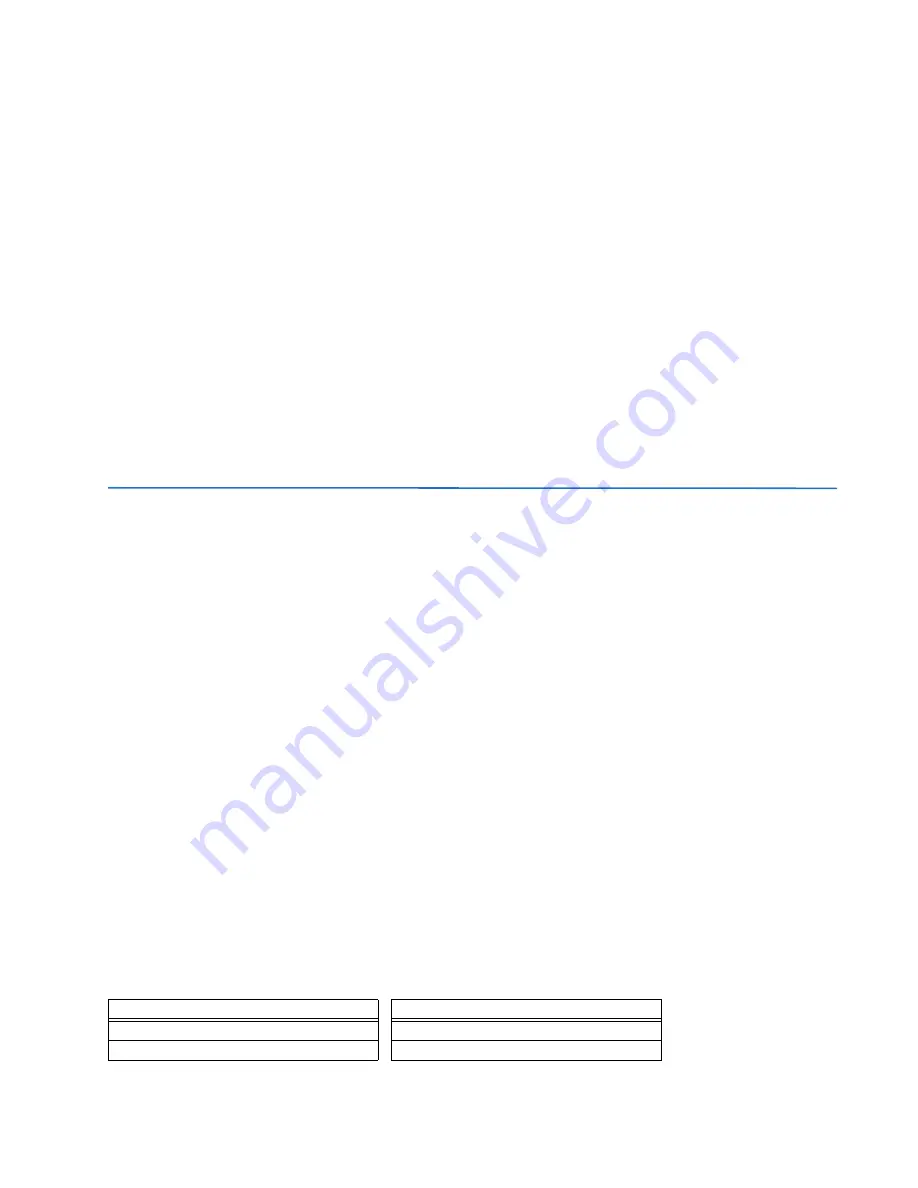
C30 CONTROLLER SYSTEM – INSTRUCTION MANUAL
2-1
C30 Controller System
Chapter 2: Product description
Product description
This chapter outlines the product, order codes, and specifications.
2.1 Product description
The C30 Controller System is part of the Universal Relay (UR) series of products. It is a microprocessor-based device
designed for power substation control and monitoring.
Diagnostic features include a sequence of records capable of storing 1024 time-tagged events. The internal clock used for
time-tagging can be synchronized with an IRIG-B signal, using the Simple Network Time Protocol (SNTP) over the Ethernet
port, or using the Precision Time Protocol (PTP). This precise time stamping allows the sequence of events to be determined
throughout the system. Events can also be programmed (via FlexLogic
™
equations) to trigger oscillography data capture
that can be set to record the measured parameters before and after the event for viewing on a computer. These tools
significantly reduce troubleshooting time and simplify report generation in the event of a system fault.
Several options are available for communication. A faceplate RS232 port can be used to connect to a computer for the
programming of settings and the monitoring of actual values. The rear RS485 port allows independent access by operating
and engineering staff. It can be connected to system computers with baud rates up to 115.2 kbps. All serial ports use the
Modbus RTU protocol. The IEC 60870-5-103 protocol is supported on the RS485 interface. IEC 60870-5-103, DNP, and
Modbus cannot be enabled simultaneously on this interface. Also only one of the DNP, IEC 60870-5-103, and IEC 60870-5-
104 protocols can be enabled at any time on the relay. When the IEC 60870-5-103 protocol is chosen, the RS485 port has a
fixed even parity and the baud rate can be either 9.6 kbps or 19.2 kbps. The 100Base-FX or 100Base-TX Ethernet interface
provides fast, reliable communications in noisy environments. The Ethernet port supports IEC 61850, Modbus/TCP, TFTP,
and PTP (according to IEEE Std. 1588-2008 or IEC 61588), and it allows access to the relay via any standard web browser
(C30 web pages). The IEC 60870-5-104 protocol is supported on the Ethernet port. The Ethernet port also supports the
Parallel Redundancy Protocol (PRP) of IEC 62439-3 (clause 4, 2012) when purchased as an option.
Secure Routable GOOSE (R-GOOSE) is supported with software options.
Settings and actual values can be accessed from the front panel or EnerVista software.
The C30 uses flash memory technology that allows field upgrading as new features are added. Firmware and software are
upgradable.
Table 2-1: Device functions
Function
Function
Breaker Control
IEC 61850 Communications
Contact Inputs (up to 96)
IEC 62351-9 Data and Communications Security