closing or
opening contact. The magnet activating the open gate contact bears an
open padlock symbol, and, vice versa, the magnet activating the closed
gate contact bears the closed padlock symbol (see Fig. 18).
Procedure for correct positioning of the two travel-limit magnets:
TTo ensure the operator functions correctly, the magnet showing an
open padlock must be positioned on the left of the operator, looking
at the automated system from the inside. Vice versa, the magnet
showing a closed padlock must be positioned on the right of the
operator.
Assemble the two magnets as shown in Fig. 18.
Set the operator to manual mode operation - as per paragraph 8 - and
power up the system.
Manually take the gate to opening position, leaving 4 cm from the travel
limit mechanical stop.
Slide the magnet nearest to the operator on the rack, in the direction of
the motor - see figure 19. As soon as the LED on the board, referring to
the travel limit stop, goes OFF, take the magnet forward by another 10
mm and fasten it with the appropriate screws (Fig. 19 ref.
).
Do likewise for the other magnet.
Take the gate to about halfway of its travel and relock the system (see
paragraph 9).
Before sending a pulse, make sure that the gate cannot be moved
manually.
Command a complete gate cycle to check if the travel-limit device is
tripping correctly.
To avoid damaging the operator and/or interrupting operation of
the automated system, leave a distance of least 40 mm from the
Fig. 15
Fig. 16
Fig. 18
Fig. 19
Fig. 17
Fig. 14