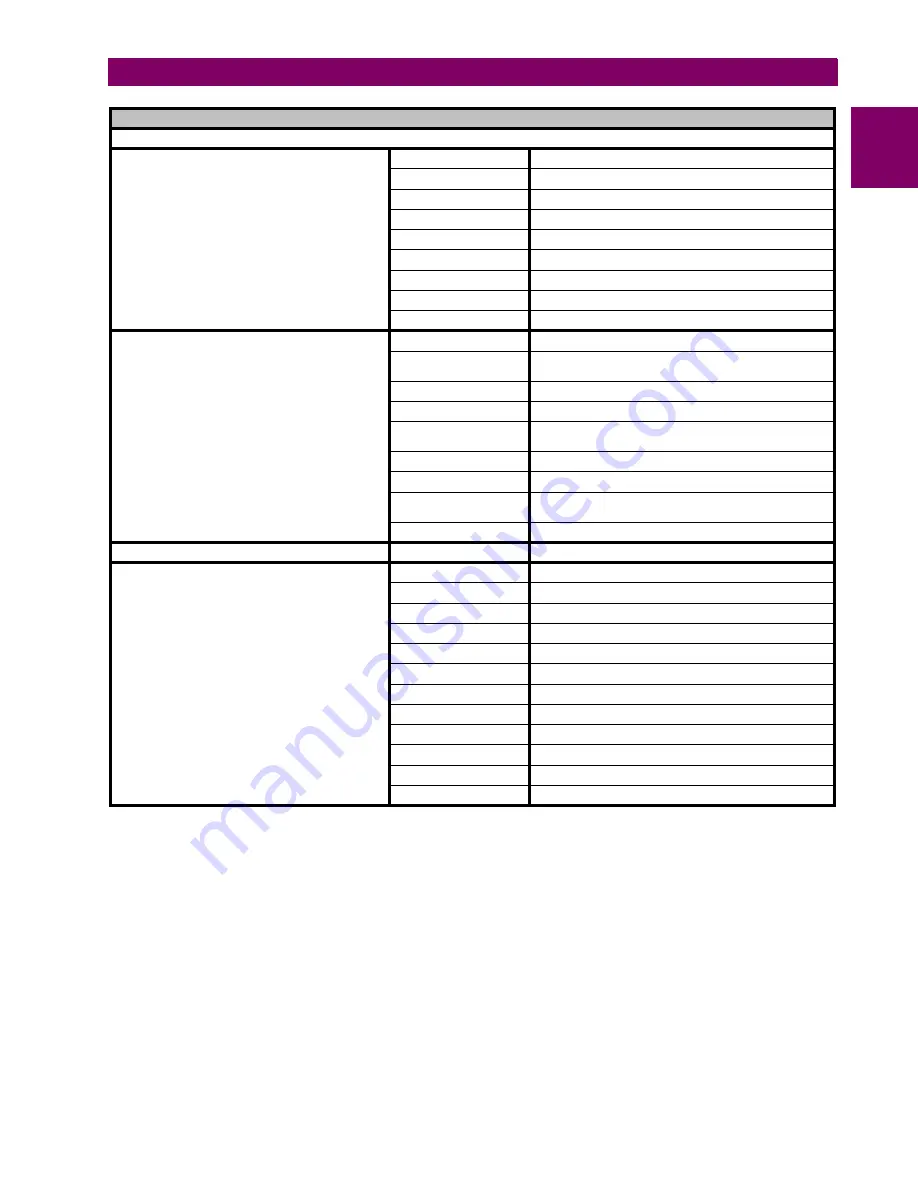
GEK-113000AE
F650 Digital Bay Controller
A-23
APPENDIX A
A.1 LOGIC OPERANDS
A
OPERANDS - F650 - MODEL FX - GX
INTERNAL SYSTEM STATUS (CONT.)
Ground Directional
GROUND DIR1 BLK INP Ground directional element block input signal Group 1
GROUND DIR1 BLOCK Ground directional element blocked Group 1
GROUND DIR1 OP
Ground directional element operation Group 1
GROUND DIR2 BLK INP Ground directional element block input signal Group 2
GROUND DIR2 BLOCK Ground directional element blocked Group 2
GROUND DIR2 OP
Ground directional element operation Group 2
GROUND DIR3 BLK INP Ground directional element block input signal Group 3
GROUND DIR3 BLOCK Ground directional element blocked Group 3
GROUND DIR3 OP
Ground directional element operation Group 3
Sensitive Ground Directional
SENS GND DIR1 BLK IP Sensitive ground directional element block input Group 1
SENS GND DIR1
BLOCK
Sensitive Ground directional element block Group 1
SENS GND DIR1 OP
Sensitive Ground directional element operation Group 1
SENS GND DIR2 BLK IP Sensitive ground directional element block input Group 2
SENS GND DIR2
BLOCK
Sensitive Ground directional element block Group 2
SENS GND DIR2 OP
Sensitive Ground directional element operation Group 2
SENS GND DIR3 BLK IP Sensitive ground directional element block input Group 3
SENS GND DIR3
BLOCK
Sensitive Ground directional element block Group 3
SENS GND DIR3 OP
Sensitive Ground directional element operation Group 3
Fuse failure
VT FUSE FAILURE
Fuse failure operation
Phase UV
PHASE UV1 BLOCK
Phase undervoltage element block Group 1
PHASE UV1 A PKP
Undervoltage element pickup AG Group 1
PHASE UV1 A OP
Undervoltage element operation AG Group 1
PHASE UV1 B PKP
Undervoltage element pickup BG Group 1
PHASE UV1 B OP
Undervoltage element operation BG Group 1
PHASE UV1 C PKP
Undervoltage element pickup CG Group 1
PHASE UV1 C OP
Undervoltage element operation CG Group 1
PHASE UV1 AB PKP
Undervoltage element pickup AB Group 1
PHASE UV1 AB OP
Undervoltage element operation AB Group 1
PHASE UV1 BC PKP
Undervoltage element pickup BC Group 1
PHASE UV1 BC OP
Undervoltage element operation BC Group 1
PHASE UV1 CA PKP
Undervoltage element pickup CA Group 1
Summary of Contents for Multilin F650
Page 66: ...2 38 F650 Digital Bay Controller GEK 113000AE 2 6 EXTERNAL CONNECTIONS 2 PRODUCT DESCRIPTION 2...
Page 210: ...6 28 F650 Digital Bay Controller GEK 113000AE 6 18 THERMAL IMAGE ELEMENT 49 6 COMMISSIONING 6...
Page 256: ...A 36 F650 Digital Bay Controller GEK 113000AE A 1 LOGIC OPERANDS APPENDIX A A...
Page 270: ...B 14 F650 Digital Bay Controller GEK 113000AE B 3 LINK LOSS ALERT LLA APPENDIX B B...
Page 272: ...GEK 113000AE F650 Digital Bay Controller C 2 APPENDIX C C 1 FACTORY DEFAULT LOGIC C...
Page 273: ...GEK 113000AE F650 Digital Bay Controller C 3 APPENDIX C C 1 FACTORY DEFAULT LOGIC C...
Page 275: ...GEK 113000AE F650 Digital Bay Controller C 5 APPENDIX C C 1 FACTORY DEFAULT LOGIC C...
Page 276: ...GEK 113000AE F650 Digital Bay Controller C 6 APPENDIX C C 1 FACTORY DEFAULT LOGIC C...
Page 279: ...GEK 113000AE F650 Digital Bay Controller C 9 APPENDIX C C 1 FACTORY DEFAULT LOGIC C...
Page 280: ...GEK 113000AE F650 Digital Bay Controller C 10 APPENDIX C C 1 FACTORY DEFAULT LOGIC C...
Page 281: ...GEK 113000AE F650 Digital Bay Controller C 11 APPENDIX C C 1 FACTORY DEFAULT LOGIC C...