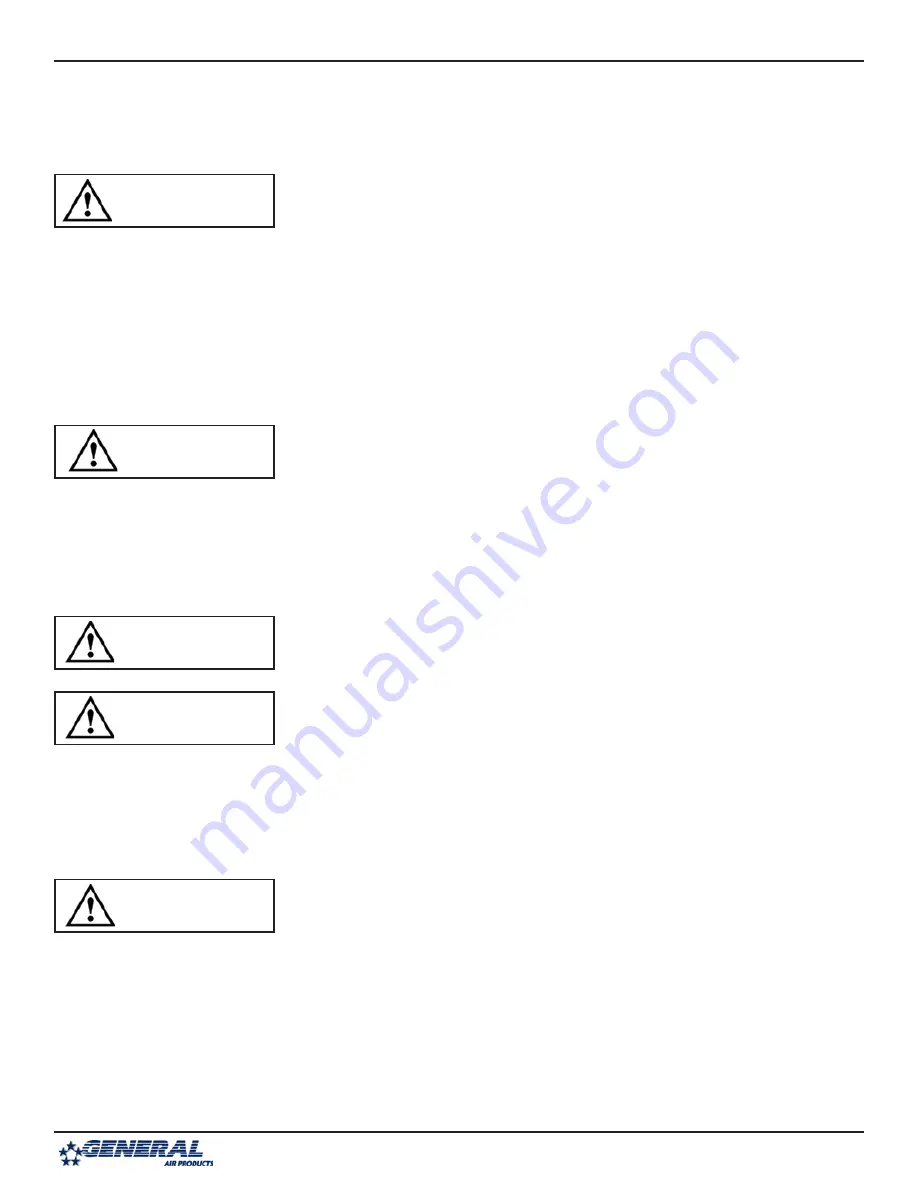
Section 1 - Installation Instructions (cont’d)
1.3 Connecting Voltage
Connect supply voltage to separate line terminals L1, L2 and L3 on terminal block. All wiring must conform to the
National Electrical Code (NEC) and any local or building codes.
Wire size must be capable of carrying the unit load without dropping the voltage at the
terminals below normal operating levels. Check incoming wire size; if there are
any questions please contact us.
Check all wire connections in control cabinet, since
they may loosen during shipment.
Be sure the control power transformer has its primary side jumpers connected to match the incoming supply
voltage. Each unit is run at the factory. Motor rotation will always need to be checked. After connecting the power, use the
on/off switch on the front of the unit to turn on the compressor briefly to check rotation. An indicating arrow is on the
compressor flywheel. If rotation is not correct on three phase units, reverse any two leads.
On single phase units refer to the motor nameplate, however it should not require changing as it has been run at
the factory. If you feel this is required please consult with factory personnel as there may have been changes made to the
unit, which should be discussed with the factory PRIOR TO starting the unit. Please ensure sufficient power is available at
the unit. Long feed line runs can cause voltage drops, which can affect the performance of the unit and damage the motor.
Only qualified electrical personnel should connect the unit.
1.4 Prior Run Time
Each Dry Air Pac is shipped with desiccant installed. Run the unit for a 1/2 hour before connecting to the sprinkler
system. This will allow the desiccant to become conditioned to the proper dew point. Throttle outlet valve to maintain air
drying tower pressure between 70 psig and 100 psig during this period.
The Dry Air Pac should not run for more than 40 minutes in any given hour.
If you are connecting to an old piping system there may be existing leaks in the system
which cause the compressor to cycle more frequently than 4 times per hour. If this is
the case there are three suggestions: 1. Fix the leaks. 2. Add a second Dry Air Pac to
provide enough air to bring the cycle times back to less than 4 times per hour. 3. Add
a receiver, which can act as a storage buffer to supply more air to the system. This should be discussed with factory personnel,
as it will only work in cases where minor leaks are involved.
1.5 Filter
The Dry Air Pac is supplied with a removable, threaded inlet air filter so that if the AHJ requires air to be drawn from
the cold room this can be done.
These units have been FM Approved with air not being drawn from the freezer room.
Therefore we do not recommend they be connected to the freezer room.
The Dry Air Pac is designed so that performance will not be adversely affected with the filter left in place directly
on the compressor. If connected in the cold room, the piping back to the compressor must be 1 1/2" minimum pipe size for
this run, bushed down directly at the compressor inlet. This pipe must be heat traced and insulated. The inlet filter should
be mounted on the inlet end of this pipe directly in the cold room. The interconnecting piping must be clean of any foreign
matter, which may be drawn into the compressor and cause damage.
1.6 Dew Point Monitor
There is a 1/2" pipe plug installed in the outlet tee. This is provided as a point to install a dew point monitoring
device, should you require one. This is after the regulator and gives you the pressure dew point of the system. Be careful
to follow the dew point monitor manufacturer's recommendations regarding installation.
1-800-345-8207
CAUTION
DANGER
NOTICE
NOTICE
NOTICE