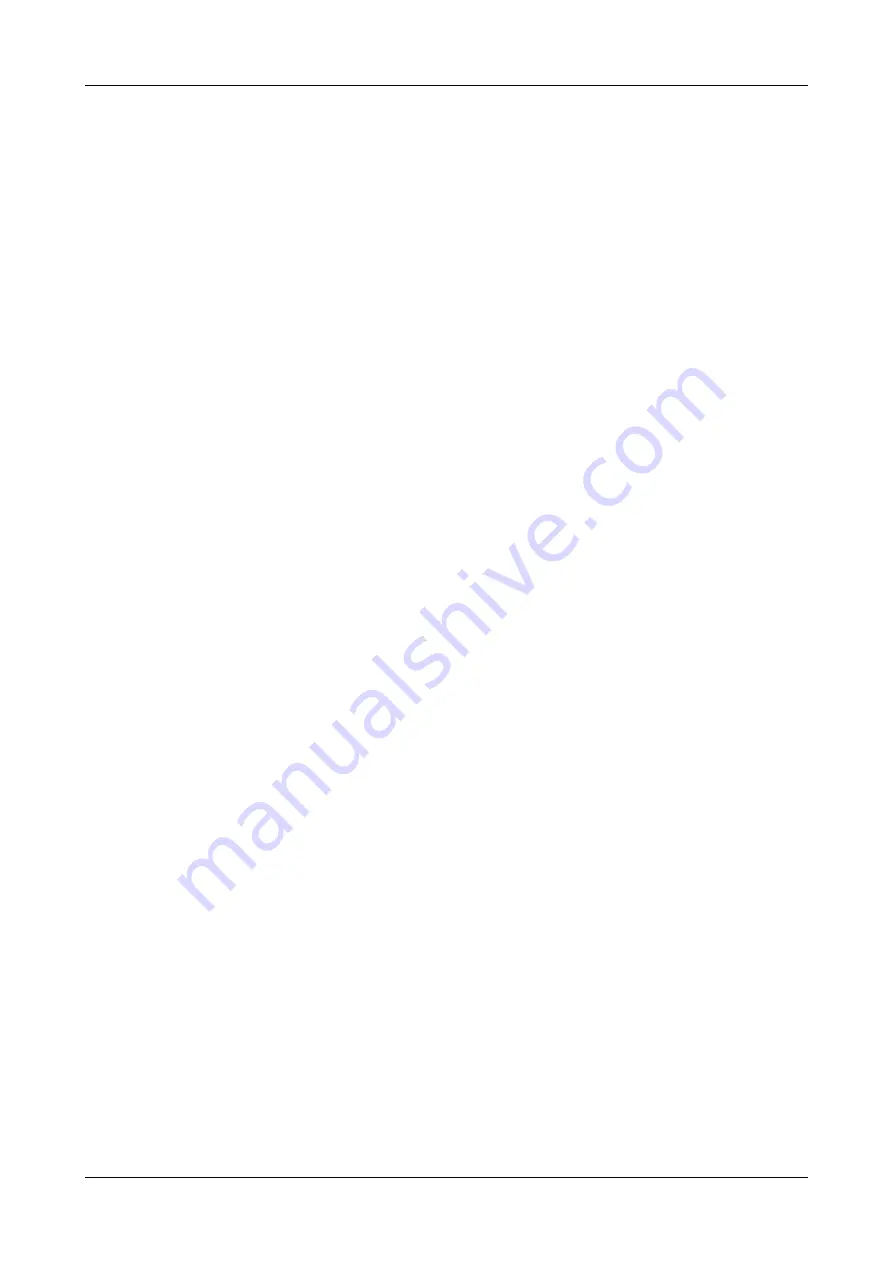
4.
Screw the switch bar T.VIS (1) into the adapters T.VIS E / SHO (139) and
tighten with jaw wrench at (1.2), torque 2 Nm.
5.
Place the control top over the T.VIS switch bar (1) and on the actuator.
6.
Tighten the clamp connection (15) with screws (39) at a torque of 1 Nm.
7.
Align the pneumatic and electrical connections in accordance with the valve
block configuration.
!
Internal air guiding is not possible on these valve types. Therefore connect
the air connection (Y1) on the control top and the connection (A.4.2) on the
actuator to the air hose (L).
8.
Carry out commissioning, see Chapter 7, Page 74.
®
Done.
Assembly and installation
Mounting the control top to different valves
430BAL013985EN_6
25.04.2023
71