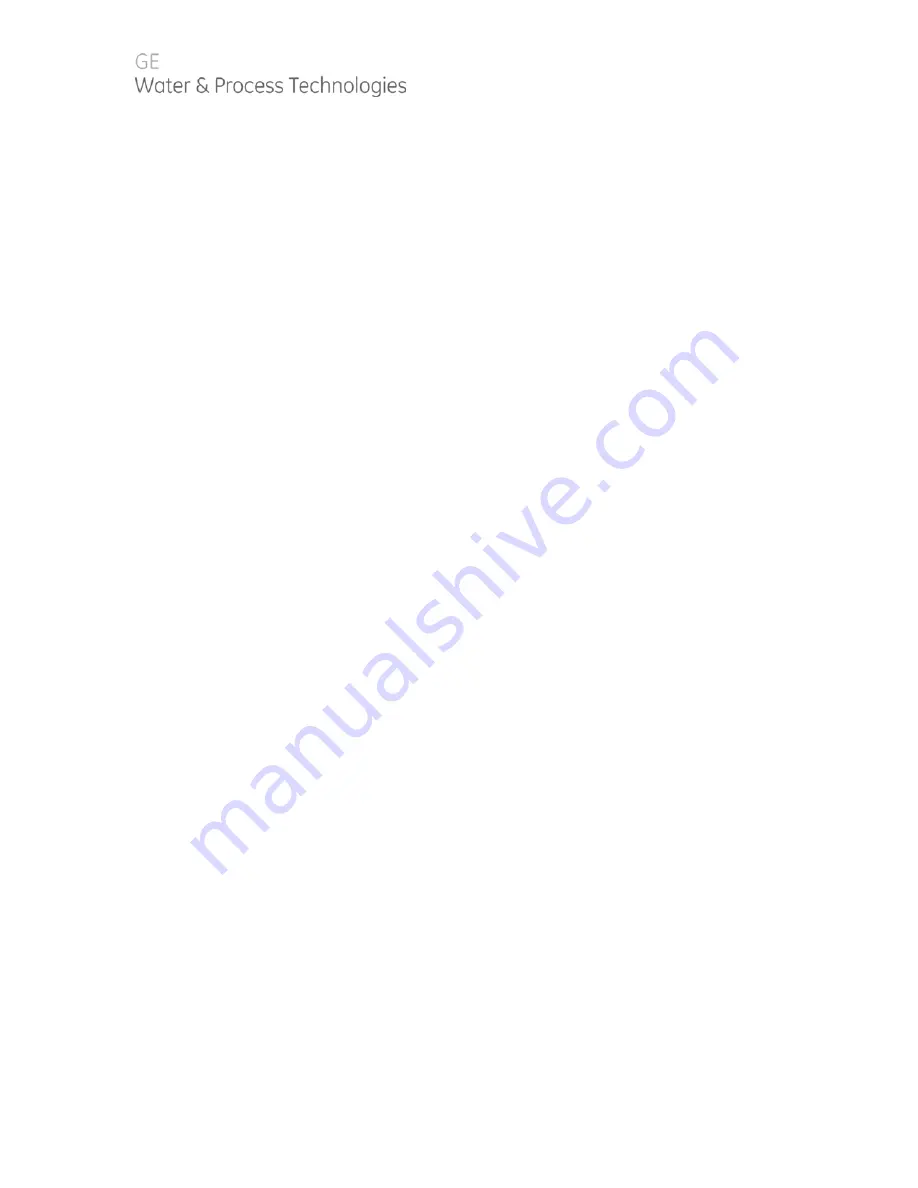
E4H Series
Operation & Maintenance Manual
19
See the following sections for specific maintenance procedures.
4.1. Daily
Log
Sheets
A daily log sheet, which includes general operating conditions (pressures, flows and
concentrations) and routine or special maintenance (pre-filter changes, flushing,
cleaning, etc.) must be kept. Copies of the log can be made from the template. A copy
of this log sheet will be required by GE Water & Process Technologies if a warranty
question arises.
4.2. Pre-Filter
A 1-micron pre-filter is factory-installed to protect the membranes and valves from
particles, which may be in the feed water. The pre-filter uses two 20-inch (50.8-cm)
diameter, 1-micron nominal rated cartridges. To order replacements, see the
standard parts list.
The filter cartridges must be replaced, at a minimum, once per week or after every
100 hours of operation, whichever comes first. A pressure drop of 8 psig (0.6 bar)
across the filter or more during operation indicates one or more cartridges need
changing. Use only GE Water & Process Technologies approved filters rated for 5
microns or less. Do not attempt to clean used filters - install new replacements.
IMPORTANT NOTE: Failure to change the filter according to these requirements will
void the warranty.
4.3. Flushing
The machine should be flushed at least daily to remove sediment from membrane
surfaces. To flush the unit:
1. Open the concentrate valve until the pressure gauge indicates the minimum
pressure designated on the nameplate. This increases the flushing action on
the membrane.
NOTE: If pressure will not decrease to designated pressure, or if the concentrate
rate does not increase when the valve is opened, the valve may be plugged.
2. Operate the machine at the designated minimum pressure for 10 to 20
minutes.
CAUTION: Do not operate the machine below the designated pressure without
approval from GE Water & Process Technologies. Operation below the stated
pressure may be detrimental to the pump.
3. Close the concentrate valve and ensure that the proper concentrate flow rate
is going to the drain (see the nameplate on the panel).
NOTE: The Autoflush (AUF) system, available in DLX packages, automatically
flushes the machine and eliminates the need for frequent manual flushing.
Summary of Contents for Osmonics E4H Series
Page 36: ......
Page 39: ...E4H Series Operation Maintenance Manual 39 1 2450 Front Panel with Display ...
Page 45: ...E4H Series Operation Maintenance Manual 45 A 6 Technician Level Menus ...
Page 46: ...E4H Series Operation Maintenance Manual 46 A 1 8 Operation ...
Page 47: ...E4H Series Operation Maintenance Manual 47 ...
Page 48: ...E4H Series Operation Maintenance Manual 48 ...
Page 49: ...E4H Series Operation Maintenance Manual 49 A 1 9 Relays ...
Page 50: ...E4H Series Operation Maintenance Manual 50 A 1 10 Alarms ...
Page 51: ...E4H Series Operation Maintenance Manual 51 A 1 11 Flow Meters ...
Page 52: ...E4H Series Operation Maintenance Manual 52 A 1 12 4 20 mA Output ...
Page 53: ...E4H Series Operation Maintenance Manual 53 A 1 13 System Setup ...
Page 54: ...E4H Series Operation Maintenance Manual 54 ...
Page 55: ...E4H Series Operation Maintenance Manual 55 ...
Page 56: ...E4H Series Operation Maintenance Manual 56 ...
Page 57: ...E4H Series Operation Maintenance Manual 57 A 1 14 Clock ...
Page 58: ...E4H Series Operation Maintenance Manual 58 A 7 Security Level Menus ...
Page 59: ...E4H Series Operation Maintenance Manual 59 A 8 Operator View Level Menus ...