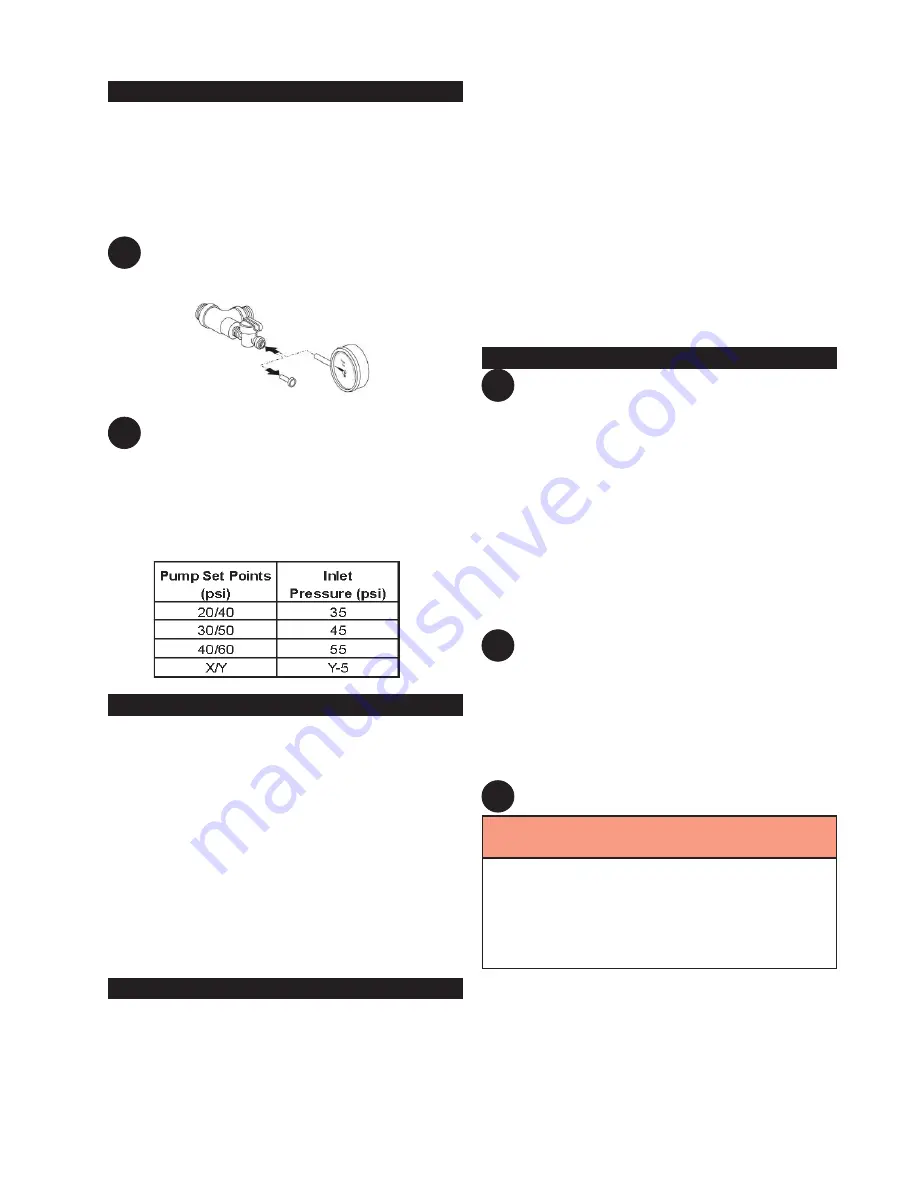
Backpulse Tank Pressure Check
Using the Digital Air Pressure Gauge, check the
Backpulse Tank pressure. If it is not at the correct pressure
(Approximately 35 psi for most installations;
Refer to the
Service Tag for the actual reading), adjust the pressure
using an air pump or compressor. Refer to Step 3 of the
System installation
section under
E. inSTallaTiOn inSTrUCTiOnS
for guidance.
2
G. annUal MainTEnanCE
To extend the life of the System’s membrane, maintenance
procedures are recommended on a minimum of an annual
basis. A Service Kit is required, including an Integrity
Tester and other necessary tools, to perform the Annual
Maintenance. A
Homespring™ Qualified Technician
must perform all maintenance including the annual
Integrity Test as required as part of the 5 year limited
prorated System warranty. If the
Homespring™ Qualified
Technician
determines that the System has a high degree
of debris causing a reduction in the flowrate, the number
of maintenance visits per year may be increased to ensure
that the System stays within operational limits, and to
ensure the limited prorated warranty protection remains in
effect.
annual Maintenance Procedure
Transmembrane Pressure Test
The first step will be to perform a “pre-cleaning” trans-
membrane pressure test. To perform this test, follow
the
steps in the
Transmembrane Pressure Test
section under
f. COMMiSSiOninG
. Thi
s test will be performed prior to
the cleaning and again following the Integrity Test. The
results of these tests are to be recorded on the Service
Tag.
If the Inlet Valve is upstream of the External Prefilter,
change the External Prefilter follo
wing guidelines
in the
Surface Water Option Kit installation
section under
E. inSTallaTiOn inSTrUCTiOnS
to install a new
External Prefilter cartridge before beginning the Membrane
Cleaning.
1
3
membrane cleaning
WARNING!
Disposable protective gloves must be worn during
maintenance of the System to protect your hands.
At the end of the procedure, wash your hands
thoroughly with soap and water. Do not reuse the
gloves. Dispose of the gloves in the garbage.
complete Paperwork
The following documents are shipped with the System:
Owner’s Manual
Congratulations letter
Installation Checklist
Service Tag
Warranty Card
Pipe Labels
• Complete all info on the Service Tag and hang from
System Cap.
• Complete and return the Installation/Registration
Checklist, ensure that all fields are complete, including the
homeowner’s signature.
•
Record the model number on page 2 of the Owner’s
Manual
for future reference.
final flush by Homeowner
Have the homeowner continue to run a cold water tap for
60 minutes. This is required to meet NSF drinking water
standards and to remove residual chlorine. The homeowner
may notice chlorine taste/smell when a tap is first opened
for a day or two following the cleaning procedure.
Transmembrane Pressure (TMP) Test
The TMP test measures the pressure drop across
the membrane. This is the pressure change that the
homeowner will observe as a result of the filtering
process. The TMP is tracked during the life of the System
and is used to determine the condition of the System
membrane. As the membrane fouls, the TMP will increase.
2
With a nearby tap running with a high flow rate,
read the two Pressure Gauges and subtract the Outlet
pressure from the Inlet pressure. The resulting value is the
TMP. Record the value on the Service Tag.
When a pump/pressure tank is in use, use the following
inlet pressure to determine TMP:
1
Insert a Pressure Gauge into each of the Inlet and
Outlet Mini Ball Valves and open the valves.
fiGUrE 46
For installations excluding ground water installations,
clean the membrane following the steps
in the
cleaning
section under
f. COMMiSSiOninG
with the following
exceptions. In Step
3,
after the System Cap is removed,
wipe the System Cap out with a clean, soft cloth, remove
the O-ring carefully, wipe the O-ring with a clean cloth,
check the O-ring for damage or wear, apply a very small
amount of DOW CORNING 111 silicone lubricant on the
23