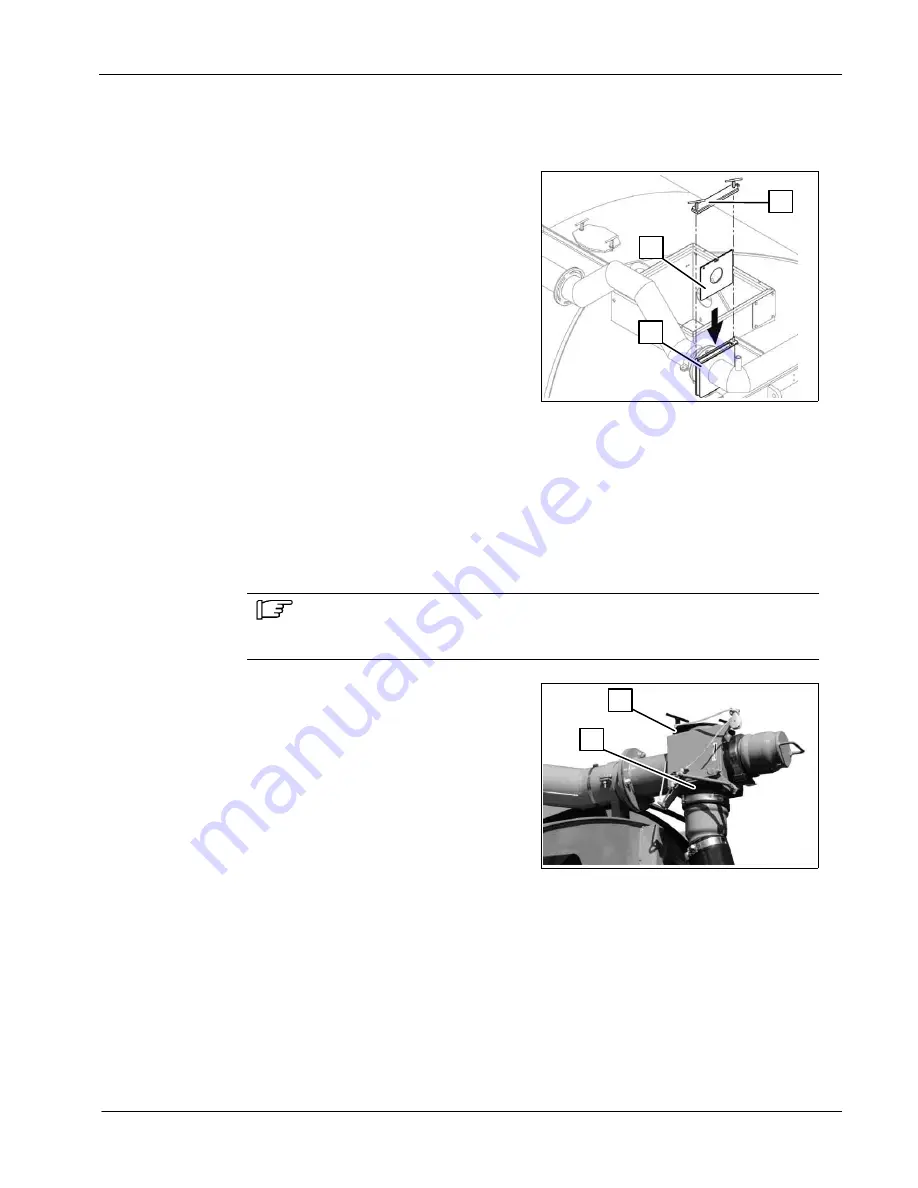
Appendix
Flow rate adjustment
2018-9015-005
09-2016
Step 3: Restriction plate (if applicable)
A spreader discharge pipe can be equipped with a housing designed to insert
a restriction plate to limit flow rate.
● Slide a restriction plate (1) in the
housing (2);
● Close the opening with the cover (3).
1
2
3
Step 4: Directional valve restrictor (if applicable)
A spreader can be equipped with more than one spreading tool at a time.
A directional valve is installed on the discharge pipe allowing the user to select
a spreading tool.
Flow rate can be reduced only inside the lower spreading tool by placing a
restrictor in the lower opening of the directional valve.
Note!
Always restrain flow rate using the flow regulator before adding a
restrictor inside the manual directional valve.
● Remove the cleaning opening (1);
● Place a restrictor in the lower
opening (2) of the directional valve to
reduce the flow rate of the tool
connected.
1
2