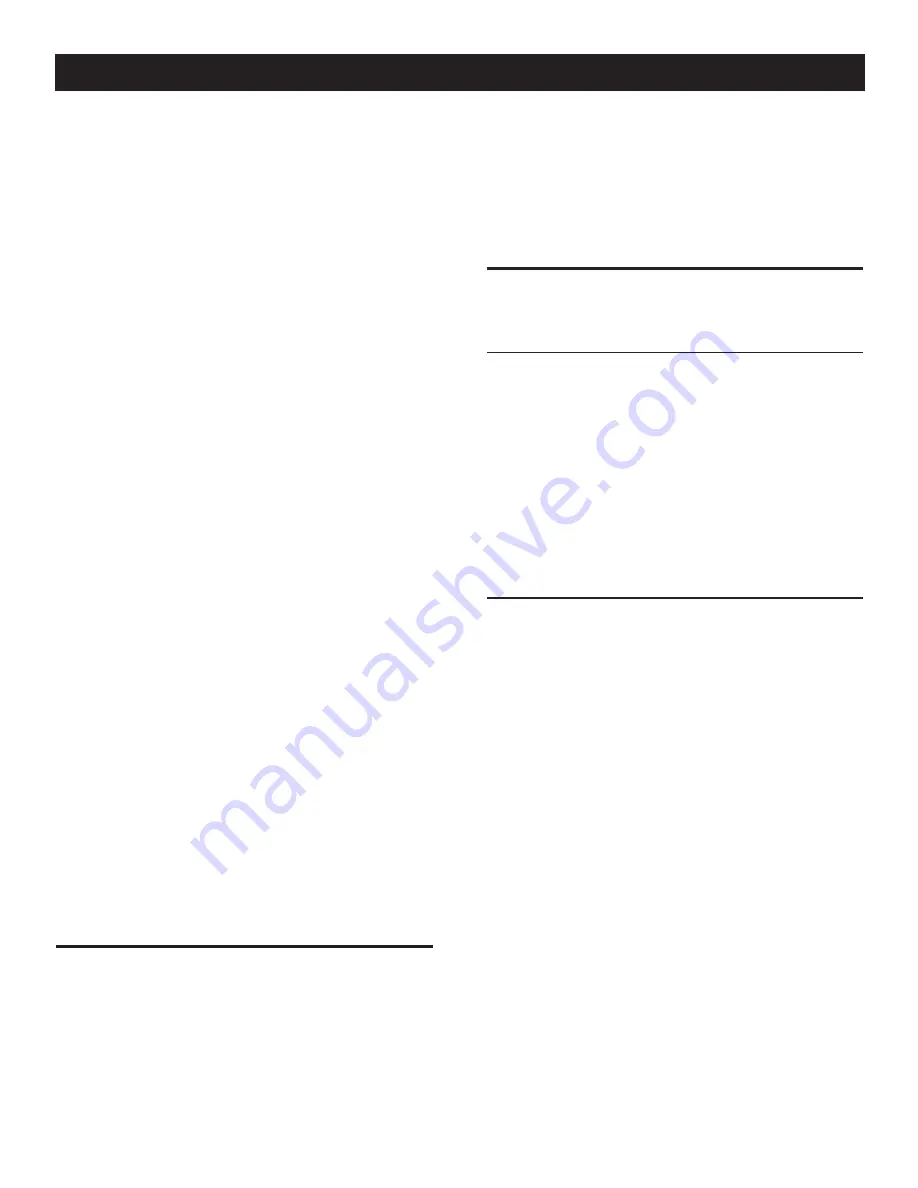
13
This test will be performed each time the controller is powered up.
Upon first power up of the generator, the display interface will
begin an installation assistant. The assistant will prompt the user
to set the minimum settings to operate. These settings are sim-
ply: Current Date/Time and Exercise Day/Time. The maintenance
intervals will be initialized when the exercise time is entered (Figure
3.1).
The exercise settings can be changed at any time via the "EDIT"
menu (see Appendix, "Menu System").
If the 12 volt battery is disconnected or the fuse removed, the
Installation Assistant will operate upon power restoration. The
only difference is the display will only prompt the customer for the
current Time and Date.
IF THE INSTALLER TESTS THE GENERATOR PRIOR TO
INSTALLATION, PRESS THE “ENTER” KEY TO AVOID SETTING
UP THE EXERCISE TIME. THIS WILL ENSURE THAT WHEN
THE CUSTOMER POWERS UP THE UNIT, HE WILL STILL BE
PROMPTED TO ENTER AN EXERCISE TIME.
NOTE:
The exerciser will only work in the AUTO mode and will not work
unless this procedure is performed. The current date/time will
need to be reset every time the 12 volt battery is disconnected
and then reconnected, and/or when the fuse is removed.
Display Interface Menus
The LCD display is organized as detailed below:
• The “Home” page, this page is the default page which will be
displayed if no keys are pressed for 30 seconds. This page
normally shows the current Status message and the current
date and time. The highest priority active Alarm and/or Warning
will be automatically posted on this page as well as flashing
the backlight when such an event is detected. In the case of
multiple Alarms or Warnings, only the first message will be
displayed. To clear an Alarm or Warning, see the Protection
Systems section - Clear Alarm.
• The display backlight is normally off. If the user presses any
key, the backlight will come on automatically and remain on for
30 seconds after the last key was pressed.
• The “Main Menu” page will allow the user to navigate to all other
pages or sub-menus by using the Left/Right and Enter keys.
This page can be accessed at any time with several presses of
the dedicated Escape key. Each press of the Escape key takes
you back to the previous menu until the main menu is reached.
This page displays the following options: HISTORY; STATUS;
EDIT; AND DEBUG. (See the Appendix - "Menu System".)
3.2
AUTOMATIC TRANSFER
OPERATION
To select automatic operation, do the following:
1. Make sure the transfer switch main contacts are set to their
UTILITY position, i.e., loads connected to the utility power
source.
2. Be sure that normal UTILITY power source voltage is avail-
able to transfer switch terminal lugs N1 and N2 (Refer to the
Electrical Data section).
3. Set the generator’s AUTO/OFF/MANUAL switch to AUTO.
4. Set the generator’s main circuit breaker to its ON (or CLOSED)
position.
With the preceding steps complete, the generator will start auto-
matically when utility source voltage drops below a preset level.
After the unit starts, loads are transferred to the standby power
source. Refer to the Sequence of Automatic Operation section.
3.3
SEQUENCE OF AUTOMATIC
OPERATION
3.3.1 UTILITY
FAILURE
Initial Conditions: Generator in Auto, ready to run, load being sup-
plied by utility source. When utility fails (below 60% of nominal),
a 10 second line interrupt delay time is started. If the utility is still
gone when the timer expires, the engine will crank and start. Once
started, a five (5) second engine warm-up timer will be initiated.
When the warm-up timer expires, the control will transfer the load
to the generator. If the utility power is restored (above 80% of
nominal) at any time from the initiation of the engine start until the
generator is ready to accept load (5 second warm-up time has not
elapsed), the controller will complete the start cycle and run the
generator through its normal cool down cycle; however, the load
will remain on the utility source.
3.3.2 CRANKING
The system will control the cyclic cranking as follows: 16 second
crank, seven (7) second rest, 16 second crank, seven (7) second
rest followed by three (3) additional cycles of seven (7) second
cranks followed by seven (7) second rests.
Choke Operation
1. The 990cc engines have an electric choke in the air box that
is automatically controlled by the electronic control board.
2. The 530cc engines have an electric choke on the divider panel
air inlet hose that is automatically controlled by the electronic
control board.
Failure to Start
This is defined as any of the following occurrences during crank-
ing:
1. Not reaching starter dropout within the specified crank cycle.
Starter dropout is defined as four (4) cycles at 1,000 RPM.
2. Reaching starter dropout, but then not reaching 2200 RPM
within 15 seconds. In this case the control board will go into
a rest cycle for seven (7) seconds, then continue the rest of
the crank cycle.
During a rest cycle the start and fuel outputs are de-energized and
the magneto output is shorted to ground.
Cranking Conditions
The following notes apply during cranking cycle.
1. Starter motor will not engage within five (5) seconds of the
engine shutting down.
2. The fuel output will not be energized with the starter.
3. The starter and magneto outputs will be energized together.
Operation
Summary of Contents for 0j2083
Page 30: ...28 Installation Diagrams Drawing No 0J3244 B ...
Page 31: ...29 Drawing No 0J3244 B Installation Diagrams ...
Page 32: ...Part No 0J2083 Revision G 04 02 13 Printed in U S A ...
Page 61: ...59 59 Notas ...
Page 62: ...Nº de parte 0J2083 Revisión G 02 04 13 Impreso en EE UU ...
Page 90: ...88 ДЛЯ ЗАМЕТОК ...
Page 91: ...89 89 ДЛЯ ЗАМЕТОК ...
Page 92: ... элемента 0J2083 Редакция G 04 02 13 Напечатано в США ...