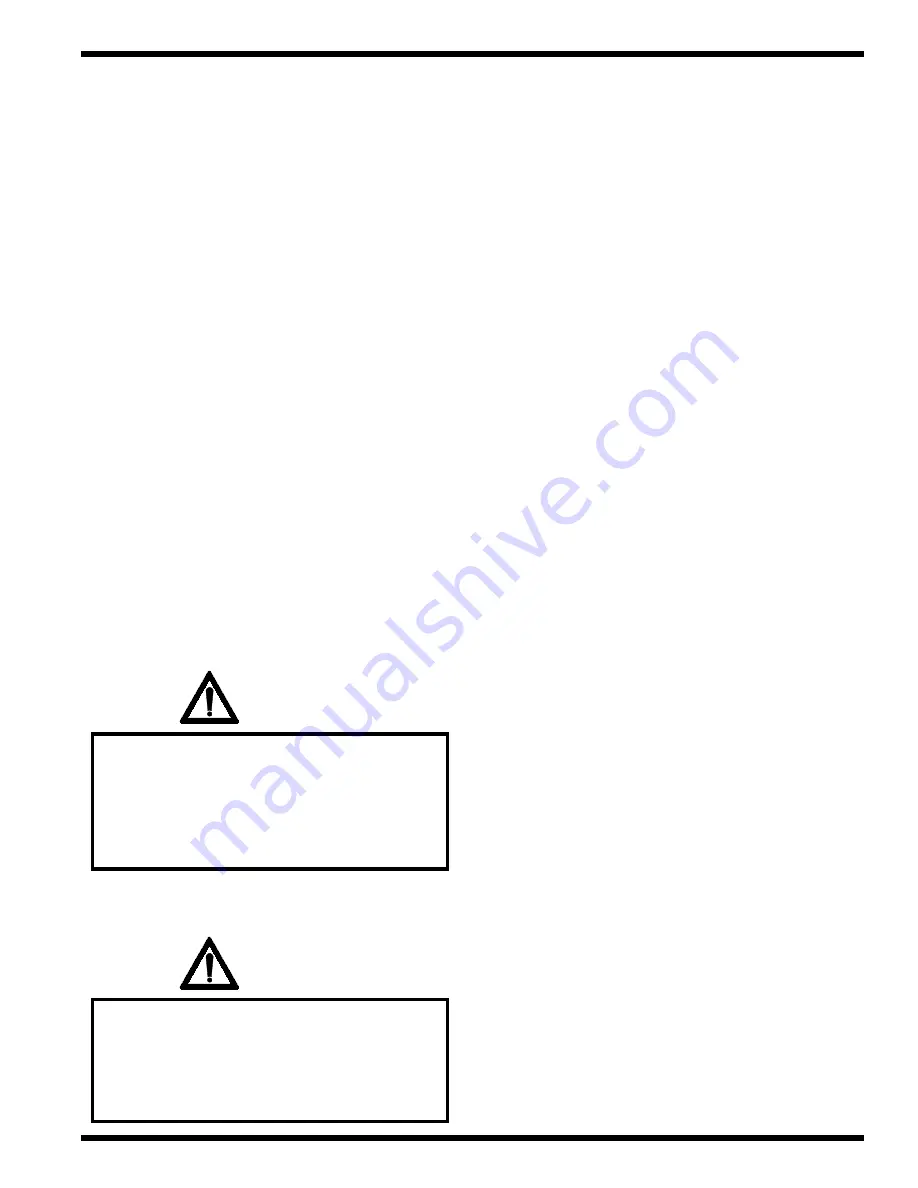
© GBC Films Group April 2000
Voyager Operation and Maintenance Manual
Page 1 - 17
Operations
4.0 OPERATION
Operating procedures given in this manual are
presented as suggestions for the operator’s consideration.
An operator experienced in the art of lamination may
prefer different procedures under certain conditions.
Your new GBC Voyager™ Laminator is a durable
machine designed for heavy work loads. By following
the procedures suggested in this manual and taking proper
care of your unit, you can be assured of years of
professional quality laminating.
This section will explain the controls of the
laminator, the feeder and the heating unit. Any control not
described within this section is done so intentionally. These
controls are not for operator manipulation.
W A R N I N G
To avoid injury to yourself or damage
to the equipment, please read and
understand the Operations section
of this manual before attempting
to operate the laminator!
W A R N I N G
Do not wear ties, loose fit clothing or
dangling jewelry while operating or
servicing the laminator. These items can get
caught in the nip and choke you or you can
be crushed or burned.
4.1 Laminator controls
1. EMERGENCY STOP ( E-STOP ): When pressed,
stops the machine from operation, raises the heating roller.
2. EMERGENCY STOP RESET: When pressed,
resets the machine after an E-STOP has been pressed.
3. SHEET SIZE selector: Enables the operator to select
the sheet size ( Short / long ).
4. KNIFE/ KNIFE & SNAP selector: Enables the
operator to engage the knife only, knife and snap or neither.
5. JOG FORWARD: Engages the machine in a forward
direction for the duration of the press. When a safety shield
is raised, JOG FORWARD and E-STOP RESET must
be pressed simultaneously.
6. JOG REVERSE: Engages the machine in a reverse
direction for the duration of the press. When a safety shield
is raised, JOG REVERSE and E-STOP RESET must be
pressed simultaneously.
7. LAMINATOR STOP: When pressed, stops all
motion to the machine.
8. LAMINATOR START: When pressed, engages all
motion on the machine.