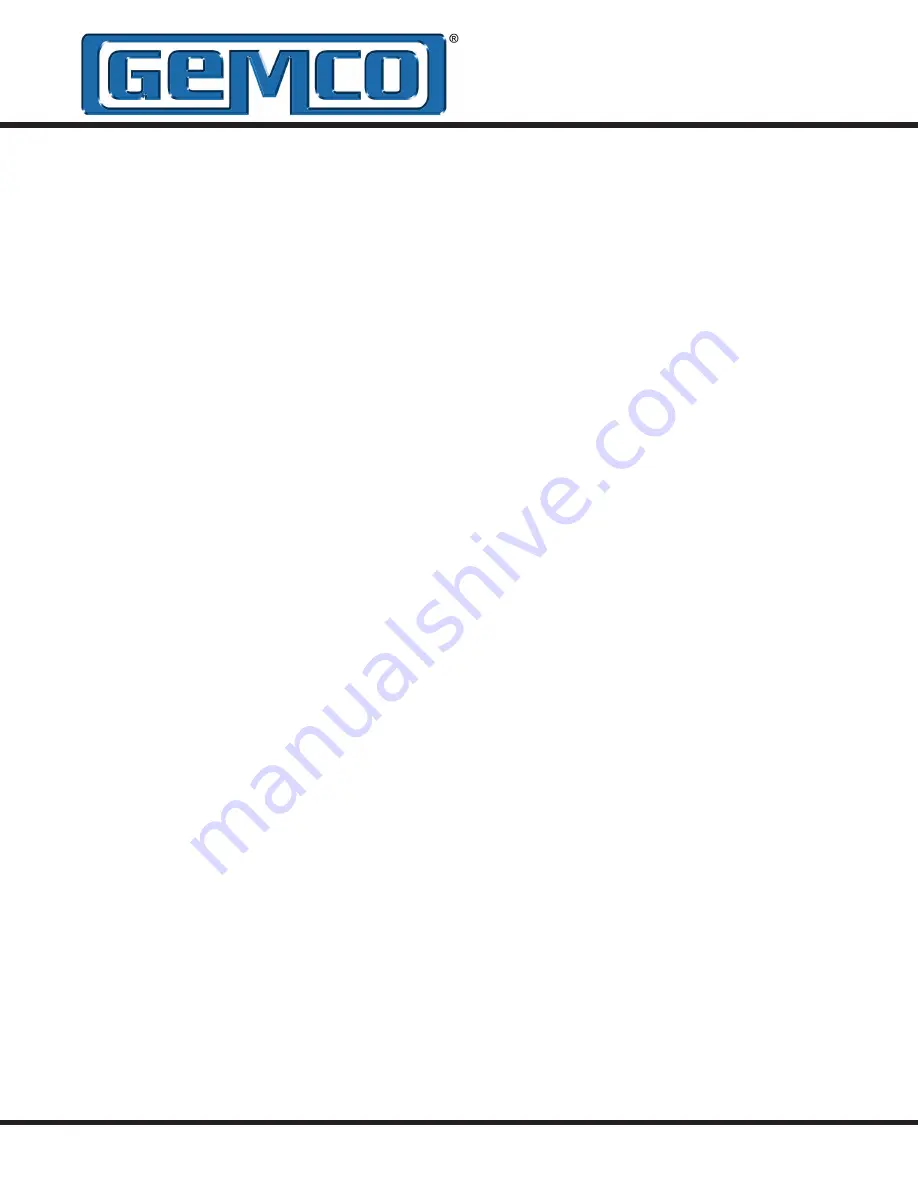
Toll Free: 800-635-0289 • Email: [email protected] • Web: www.ametekfactoryautomation.com
Mounting the Magnet Assembly
Before mounting the magnet assembly, the following
should be considered:
• Ferromagnetic material should not be placed
closer than 0.25” from the LDT’s magnet
assembly or rod end. Failure to do so could
cause erratic operations. Non-ferrous materials,
such as brass, copper, aluminum, non-magnetic
stainless steel, or plastics, can be in direct
contact with the magnet assembly and rod end
without producing any adverse results.
• Minimal clearance between the LDT’s rod and
the magnet assembly through the full stroke is
required. Stress between the magnet and the
rod can cause flexing of the mounting brackets.
This may appear as nonlinearity.
• LDTs using a split magnet assembly must keep
the diameter of the magnet assembly around
the rod throughout the complete stroke. The
diameter of this magnet assembly should not be
farther than 0.2” away from the rod. Split magnet
assemblies outside this range will cause signal
loss.
To install the magnet assembly, perform the
following steps:
1. Slide the magnet assembly over the LDT rod.
2. Mount the magnet to the non-ferrous, movable
portion of the device being controlled using non-
ferrous screws.
2.2: Installing the LDT in a
Hydraulic Cylinder
Before installing an LDT in a hydraulic cylinder, note
the following considerations. Items discussed in this
section are found in Figures 1-1 and 2-1.
• A non-ferrous spacer must be used to separate
the magnet assembly from the head of the
piston rod. See Figure 2-1.
• The magnet should not be closer than 2.0”
from the base of the LDT’s hex head
when the
piston rod is fully retracted. In instances where
space restraints exist, it may be required to
countersink the magnet into the piston rod.
Two magnets are available for mounting to
the piston: the standard 1.29" in diameter
(part number SD0400800) four-hole magnet
and a 1.0" magnet (part number SD0410300)
designed exclusively for countersunk mounting
applications. The 1.0" magnet must be held
captive with a snap ring.
• An O-ring groove is provided at the base of the
LDT’s mounting hex for pressure sealing. The
O-Ring seal was designed to meet Mil-Std-
MS33656. Refer to SAE J514 or SAE J1926/1
for machining of mating surfaces.
• It is recommended that a chamfered rod
bushing be used with LDTs having a rod 60.0”
or longer in length. On applications with rods
of this length, a chamfered rod bushing in front
of the magnet may be required. This bushing
will prevent wear on the magnet assembly
(wear occurs as the piston retracts from
extended lengths). This rod bushing should be
manufactured from a high wear polymer, such
as Teflon®.
• It is recommended the bore for the cylinder
piston rod have an inside diameter of at least
0.50”. The LDT rod has an outside diameter of
0.405”. Use standard practices for machining
and mounting these components. Consult the
cylinder manufacturer for details on applicable
SAE or military specifications.
Before performing the following steps for installing
the LDT into a hydraulic cylinder, it may be
necessary to perform machining and mounting
operations on the hydraulic cylinder. Consult the
information and specifications provided by the
cylinder manufacturer before beginning the following
steps:
1. Unscrew the LDT’s jam nut from the threads
protruding from the hex mounting base.
5