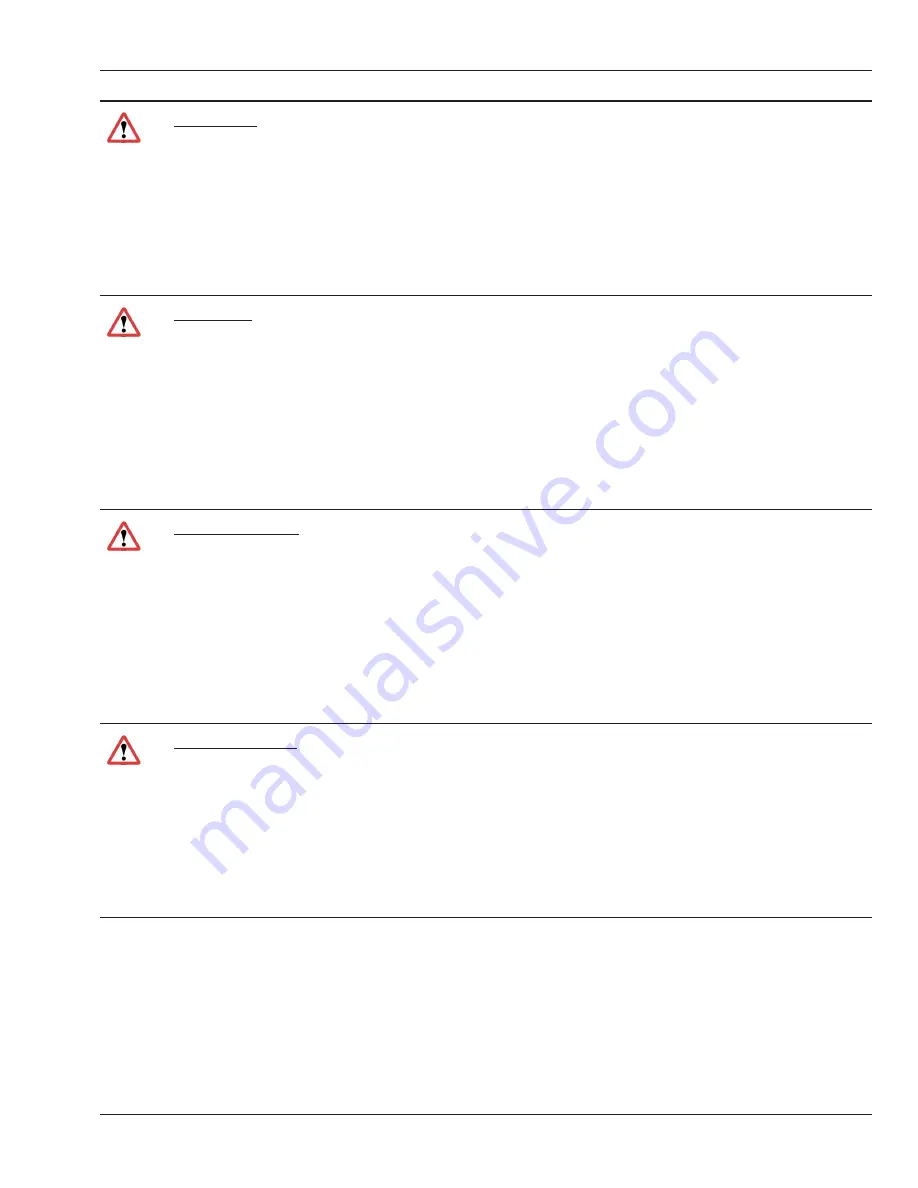
© 2001 by Datex-Ohmeda, Inc.. All rights reserved.
6600-0343-000 104
xxiii
About this Manual
(FR)
ATTENTION
Ce manuel d’installation et de maintenance est disponible uniquement en anglais.
• Si le technicien d’un client a besoin de ce manuel dans une langue autre que l’anglais, il
incombe au client de le faire traduire.
• Ne pas tenter d’intervenir sur les équipements tant que ce manuel d’installation et de
maintenance n’a pas été consulté et compris.
• Le non-respect de cet avertissement peut entraîner chez le technicien, l’opérateur ou le patient
des blessures dues à des dangers électriques, mécaniques ou autres.
(DE)
WARNUNG
Diese Serviceanleitung existiert nur in englischer Sprache.
• Falls ein fremder Kundendienst eine andere Sprache benötigt, ist es Aufgabe des Kunden für
eine entsprechende Übersetzung zu sorgen.
• Versuchen Sie nicht diese Anlage zu warten, ohne diese Serviceanleitung gelesen und
verstanden zu haben.
• Wird diese Warnung nicht beachtet, so kann es zu Verletzungen des Kundendiensttechnikers,
des Bedieners oder des Patienten durch Stromschläge, mechanische oder sonstige Gefahren
kommen.
(EL)
ΠΡΟΕΙΔΟΠΟΙΗΣΗ
Το παρόν εγχειρίδιο σέρβις διατίθεται μόνο στα αγγλικά.
• Εάν ο τεχνικός σέρβις ενός πελάτη απαιτεί το παρόν εγχειρίδιο σε γλώσσα εκτός των
αγγλικών, αποτελεί ευθύνη του πελάτη να παρέχει τις υπηρεσίες μετάφρασης.
• Μην επιχειρήσετε την εκτέλεση εργασιών σέρβις στον εξοπλισμό αν δεν έχετε συμβουλευτεί
και κατανοήσει το παρόν εγχειρίδιο σέρβις.
• Αν δεν προσέξετε την προειδοποίηση αυτή, ενδέχεται να προκληθεί τραυματισμός στον
τεχνικό σέρβις, στο χειριστή ή στον ασθενή από ηλεκτροπληξία, μηχανικούς ή άλλους
κινδύνους.
(HU)
FIGYELMEZTETÉS
Ezen karbantartási kézikönyv kizárólag angol nyelven érhető el.
• Ha a vevő szolgáltatója angoltól eltérő nyelvre tart igényt, akkor a vevő felelőssége a fordítás
elkészíttetése.
• Ne próbálja elkezdeni használni a berendezést, amíg a karbantartási kézikönyvben leírtakat
nem értelmezték.
• Ezen figyelmeztetés figyelmen kívül hagyása a szolgáltató, működtető vagy a beteg áramütés,
mechanikai vagy egyéb veszélyhelyzet miatti sérülését eredményezheti.
Summary of Contents for Giraffe OmniBed
Page 10: ...x 6600 0343 000 104 2001 by Datex Ohmeda Inc All rights reserved Table of Contents ...
Page 28: ...xxviii 6600 0343 000 104 2001 by Datex Ohmeda Inc All rights reserved About this Manual ...
Page 48: ...20 6600 0343 000 104 2001 by Datex Ohmeda Inc All rights reserved Chapter 2 Service Checkout ...