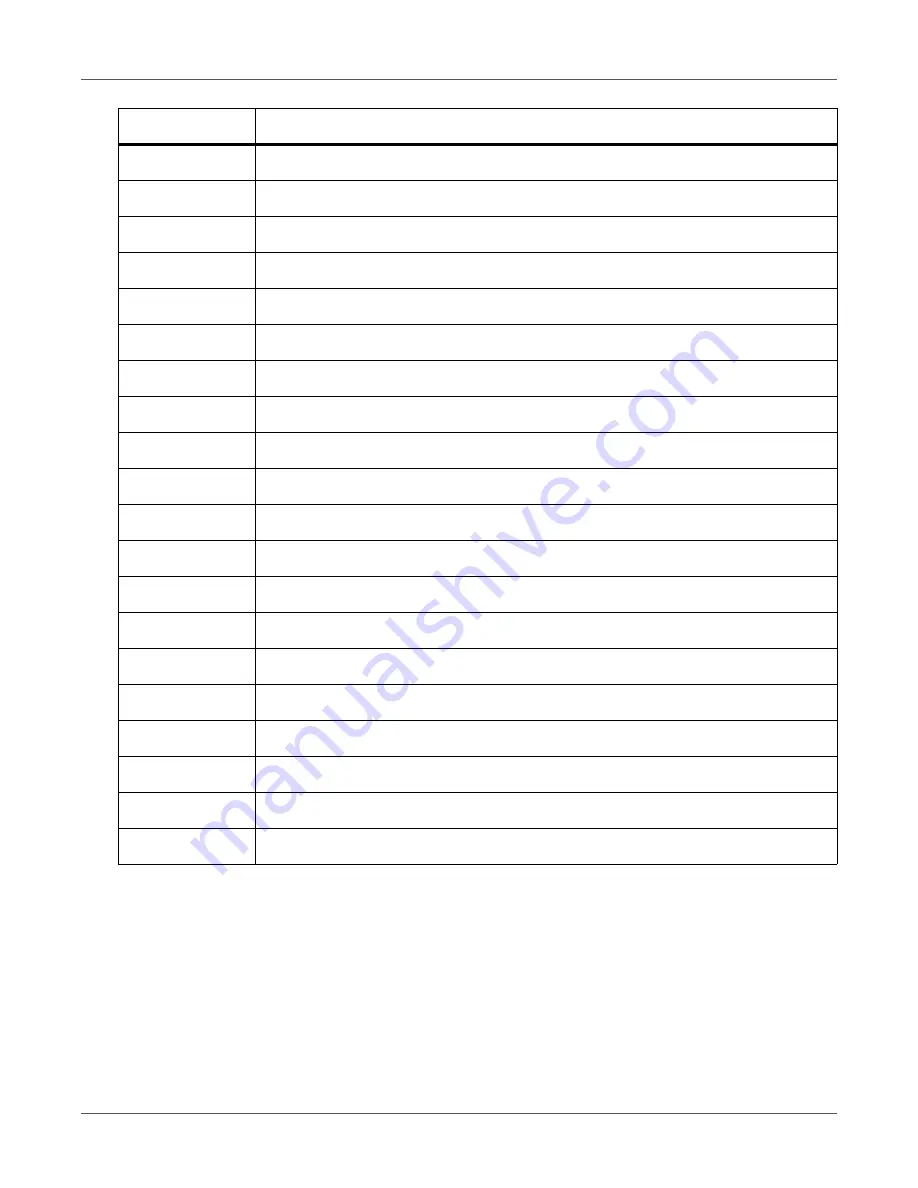
E
RROR
C
ODES
[EN] English
154
K0553 Revision D
336
PT control sensor EEPROM write error
337
PS control sensor checksum error
338
PS control sensor diode ADC acquisition error
339
PS control sensor frequency acquisition error
340
PS control sensor EEPROM write error
341
LED IO expander initialisation error
342
Valve IO expander initialisation error
343
Power check initialisation error in external ready
344
Power check initialisation error in internal ready
345
Power check error in internal power level
346
Power check error in internal ready
347
Power check error in external ready
348
Internal CAN connection timeout
349
Software version mismatch
350
Power check initialisation external reset error
351
ERROR_DRIVER_PWR_INIT_EXT_MISC
352
Power check external reset error
353
Ps differential limit exceeded
354
Slave board synchronisation error
355
Switched from three channel to four channel controller
Error Number
Description
Summary of Contents for ADTS542F
Page 19: ...Chapter 1 Introduction ...
Page 30: ...DUAL HAND TERMINAL EN English 19 K0553 Revision D Figure 1 8 ADTS Touch Slave ...
Page 31: ...Chapter 2 Installation ...
Page 34: ...PACKING FOR STORAGE OR TRANSPORTATION EN English 24 K0553 Revision D ...
Page 40: ...Chapter 3 Operation ...
Page 114: ...Chapter 4 Calibration ...
Page 123: ...Chapter 5 Maintenance ...
Page 132: ...Chapter 6 Testing and Fault Finding ...
Page 152: ...Chapter 7 Specification ...