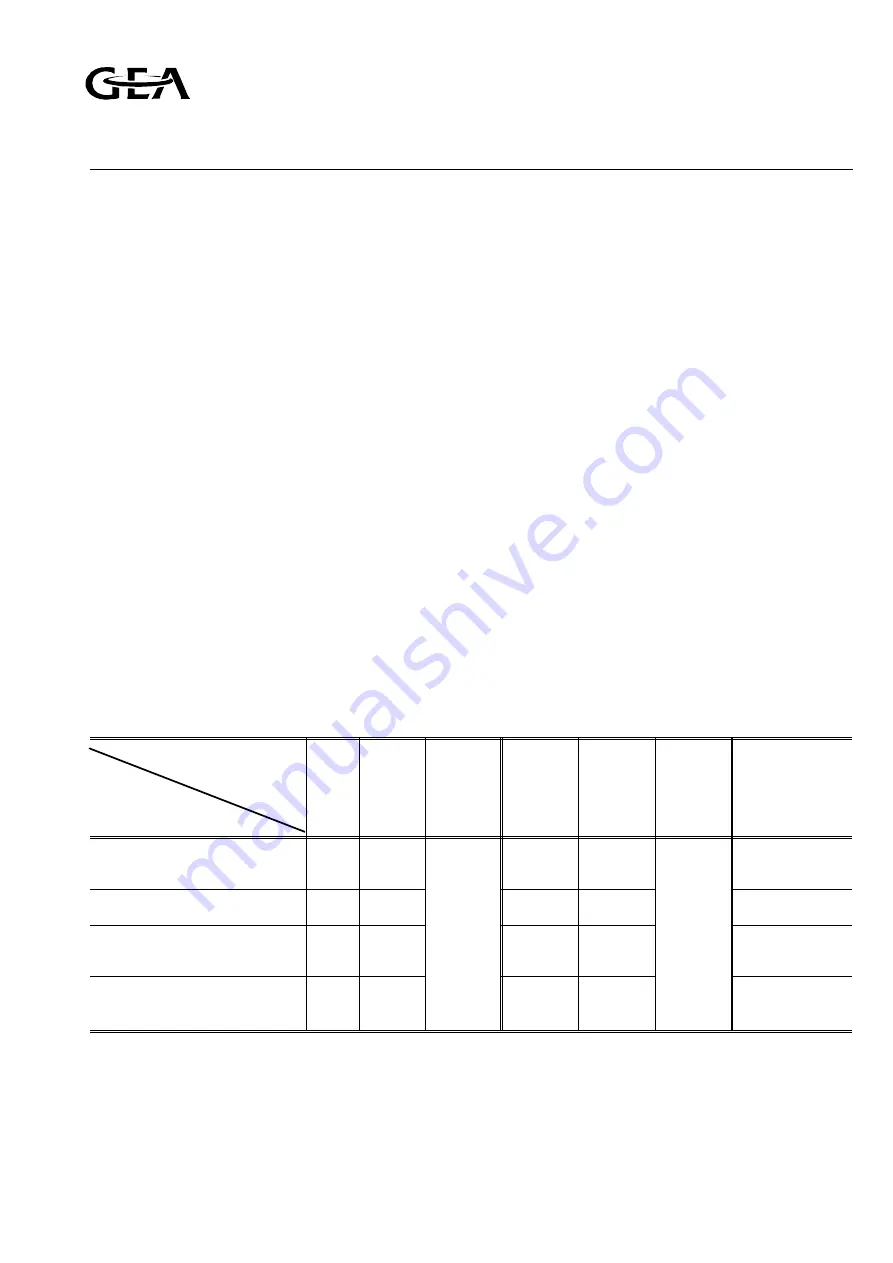
Besides the inspection during operation described in
chapter 8, the compressor requires regular
maintenance. This maintenance is limited to topping
up or changing the lubricating oil, regular cleaning of
oil filters and gas suction strainer and to the
inspection of suction and discharge valves; these
operations can be carried out by the operating
personnel. Moreover, it is recommended to have the
compressor inspected annually by the installation
engineer, irrespective of the number of operating
hours. A major inspection should at any rate be
carried out after every 10,000 operating hours.
9.1 MAINTENANCE SCHEDULE
The maintenance schedule below indicates after
how many operating hours maintenance
operations have to be carried out. This schedule
can be regarded as a directive, based on the
experience gained with a large number of
compressors.
For most of the maintenance operations the
compressor must be put out of action. In order to
avoid that this should take place at inconvenient
times, the operations should as much as possible
be affected during a stand-still period. The
schedule has been drawn up in such a way that
several operations can be carried out
sumultaneously, which results in reduced
maintenance costs.
9.2 LUBRICATION DATA
The types of oil mentioned in table 3.1 on page
3.3 have the required properties and may
therefore be used.
The choice of the type of oil depends on the
operating conditions of the compressor and the
refrigerant used; this choice should therefore be
left up to the installation engineer’s decision. It is
emphatically pointed out that it is not permitted
to mix different types of oil.
If another type of oil is used, first remove all stale
oil, consequently also the oil in the filters, oil
pump, crankcase, shaft seal, oil separator and oil
drains of the installation. Oil change must take
place as soon as the oil is dirty. Dirty oil is dark
coloured and hardly transparent. In order to find
out if it is necessary to change oil, a slight quantity
of oil should be drained via the oil drain valve and
compared with fresh oil.
9.3 TOPPING UP OIL WITH COMPRESSOR
OPERATING
Topping up oil may be carried out with the
compressor operating. Use the same oil as present
in the compressor (refer to the listed oil on table
3.1). Without affecting the operation of the
compressor, the oil may be topped up by means
MAINTENANCE SCHEDULE
Number of
operating
hours 100
1
)
2500
2
)
5000
7500
2
)
10,000
10,100
12,500
2
)
15,000
17,500
2
)
20,000
etc.
Maintenance
Cleaning of oil suction filter and
renewal of oil discharge filter
(ref. to par. 9.6).
×
×
Maj
or
ins
pe
ct
ion
to
b
e
ca
rrie
d
ou
t
by
ins
ta
lla
ti
on
e
ng
ine
e
r
×
×
Maj
or
ins
pe
ct
ion
to
b
e
ca
rrie
d
ou
t
by
ins
ta
lla
ti
on
e
ng
ine
e
r
Cleaning of suction gas strainer
(ref. to par. 9.7).
×
×
×
Inspection of suction and
discharge valves
(ref. to par. 9.8)
×
×
Draining and change of oil
3)
(ref. to par. 9.5).
×
×
×
×
1
) time dependent on pollution.
2
) Only for NH
3
-compressors
3
) In the case of a possible rapid pollution of the oil, it should be drained and renewed sooner than at the times given
above.
For most of the maintenance operations the compressor must be evacuated before in order to remove
the refrigerant gas. after completion of the operations the compressor has to be purged. Both compres-
sor evacuation and purging are dealt within this chapter.
Refrigeration Division
Grasso
9. COMPRESSOR MAINTENANCE
v003.98.11.en
Refrigeration Compressors Series RC9
Page 9.1