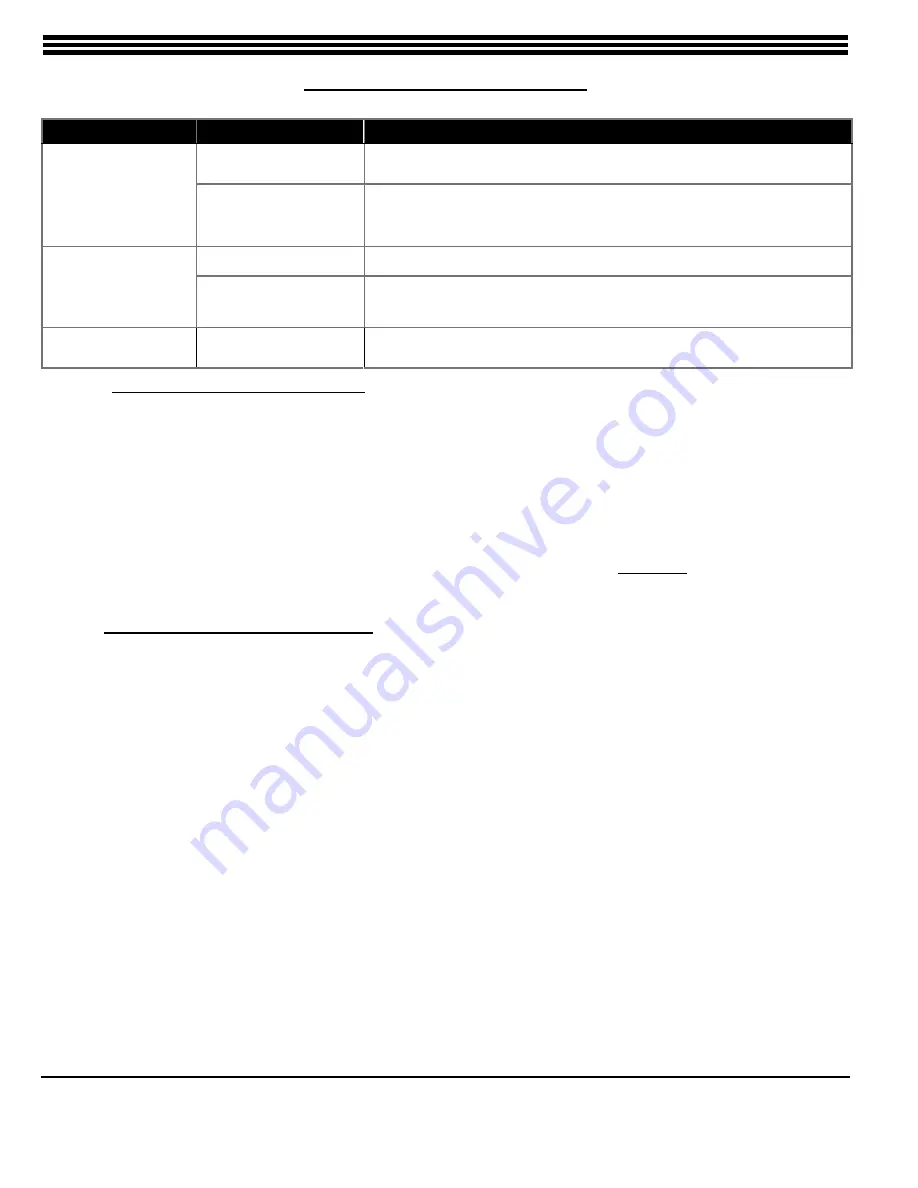
UNSATISFACTORY PERFORMANCE
If the engine governing system functions poorly, preform the following test.
Symptom
Test
Probable Fault
Engine overspeeds.
1. Do not crank. Apply DC power to
1. Actuator goes to full fuel. Then, disconnect speed sensor at Terminals C & D. If the actuator is still at full fuel - the
the governor system.
speed control is defective. If the actuator is still at minimum fuel fuel position - erroneous spped signal. Check speed
sensor data.
2. Manually hold the engine at the
1. If the voltage speed reading is 1.0 to 2.0 VDC; a.)
SPEED
adjustment is set above desired speed. b.) Defective
desired running speed. Measure the
speed control unit.
DC voltage between Terminals A (-) &
2. If the voltage reading is above 2.0 VDC; a.) Actuator or linkage binding.
F(+) on the speed control unit.
3. If the voltage reading is below 1.0 VDC; a.) Defective speed control unit.
4. Gain set too low.
Actuator does not energize fully.
1. Measure the voltage at battery while
1. If the voltage is less than 7VDC for a 12VDC system or less than 14VDC for a 24VDC system, replace the battery if
cranking.
it is weak or undersized.
2. Momentarily connect Terminal A &
1. Actuator or battery wiring in error.
F. The actuator should move to full
2. Actuator or linkage bringing.
throttle position.
3. Defective actuator. See actuator troubleshooting.
4. Fuse opens. Check for short in actuator or actuator wiring harness.
Engine remains below desired
1. Measure the actuator output.
1. If voltage measurement is within approx. 2 volts of the battery supply voltage, then fuel control restricted from reach-
governed speed.
Terminal a & B, while running under
ing full fuel position. Possible due to interference from the mechnical governor, carburetor spring or linkage alignment.
governor control.
2. Speed setting too low.
Insufficient Magnetic Speed Signal
A strong magnetic speed sensor signal will eliminate the
possibility of missed or extra pulses. The speed control unit
will govern well with 0.5 volts RMS speed sensor signal. A
speed sensor signal of 3 volts RMS or greater at governed
speed is recommended. Measurement of the signal is made
at Terminals C and D.
The amplitude of the speed sensor signal can be raised by
reducing the gap between the speed sensor tip and the
engine ring gear. The gap should not be any smaller than
0.020 in (0.45 mm). When the engine is stopped, back the
speed sensor out by 3/4 turn after touching the ring gear
tooth to achieve a satisfactory air gap.
Electromagnetic Compatibility (EMC)
EMI SUSCEPTIBILITY - The governor system can be ad-
versely affected by large interfering signals that are conduct-
ed through the cabling or through direct radiation into the
control circuits.
All GAC speed control sensors contain filters and shielding
designed to protect the unit’s sensitive circuits from mod-
erate external interfering sources. Although it is difficult to
predict levels of interference, applications that include mag-
netos, solid sate ignition systems, radio transmitters, voltage
regulators or battery chargers should be considered suspect
as possible interfering sources.
If it is suspected that external fields, either those that are
radiated or conducted, are or will affect the governor sys-
tems operation, it is recommended to use shielded cable for
all external connections. Be sure that only one end of the
shields, including the speed sensor shield, is connected to a
single point on the case of the speed control unit. Mount the
speed control to a grounded metal back plate or place it in a
sealed metal box.
Radiation is when the interfering signal is radiated directly
through space to the governing system. To isolate the gover-
nor system electronics from this type of interference source, a
metal shield or a solid metal container is usually effective.
Conduction is when the interfering signal is conducted
through the interconnecting wiring to the governor system
electronics. Shielded cables and installing filters are com-
mon remedies.
In severe high-energy interference locations such as when
the governor system is directly in the field of a powerful
transmitting source, the shielding may require to be a spe-
cial EMI class shielding. For these conditions, contact GAC
application engineering for specific recommendations.
Instability
Instability in a closed loop speed control system can be
categorized into two general types. PERIODIC appears to
be sinusoidal and at a regular rate. NON-PERIODIC is a
random wandering or an occasional deviation from a steady
state band for no apparent reason.
Switch C1 controls the “Lead Circuit” found in the
ESD5550/5556/5570. The normal position is “ON.” Move the
switch to the “OFF” position if there is fast instability in the
system.
Switch C2 controls an additional circuit added in the
ESD5550/5570 that is designed to eliminate fast erratic gov-
ernor behavior, caused by very soft or worn couplings in the
drive train between the engine and generator. The normal
position is “OFF.” Move to the “ON” position if fast erratic en-
gine behavior due to a soft coupling is experienced.
The PERIODIC type can be further classified as fast or slow
instability. Fast instability is a 3 Hz. or faster irregularity of the
speed and is usually a jitter. Slow periodic instability is below 3
Hz., can be very slow, and is sometimes violent.
If fast instability occurs, this is typically the governor respond-
ing to engine firings. Raising the engine speed increases the
frequency of instability and vice versa. In this case, plac-ing
switch C1 in
the “OFF” position will reduce the speed control
unit’s sensitivity to high frequency signals. Readjust the GAIN
and STABILITY 1or optimum control. Should in-stability still be
present, the removal of E1 to E2 jumper may help stabilize the
engine. Post locations are illustrated in
4