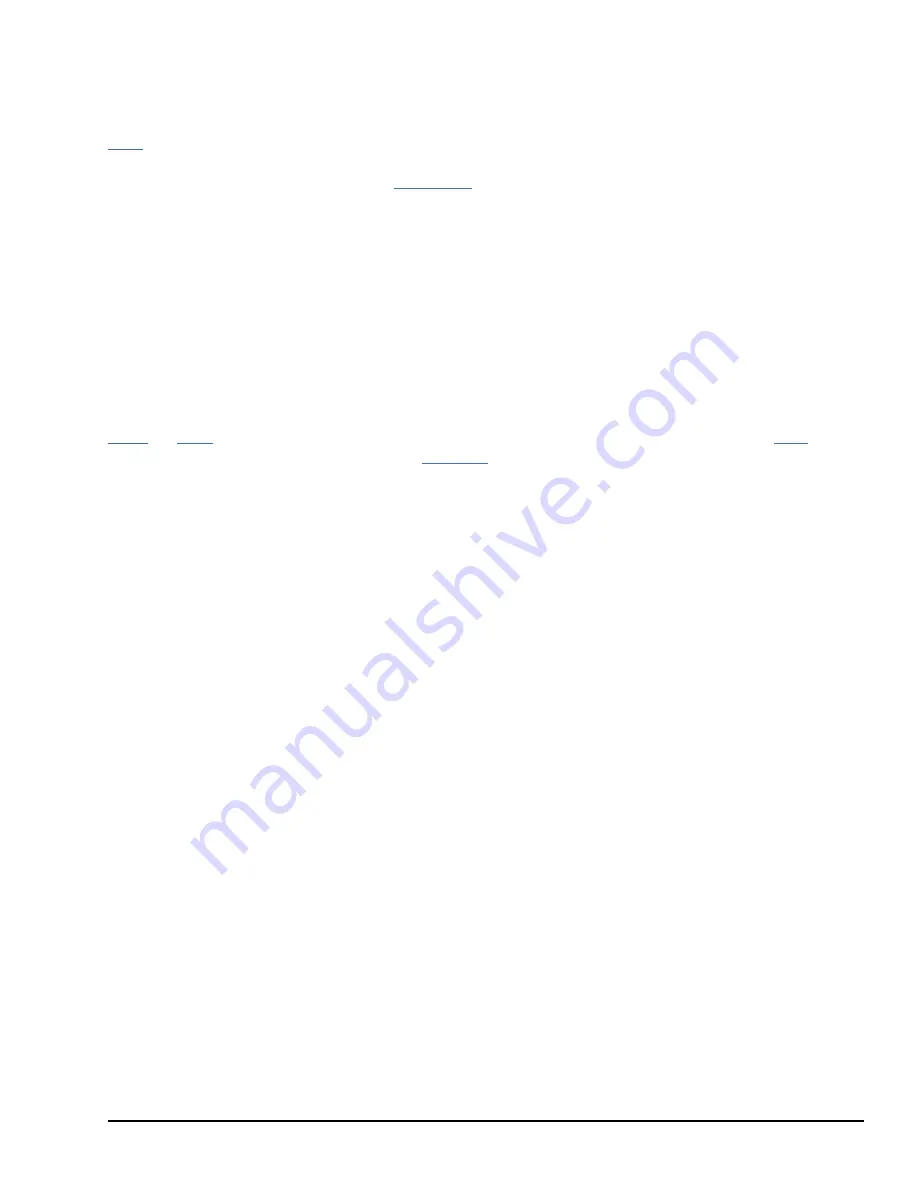
The application designer can use as much Relay Ladder or Function Block Diagram logic as is needed to condition the
Boolean or Analog variable such that alarms are not triggered unless conditions truly warrant creation of an alarm. This
ability to use arbitrary control logic to condition alarm generation in real-time at fast sample rates is a very powerful
capability afforded by creating alarms in the controller itself. Alarm detection happens as part of the Mark VIe controller
(part of the outputs phase of processing and synchronous to the control logic). Because of this, timestamps of alarms
are very accurate, and can easily be compared to other data collected from the controller since that data is time stamped with
exactly the same time as the alarm. Specialized
are also available, effectively capturing many design patterns for
pre-alarm signal conditioning in a reusable library form.
The alarm system collects exactly what the controller logic detects so there are no losses in resolution and there is no
resampling. The Mark VIe controller can run frames as fast as once every 10 milliseconds, and uses POSIX timestamps with
nanosecond resolution and sub millisecond accuracy. Comparison of timestamps from alarms that originate from different
controllers devices is possible since the controllers and HMIs are all time synchronized with NTP.
When an alarm Boolean first transitions to True, the controller creates a new instance of an alarm record structure and places
it in the alarm queue of the controller. Later, the Boolean might transition to False, but unless the operator takes action, the
alarm queue entry remains. If the Boolean again transitions to True, the alarm queue entry is updated. The alarm queue entry
will not be deleted unless the alarm is set for Auto Acknowledge. The operator can acknowledge the alarm, the alarmed
Boolean can change to False, and the operator can reset the alarm. The acknowledge and reset may be accomplished in single
keystroke if the auto-acknowledge feature is enabled.
and
can be created in a fashion that is very similar to that of process alarms. Sequence of Events (
) are
created by setting a similar property on an IO Point.
Alarms can also be created in the controller by transmission
from other subsystems such as from F
OUNDATION
Fieldbus devices. Diagnostic Alarms are created by firmware itself, not by
the application engineer.
7.5.2.1
Intrinsic Variables and Totalizers
Intrinsic variables allow alarm manager commands to be generated when a variable changes state. Totalizers are timers and
counters that store critical data such as number of trips, number of starts, and number of fired hours. The controller provides a
special block,
Totalizer
, which maintains values in a protected section of non-volatile RAM (NVRAM). ControlST V07.04
and lower supports 64 totalizers. ControlST V07.05 and higher supports 128 totalizers. This Totalizer block should be placed
in a protected macro to prevent the logic driving its counters from being modified. Users can set and clear Totalizer counter
values from the ToolboxST application. The standard block library instruction guide (GEI-100682) provides more details on
using the Totalizer block. Refer to
GEH-6700 ToolboxST User Guide for Mark VIe Control
, the section,
Intrinsic Variables
.
7.5.2.2
External Process Alarms
Process alarms may also enter the alarm system through the WorkstationST application rather than through the Mark VIe
controller. The WorkstationST appliation can scan Boolean variables and create alarms in a manner similar to the Mark VIe
controller. Additionally, the WorkstationST application can import alarms from other systems using OPC AE or OPC UA.
Alarm Overview
GEH-6721_Vol_I_BP System Guide 173
Public Information