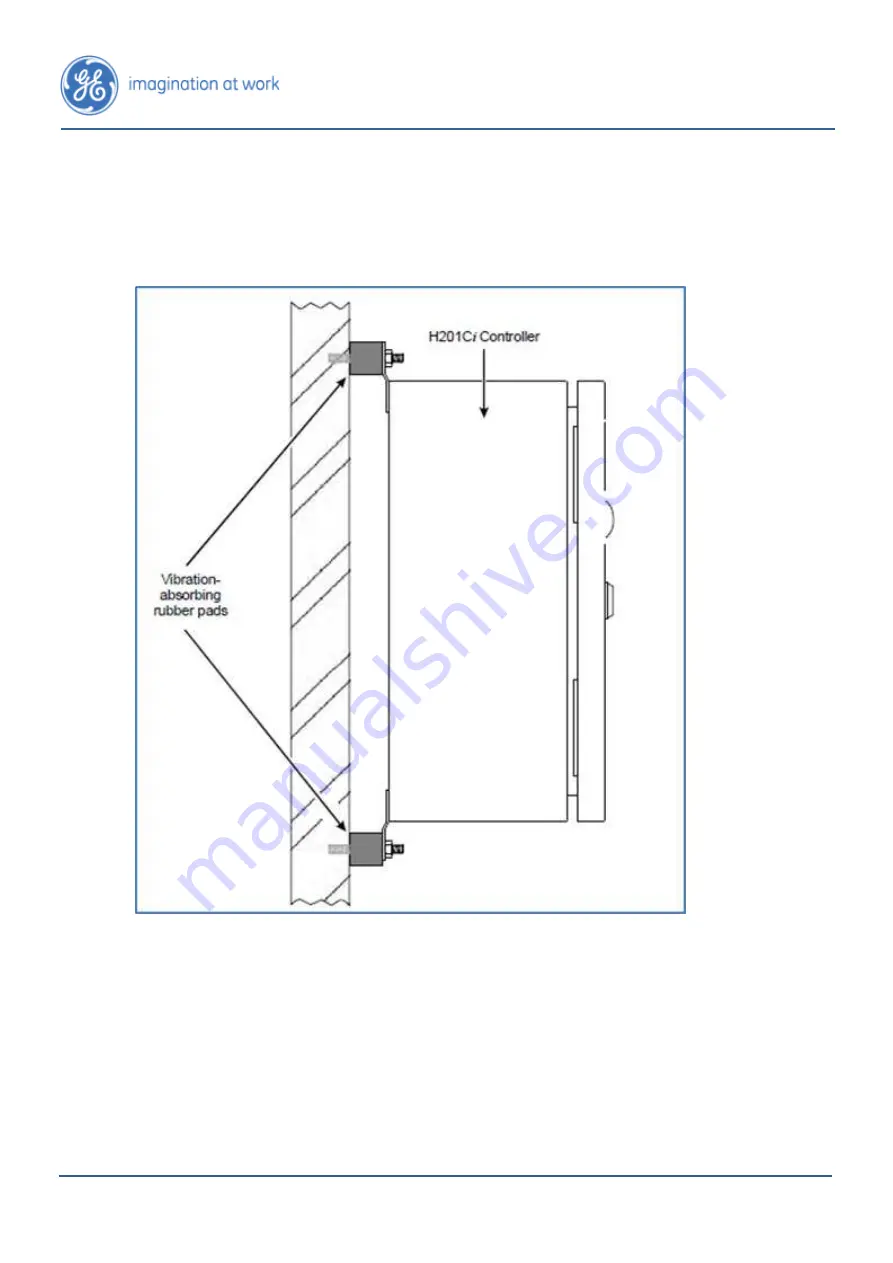
Hydran* 201
i
Installation Guide
Page 14
17996 Rev5, August 2013
2.3
Vibration-Absorbing Rubber Pads
If vibrations are present, rubber pads (which can be purchased from General
Electric) are used on the back of the Hydran 201C
i
Controllers; an example is shown
in Figure 3 below.
Figure 3: Vibration-Absorbing Rubber Pads