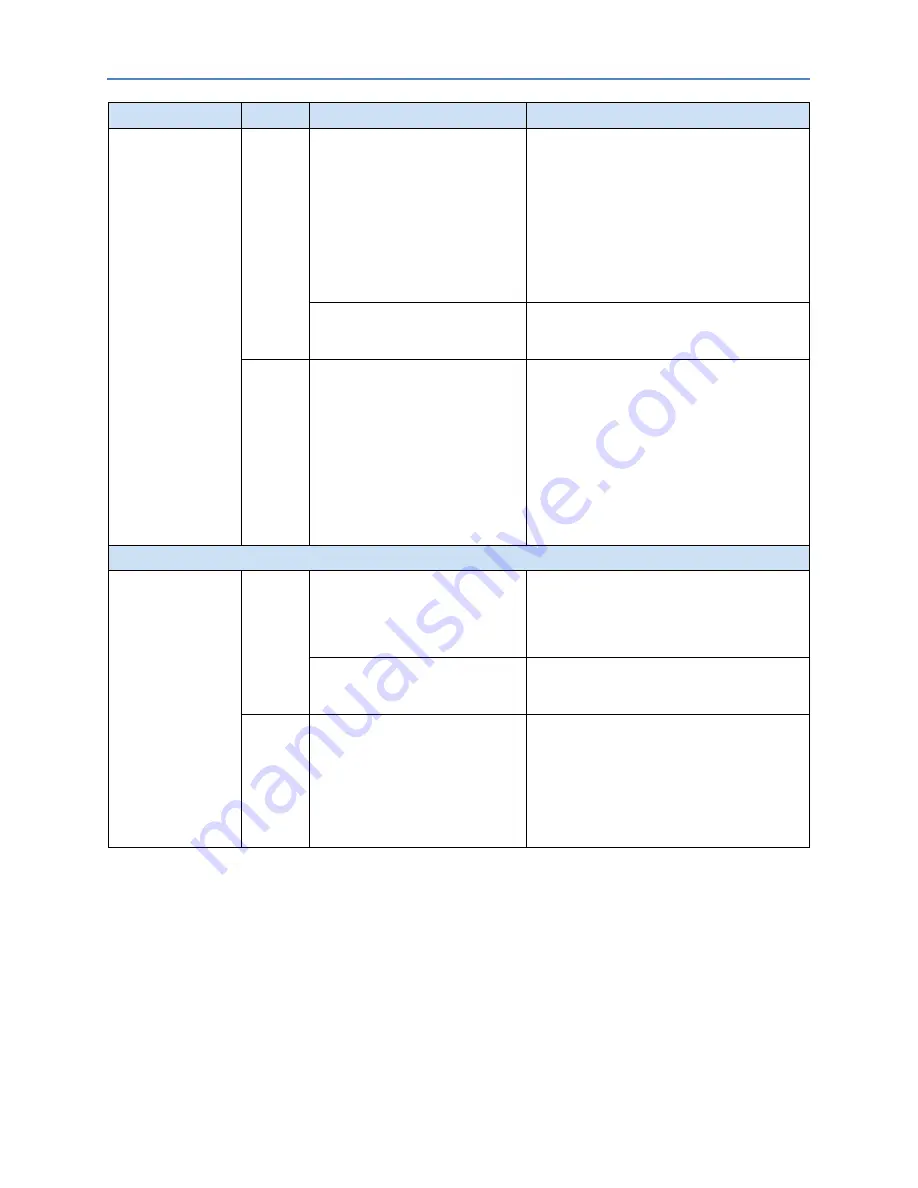
Chapter 12 LED Indicators and Troubleshooting
GFK-2958E
RSTi-EP User Manual
405
Module
LED
Status
Recommended action
EP-3804, EP-3704
Status
LED
Red:
–
Error in supply voltage at input
current path
–
Communication error on the
system bus
–
There is a new diagnostic
message
–
Channel error
–
Firmware error
–
Check that the module has been snapped
into place properly
–
Check the supply voltage
–
Check channel error
–
Check firmware, update firmware as
necessary
Status LED
off
and all other LEDs
red:
Error in the bus network
adapter power supply
–
Check the bus network adapter supply
voltage
Channel
LED
1.1-4.1
Red:
–
Input signal outside permissible
range
–
Line break
–
Cold-junction compensation error
(EP-3804 only)
–
System bus cannot be accessed
(for example, caused by
interruption of the bus network
adapter power supply)
–
Check the input signal, the cabling and, if
necessary, the sensor for external cold-
junction compensation.
–
Check the bus network adapter supply
voltage
Analog output modules
EP-4164, EP-4264
Status
LED
Red:
–
Error in supply voltage
–
Communication error
–
Channel error
–
Check that the module has been snapped
into place properly
–
Check the supply voltage
–
Check the channel error
Status LED
off
and all other LEDs
red:
Error in the bus network
adapter power supply
–
Check the bus network adapter supply
voltage
Channel
LED
1.1-4.1
Red:
–
Overload in voltage mode
–
Broken line in current mode
–
System bus cannot be accessed
(for example, caused by
interruption of the bus network
adapter power supply)
–
Check the connected load, check the cabling,
–
Check the bus network adapter supply
voltage
Summary of Contents for GFK-2958E
Page 1: ...RSTi EP User Manual GFK 2958E November 2017 ...
Page 23: ...Chapter 1 Introduction GFK 2958E RSTi EP User Manual 19 Notes ...
Page 56: ...Chapter 3 Configuration GFK 2958E RSTi EP User Manual 52 Notes ...
Page 183: ...Chapter 5 Detailed Descriptions of I O Modules GFK 2958E RSTi EP User Manual 179 EP 5111 ...
Page 184: ...Chapter 5 Detailed Descriptions of I O Modules GFK 2958E RSTi EP User Manual 180 EP 5111 ...
Page 316: ...Chapter 5 Detailed Descriptions of I O Modules GFK 2958E RSTi EP User Manual 312 Notes ...
Page 330: ...Chapter 6 Installation GFK 2958E RSTi EP User Manual 326 Notes ...
Page 344: ...Chapter 7 Earthing and Shielding GFK 2958E RSTi EP User Manual 340 ...
Page 345: ...Chapter 7 Earthing and Shielding GFK 2958E RSTi EP User Manual 341 Notes ...
Page 385: ...Chapter 8 Web Server GFK 2958E RSTi EP User Manual 381 Notes ...
Page 401: ...Chapter 11 Disassembly and Disposal GFK 2958E RSTi EP User Manual 397 Notes ...
Page 413: ...Chapter 12 LED Indicators and Troubleshooting GFK 2958E RSTi EP User Manual 409 Notes ...
Page 416: ...Chapter 14Accessories and Replacement Parts GFK 2958E RSTi EP User Manual 412 Notes ...