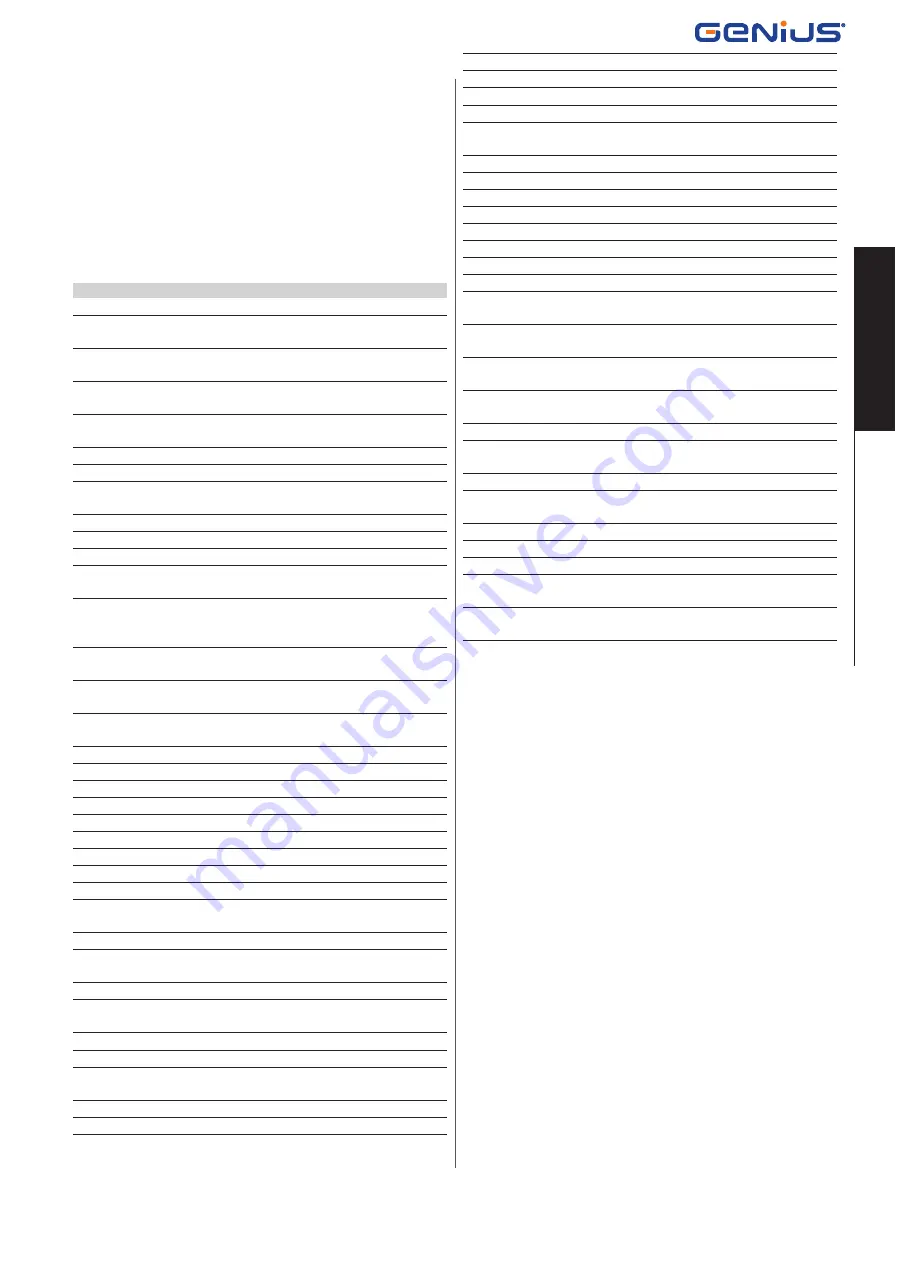
BLIZZARD 500-900
19
532102 - Rev.B
Tr
ansla
tion of the original instruc
tions
ENGLISH
7.1 SCHEDULED MAINTENANCE
The Scheduled Maintenance Table
9
lists the operations which
must be performed on a regular basis in order to keep the automation
system working reliably and safely; these are given purely as a guide-
line and should not be considered exhaustive. The installer/machine
manufacturer is responsible for drawing up the maintenance plan
for the automation system, supplementing this list or modifying the
maintenance operations on the basis of the machine characteristics.
9
Scheduled Maintenance
Operations
Frequency
Structures
Check the slab, the structures and components of the building/fence adjacent
to the automation system, ensuring there is no damage, cracking or subsidence.
12
Check the gate's area of movement, ensuring it is free from obstacles, objects or
deposits which would reduce the effectiveness of the safety measures.
12
Check that there are no gaps in the perimeter fence and that any protective grilles
in the area where it overlaps with the sliding gate section are intact.
12
Ensure that there are no sharp protrusions which could represent a perforation
or hooking hazard.
12
Gate
Check the gate, ensuring it is intact and free of deformations, rust etc.
12
Check that there are no slots/openings on the gate and that any protective
grilles are intact.
12
Check that screws and bolts are correctly tightened.
12
Check that the sliding guides are straight and not excessively worn.
12
Check that the bearings are in good condition and there is no friction.
12
For cantilever systems, check the solidity of the guide system for the suspended
gate section and the counterweight, where present.
12
Check that the mechanical strikes are fastened solidly and in good condition.
This check must be performed on both sides, simulating any knocks which could
occur during use.
12
Check the wheels, ensuring that they are intact, correctly fastened and free of
deformation, wear and rust.
12
Check the rack, ensuring it is straight, spaced correctly from the pinion along its
entire length, and correctly fastened to the gate.
12
Check the containing guide and the anti-tipping column, ensuring they are
correctly fastened and intact.
12
Perform a general clean of the area of movement of the gate.
12
Gear Motor
Check that the gear motor is intact and correctly fastened.
12
Check that the pinion is correctly keyed to the shaft and tightened correctly.
12
Check that the hand guard around the pinion is present and intact.
12
Check that it is irreversible.
12
Check that there is no loss of grease.
12
Check the condition of the gear motor cables, the cable glands and junction boxes. 12
Electronic Equipment
Check that the power supply and connecting cables and the cable glands are
intact.
12
Check that the connectors and wiring are intact.
Check that there are no signs of overheating, burning etc. of electronic com-
ponents.
12
Check that the earth connections are intact.
12
Check the operation of the circuit breaker and RCD.
12
Check that the limit switch is intact and that it operates correctly.
12
Control Devices
Check that the installed devices and remote controls are in good condition and
that they operate correctly.
12
Sensitive Edges
Check condition, fastening and correct operation.
6
Deformable Edges
Check that they are intact and correctly fastened.
12
Photocells
Check condition, fastening and correct operation.
6
Check the posts, ensuring that they are intact, correctly fastened and free of
deformation etc.
6
Flashing Light
Check condition, fastening and correct operation.
12
Electric Locks
Check condition, fastening and correct operation.
12
Clean the seats.
12
Access Controls
Check that the gate opens only when an authorised user is recognised.
12
Complete Automation System
Check that the automation system operates correctly, following the set logic,
when using the various control devices.
12
Check that the gate moves correctly - smooth, regular and without abnormal
noise.
12
Check that both the opening and closing speed are correct and that the stop
positions and slow-downs provided for are respected.
12
Check that the manual release operates correctly: when the release mechanism
is activated, it must only be possible to move the gate manually.
6
Check that the caps on the locks are present.
Check that the maximum force required for manual movement of the gate is
below 225 N in residential areas and 390 N in industrial or commercial settings.
6
Check that the safety edges operate correctly when faced with an obstacle.
6
Check that the encoder (where present) functions correctly when an obstacle
is detected.
6
Check that each pair of photocells is working correctly.
6
Check that there is no optical/light interference between the pairs of photocells. 6
Check the force limitation curve (per EN 12453).
6
Check that all necessary signage and warnings are present, intact and legible:
residual risks, exclusive use etc.
12
Check that the gate's CE marking and the DANGER, AUTOMATIC MOVEMENT
warning signage is present, intact and legible.
12