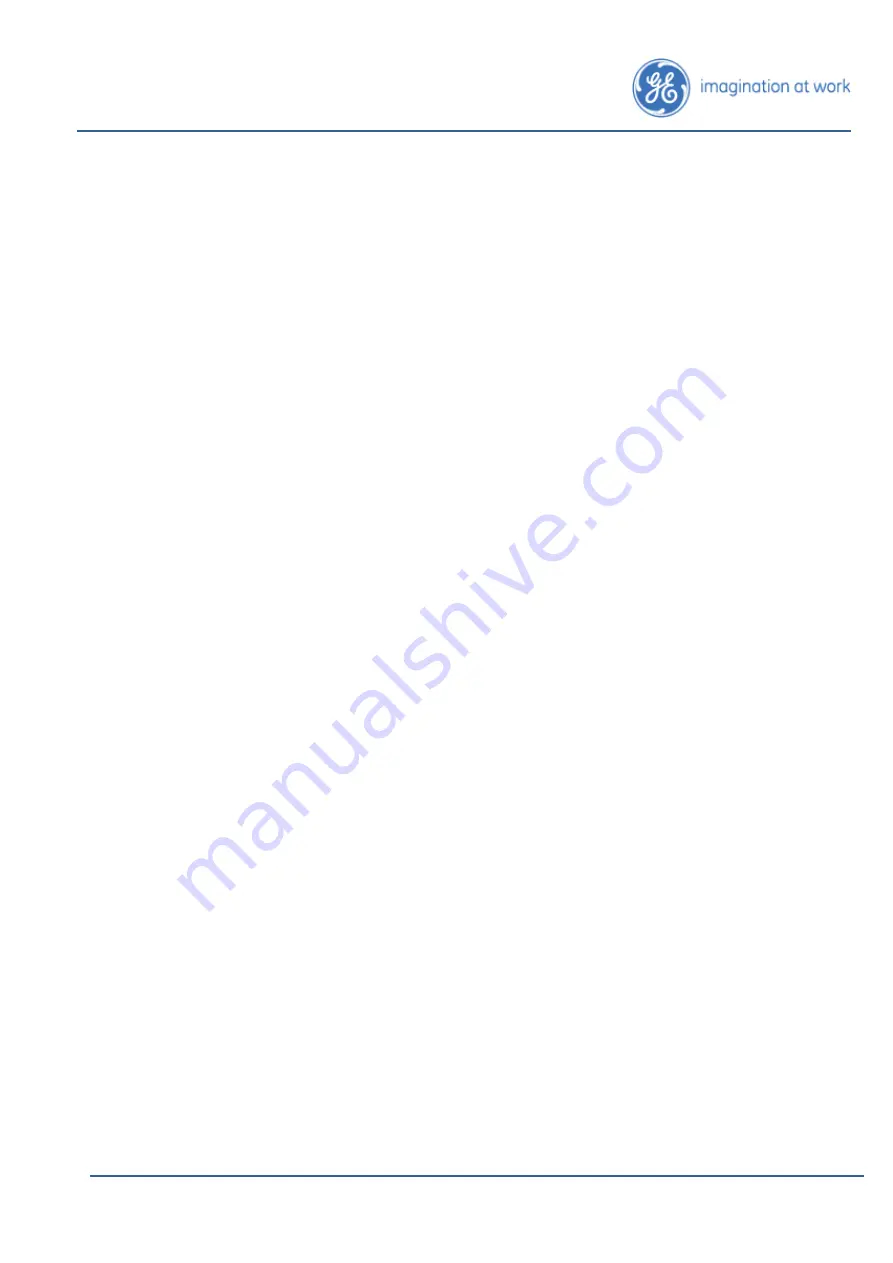
Page 17
Intellix
™
BMT 330 User Manual
BMT330UM
v1.0
20-Jun-16
Changing between Intellix™ BMT 330 and Intellix™ BMT 300
units
When the BMT Setup Software opens, it is designed to try to connect to the last
Intellix™ BMT unit used. If this connection is no longer available or the user wishes to
connect to different unit, then the communication settings for the applicable unit will
need to be entered.
If the BMT Setup Software is unable to establish an automatic connection on
opening, it will default to the Intellix™ BMT 330 interface.
To subsequently connect to an Intellix™ BMT 300 unit, the communications
settings need to be setup and a “
Ping
” (
Communication
page) will return a message
stating that the firmware does not match the 3.3 version of the BMT Setup Software.
This message indicates that a successful firmware read has occurred and that a
restart of the BMT Setup Software should now auto-connect to the Intellix™ BMT 300
unit.
Figure 5 shows the logic steps when changing between Intellix™ BMT330 and
Intellix™ BMT 300 units.