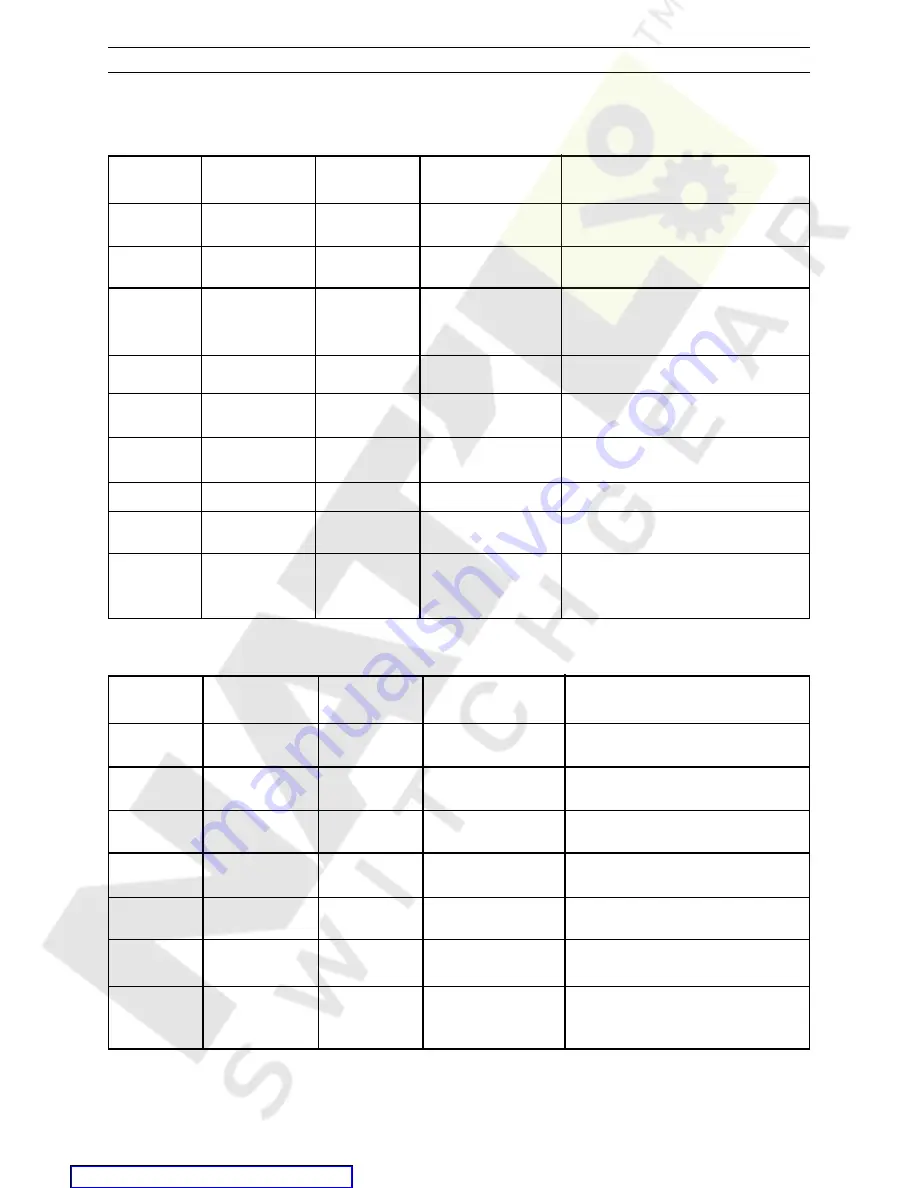
43
TABLE #1 MEASUREMENTS
CLOSING
OPENING
ITEM
BREAKER
SPRING
SPRING
MEASUREMENT
Contact
Open
Charged
Discharged
Measure the stem or between
Wipe
Closed
Charged
Charged
spring block and nut
Contact
Open
Charged
Discharged
Measure the travel of the
Gap
Closed
Charged
Charged
operating rod insulator
Contact
Trip
Closed
Discharged
Charged
Measure between plunger
Coil
button and coil housing
Close
Open
Charged
Discharged
Measure under the collar
Coil
to the end of plunger
Control
Open
Discharged
Discharged
Depends on switch type
Switches
See Chapter 8
Timing
See Chapter 10-10
Contact
See Figure 26
Speeds
Motor
Cutoff
See Figure 47
Switch
PowerVac
®
5kV Vertical Lift
Chapter 11. Mechanical Adjustments
TABLE #2 ADJUSTMENTS
CLOSING
OPENING
ITEM
BREAKER
SPRING
SPRING
MEASUREMENT
Contact
Closed
Charged
Charged
Adjust operating rod to obtain
Wipe
required dimensions
Contact
Open
Charged
Discharged
Use buffer shims to advance
Gap
or retard gap adjustment
Contact
Erosion
Trip
Closed
Discharged
Charged
Turn adjusting nut to obtain
Coil
required dimension
Close
Open
Charged
Discharged
Loosen set screw and
Coil
move collar up or down
Control
Open
Discharged
Discharged
Adjust link
Switches
Motor
Cutoff
See Figure 47
Switch
Measure distance from bottom of
insulated operating rod to bottom
of stainless steel interrupter
support
Erosion
Replace interrupter when
wear exceeds 0.125”