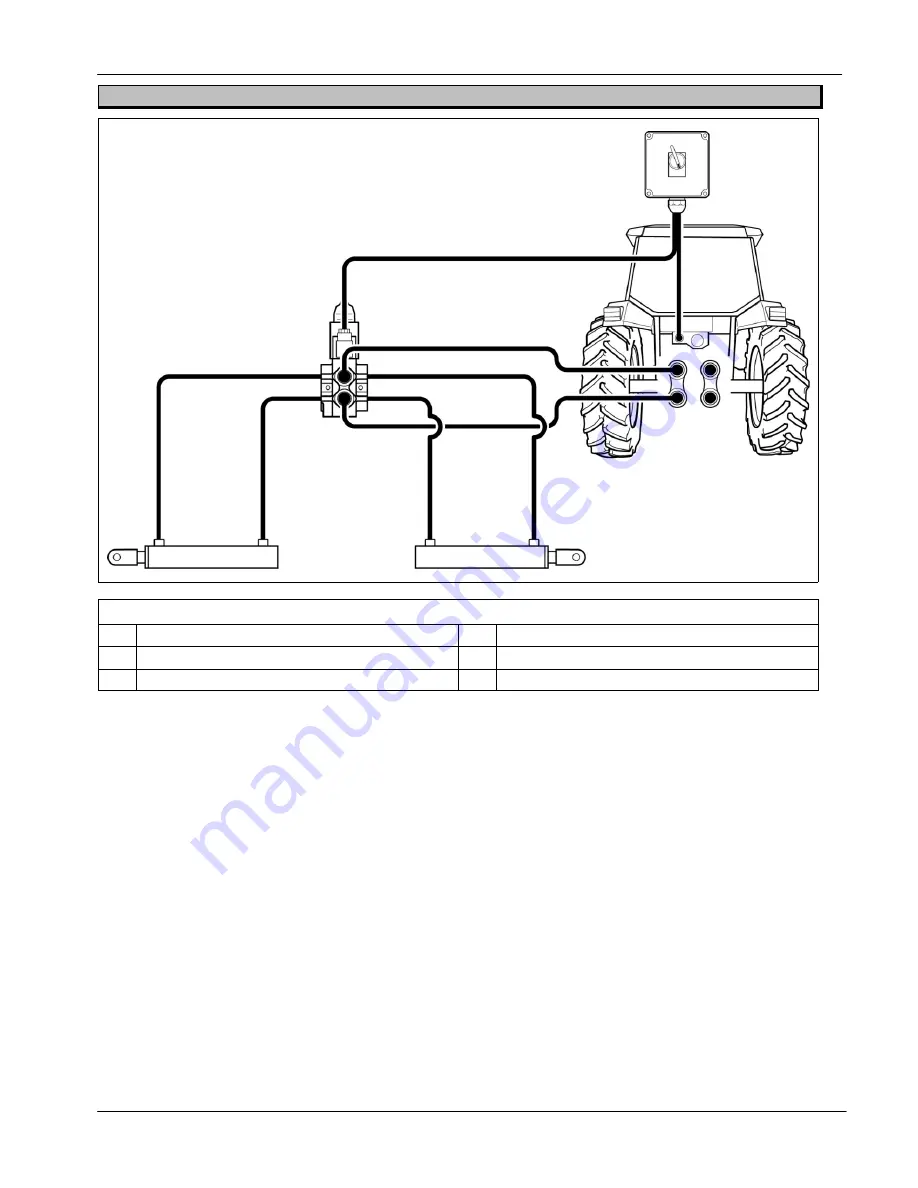
Appendix
Hydraulic diagram - Solenoid valves control option
2018-9015-001
09-2016
11.10
Hydraulic diagram - Solenoid valves control option
2
3
1
6
5
4
Legend:
1
Solenoid valve
4
Hydraulic component #2
2
Selector switch
5
Tractor hydraulic outlets
3
Hydraulic component #1
6
Tractor electric connection (12VDC)