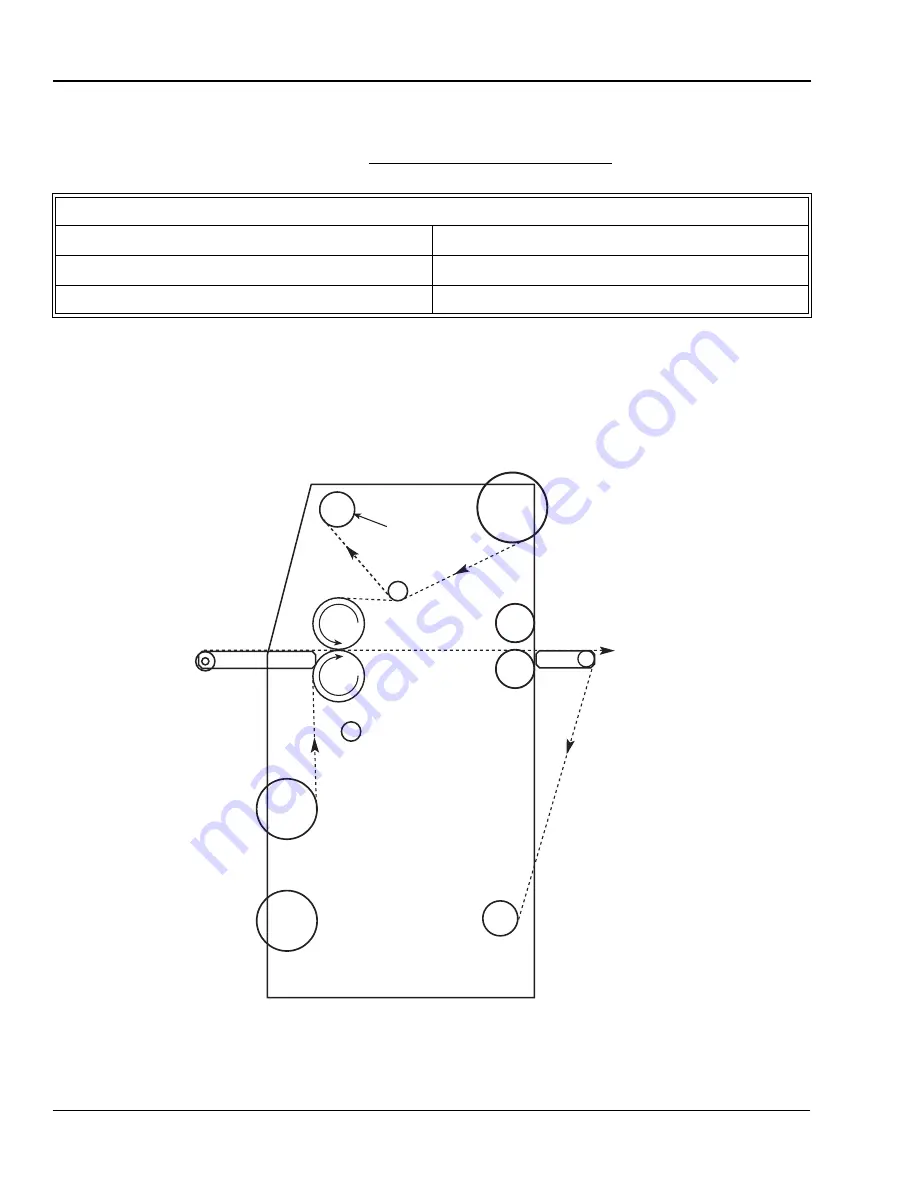
Operation
F-60+ Operation and Maintenance Manual
3-14
© GBC Pro-Tech 1999 April
352&(66&21752/&+$57$
Product: ______________________ Process: Cold Mount & Laminate (First Pass)
Date: ________________
352&(66&21752/',$*5$0$
Cold Mount and Laminate (First Pass)
FRONT CONTROL SETTINGS
Speed: 0-6 fpm (180 cpm)
Reverse/Forward: Forward
Roll Pressure: 30-60%
Top Heater: 105 °F (40 °C)
Cooling: Off
Bottom Heater: 32 °F (0 °C)
Pro
Gloss
Pro
Mount
Release
Paper
Rewind
Optional
Summary of Contents for 930-028
Page 10: ...Safety F 60 Operation and Maintenance Manual 1 6 GBC Pro Tech 1999 April Blank page...
Page 36: ...Operation F 60 Operation and Maintenance Manual 3 18 GBC Pro Tech 1999 April Blank page...
Page 44: ...Warranty F 60 Operation and Maintenance Manual 5 2 GBC Pro Tech 1999 April Blank page...
Page 46: ...Specifications F 60 Operation and Maintenance Manual 6 2 GBC Pro Tech 1999 April Blank page...