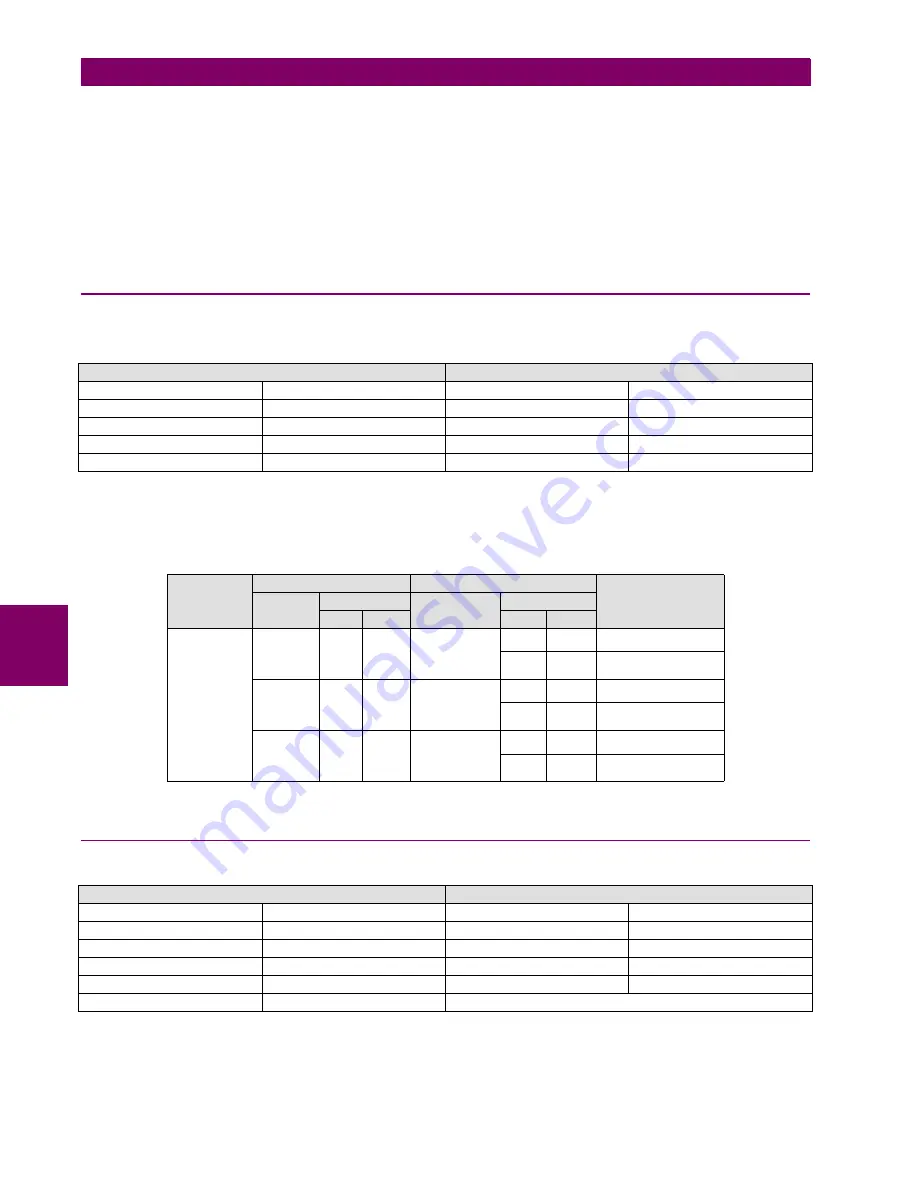
6-14
F650 Digital Bay Controller
GEK-113000T
6.12 DIRECTIONAL ELEMENTS (67P, 67N, 67G, 67SG)
6 COMMISSIONING
6
6.12DIRECTIONAL ELEMENTS (67P, 67N, 67G, 67SG)
In order to test directional units in the relay, instantaneous trips will be commanded.
Two points will be tested, per phase, test element.
In order to test the directional units, configure (in the "
Setpoint > Relay Configuration > Protection Elements
" screen of
the EnerVista 650 Setup program), some overcurrent element to be supervised by a directional unit. This way, if the
directional element is enabled and detects the fault in the block direction, then the overcurrent unit will not operate. If the
directional element is not enabled or if it is enabled and it detects a fault in a trip direction, then the overcurrent unit will
operate if the set current level is exceeded.
6.12.1 67P ELEMENT
Activate only protection elements 50PH and 67P and set the relay as follows:
Configure one of the outputs to be activated only by unit 50PH.
Apply the following tests:
6.12.2 67N ELEMENT
Activate only protection elements 50N and 67N and set the relay as follows:
Configure one of the outputs to be activated only by unit 50G
.
67P SETTINGS
50PH SETTINGS
Function
ENABLED
Function
ENABLED
MTA
45 Deg
Input
PHASOR (DFT)
Direction
FORWARD
Pickup Level
0.50 A
Block Logic
PERMISSION
Trip Delay
0.30
Pol V Threshold
30 V
Reset Delay
0.00
ELEMENTS
PHASE UNDER TEST
POLARIZATION PHASE
ELEMENT TRIP
CHANNEL MAGNITUDE
CHANNEL
MAGNITUDE
MOD
ARG
MOD
ARG
50PH/67P
IA
2 A
0º
VIII
60 V
0º
NO
60 V
180º
YES
IB
2 A
0º
VI
60 V
0º
NO
60 V
180º
YES
IC
2 A
0º
VII
60 V
0º
NO
60 V
180º
YES
67N SETTINGS
50N SETTINGS
Function
ENABLED
Function
ENABLED
MTA
-45 Deg
Input
PHASOR (DFT)
Direction
FORWARD
Pickup Level
0.50 A
Polarization
VO
Trip Delay
0.30
Block Logic
PERMISSION
Reset Delay
0.00
Pol V Threshold
10 V
Summary of Contents for Multilin GEK-113000T
Page 5: ...4 F650 Digital Bay Controller GEK 113000T TABLE OF CONTENTS ...
Page 25: ...1 20 F650 Digital Bay Controller GEK 113000T 1 4 650 HARDWARE 1 GETTING STARTED 1 ...
Page 169: ...6 26 F650 Digital Bay Controller GEK 113000T 6 17 THERMAL IMAGE ELEMENT 49 6 COMMISSIONING 6 ...
Page 215: ...A 36 F650 Digital Bay Controller GEK 113000T A 1 LOGIC OPERANDS APPENDIXA A ...
Page 259: ...D 2 F650 Digital Bay Controller GEK 113000T D 1 GE MULTILIN WARRANTY APPENDIXD D ...