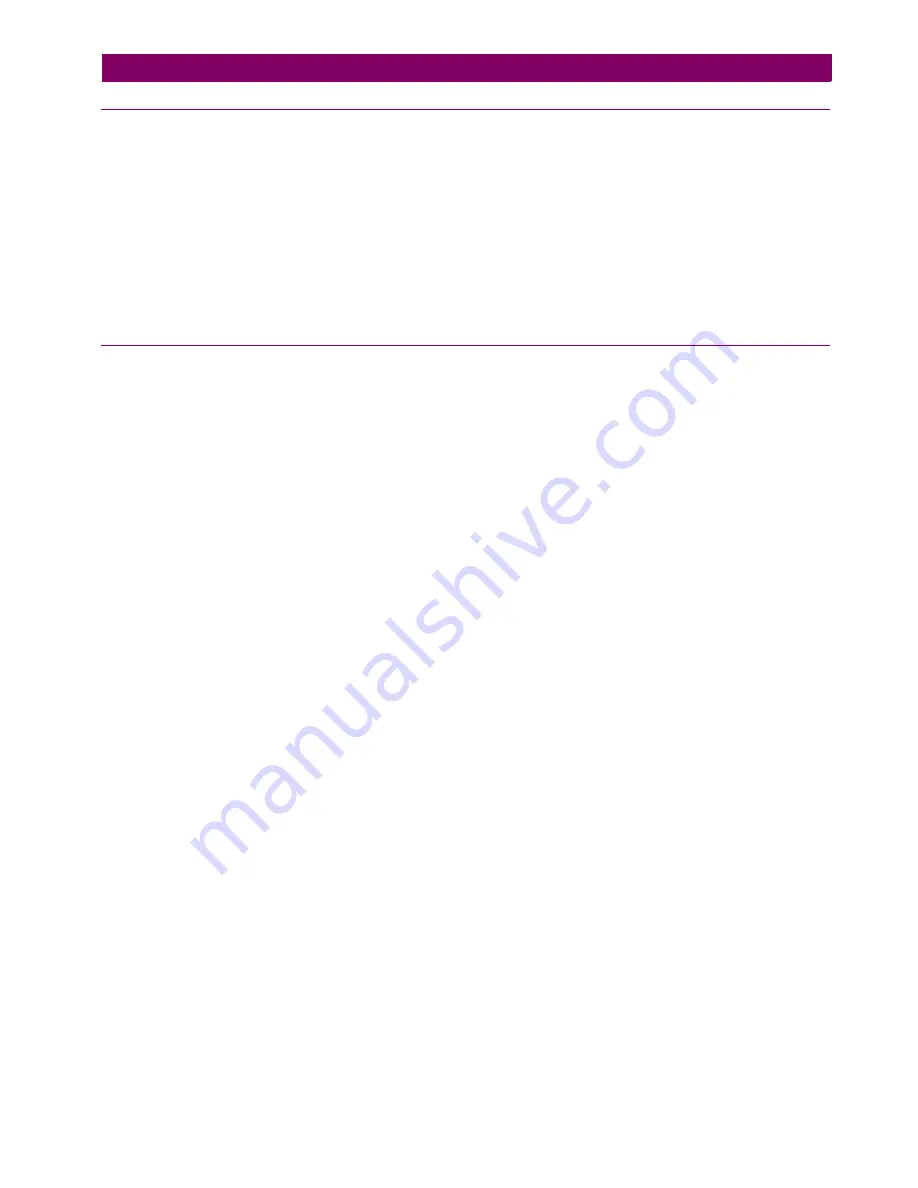
GEK-106237P
MIFII Digital Feeder Relay
1
TABLE OF CONTENTS
1.
GETTING STARTED
1.1 INSPECTION CHECKLIST
1.2 ENERVISTA MII SETUP SOFTWARE
1.2.1
SYSTEM REQUIREMENTS .............................................................................. 1-4
1.2.2
SAFETY INSTRUCTIONS ................................................................................. 1-4
1.2.3
INSTALLATION.................................................................................................. 1-5
1.3 MII RELAY FAMILY HARDWARE
1.3.1
MOUNTING & WIRING.................................................................................... 1-11
1.3.2
COMMUNICATIONS........................................................................................ 1-11
1.3.3
FACEPLATE KEYPAD & DISPLAY ................................................................. 1-11
1.4 USING THE KEYPAD AND DISPLAY
1.4.1
HIERARCHICAL MENUS ................................................................................ 1-12
2.
PRODUCT DESCRIPTION
2.1 SUMMARY
2.1.1
GENERAL OVERVIEW...................................................................................... 2-1
2.2 INTRODUCTION
2.3 ACCESS SECURITY FEATURES
2.4 OVERCURRENT ELEMENTS
2.4.1
PHASE TIME OVERCURRENT ELEMENT (51P)DIFFERENTIAL UNITS (87-1)
(87-2)
2-4
2.4.2
PHASE(50P1, 50P2) ......................................................................................... 2-6
2.4.3
GROUND TIME OVERCURRENT ELEMENT (51G)......................................... 2-6
2.4.4
GROUND INSTANTANEOUS OVERCURRENT ELEMENTS (50G1, 50G2).... 2-6
2.5 THERMAL IMAGE ELEMENT (49)
2.6 RECLOSER ELEMENT
2.6.1
INTRODUCTION................................................................................................ 2-8
2.6.2
RECLOSER STATUSES ................................................................................... 2-8
2.6.3
RECLOSER SETTINGS ................................................................................. 2-12
2.7 COLD LOAD PICKUP (AVAILABLE ONLY IN OPTION 2 MODELS)
2.8 BREAKER FAILURE TO OPEN (AVAILABLE ONLY IN OPTION 2
MODELS)
2.9 I2 COUNTER (AVAILABLE ONLY IN OPTION 2 MODELS)
2.10 EVENTS (AVAILABLE IN OPTION 1 AND OPTION 2 MODELS)
2.11 OSCILLOGRAPHY (AVAILABLE IN OPTION 1 AND OPTION 2 MODELS)
2.12 MULTIPLE SETTING GROUPS
2.13 MEASUREMENT AND SELF-TEST
2.13.1 MEASUREMENT ............................................................................................. 2-21
2.13.2 SELF-TEST...................................................................................................... 2-21
2.14 USER INTERFACE
2.14.1 LED TARGETS ................................................................................................ 2-22
2.14.2 KEYPAD AND DISPLAY.................................................................................. 2-23
2.14.3 COMMUNICATION PORTS............................................................................. 2-23
2.14.4 SOFTWARE..................................................................................................... 2-23
2.15 ORDERING CODES
2.16 TECHNICAL SPECIFICATIONS
2.16.1 PROTECTION ELEMENTS ........................................................................... 2-25
2.16.2 METERING FUNCTIONS ................................................................................ 2-26
2.16.3 INPUTS ............................................................................................................ 2-26
2.16.4 POWER SUPPLY ............................................................................................ 2-27
2.16.5 OUTPUTS ........................................................................................................ 2-27
2.16.6 COMMUNICATIONS........................................................................................ 2-28
2.16.7 ENVIRONMENTAL .......................................................................................... 2-28
2.16.8 TYPE TESTS AND CERTIFICATIONS............................................................ 2-28
2.16.9 PRODUCTION TESTS .................................................................................... 2-30
Summary of Contents for MIFII GEK-106237P
Page 91: ...4 28 MIFII Digital Feeder Relay GEK 106237P 4 7 VIEW 4 COMMUNICATIONS 4 ...
Page 124: ...GEK 106237P MIFII Digital Feeder Relay 8 7 8 KEYPAD AND DISPLAY 8 5 MENU TREE 8 8 5MENU TREE ...
Page 125: ...8 8 MIFII Digital Feeder Relay GEK 106237P 8 5 MENU TREE 8 KEYPAD AND DISPLAY 8 ...
Page 126: ...GEK 106237P MIFII Digital Feeder Relay 8 9 8 KEYPAD AND DISPLAY 8 5 MENU TREE 8 ...
Page 127: ...8 10 MIFII Digital Feeder Relay GEK 106237P 8 5 MENU TREE 8 KEYPAD AND DISPLAY 8 ...
Page 128: ...GEK 106237P MIFII Digital Feeder Relay 8 11 8 KEYPAD AND DISPLAY 8 5 MENU TREE 8 ...
Page 129: ...8 12 MIFII Digital Feeder Relay GEK 106237P 8 5 MENU TREE 8 KEYPAD AND DISPLAY 8 ...
Page 130: ...GEK 106237P MIFII Digital Feeder Relay 8 13 8 KEYPAD AND DISPLAY 8 5 MENU TREE 8 ...
Page 131: ...8 14 MIFII Digital Feeder Relay GEK 106237P 8 5 MENU TREE 8 KEYPAD AND DISPLAY 8 ...
Page 185: ...A 10 MIFII Digital Feeder Relay GEK 106237P A 6 MIFII THERMAL CURVES APPENDIXA A ...
Page 203: ...B 18 MIFII Digital Feeder Relay GEK 106237P B 3 IAC CURVES APPENDIXB B ...
Page 245: ...F 8 MIFII Digital Feeder Relay GEK 106237P F 5 CONCLUSIONS APPENDIXF F ...