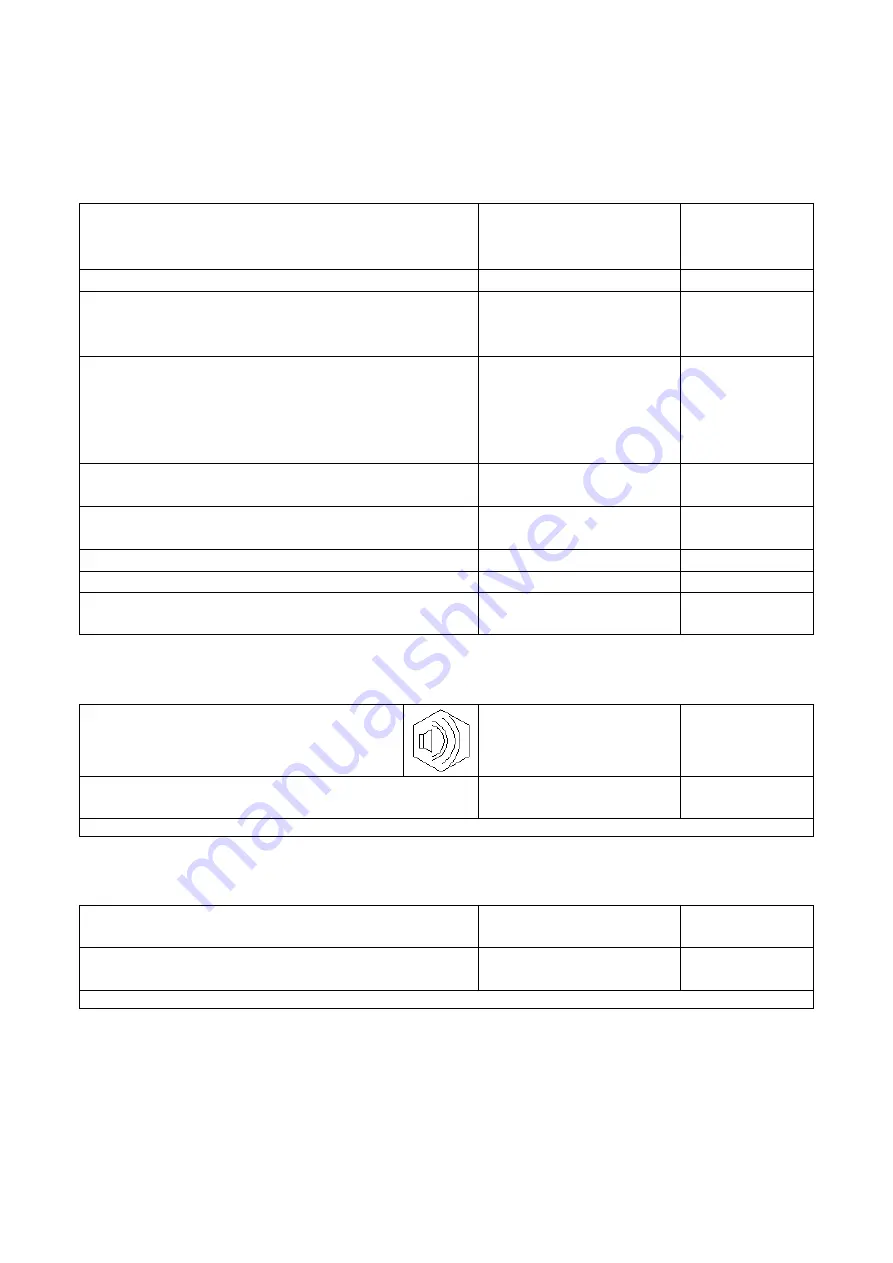
GEAX
s.r.l
Chapter 8
GENERAL DESCRIPTION OF DRILLING RIG
2
8.3 Technical data
8.3.1
Mechanical specifications
Rotary head
Max. torque
7500
[DaNm]
Max. drilling depth:
16,5
[m]
Tool diameter
Max.
Min.
0.75
0.3
[m]
[m]
Mast adjustment in working position:
Rotation on transverse plane
Rotation on longitudinal plane
±5
±5
[°]
[°]
Main winch
Max. pull
12000 x 3
[DaN]
Auxiliary winch
Max. pull
3700
[DaN]
Mass (without accessories)
24000
[kg]
Tracked crawler
JCB JS160 NLC
Diesel engine
power
93
[kW]
8.3.2
Noise levels
LwA
Acoustic power level of airborne noise
102
dB(A)
LpA
Noise level inside operator's control cab
70
dB(A)
Note: Measurements made in accordance with standard 2000/14/CE, UNI EN 791/1997
8.3.3
Vibration level
Acceleration on operator's hands and arms
< 2.5
[ m/sec
2
]
Acceleration on operator's body
< 0.5
[ m/sec
2
]
Note: Measurements made in accordance with standards ISO 2631/1, ISO 5349, SAE J1166